Tight deadlines and evolving specifications increasingly characterize electric vehicle (EV) and energy storage battery projects. This dynamic environment requires flexible and adaptable solutions, often iterated throughout the proposal development, project build, and implementation stages. Within these projects, one critical consideration is developing a strategy to mitigate the financial risks associated with heavily front-loaded capital expenditures (CAPEX).
Modular and flexible assembly production solutions are essential, as they can evolve in tandem with product and market demands. Considering the rapid rate of adoption in the industry and sustained variation of packaging designs and battery chemistries these systems will likely necessitate more frequent retooling to keep pace with technological advancements in the industry. We are actively observing large OEMs pivot to alternative form factors and battery chemistries, which will likely drive the need for major reinvestment in their assembly equipment.
Battery Assembly Proof of Principle Use Case
For instance, a customer with demand for both Battery Electric Vehicle (BEV) and Plug-in Hybrid Electric Vehicle (PHEV) battery production faced changing production targets and changing technical specifications due to evolving market demands. This scenario required adaptable and forward-thinking solutions for the customer’s battery assembly projects. Due to the changes in market demand between BEV and PHEV in different geographic regions around the globe, there is a growing emphasis on scaling production with equipment adaptability at the forefront.
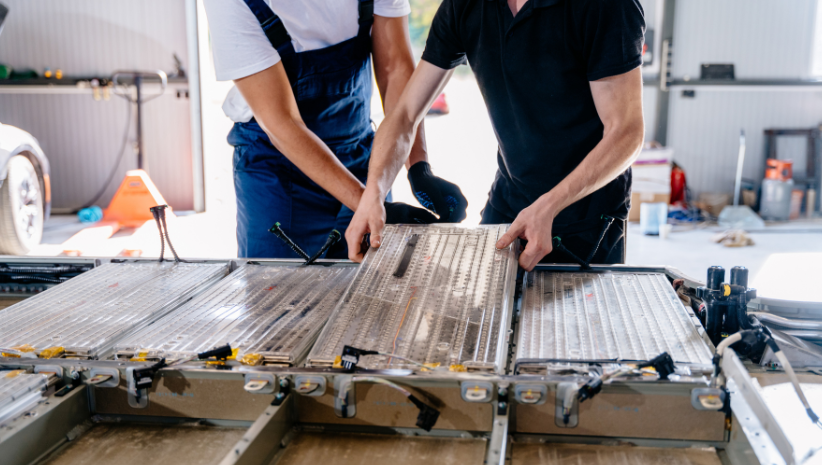
Whether customers are building EV or energy storage batteries, conducting a Proof of Principle (POP) study early in development can play a critical role in validating battery designs, managing changing specifications, and ensuring a smooth transition from ideation to full-scale production.
With POP studies, teams can mitigate risks, refine designs, streamline development, and improve project outcomes.
Understanding the Benefits of a Proof of Principle Studies
POP studies are used to demonstrate that a product, concept, or process is feasible and can be successfully implemented. When conducted early in the design process, POP testing can help optimize part and product performance, leading to scalable solutions and adaptable production strategies. POP studies provide a foundation for successful manufacturing, with far-reaching benefits that allow companies to minimize Total Cost of Ownership (TCO) across the product lifecycle.
The benefits of these studies most often take the form of Program Risk Mitigation or Cost Risk Mitigation.
Program Risk Mitigations
- Gain Insight Into Product Design Requirements: POP studies provide valuable insights into product design requirements that may not have been initially considered, enabling more informed decision-making early in the lifecycle.
- Collect Data Early: By collecting product data early in the design cycle, a POP study helps to refine and validate solutions before full-scale production commences.
- Reduce Production Capacity and Up-Time Risks: Early identification and resolution of potential production issues help to ensure smooth and uninterrupted production processes through scaling. In addition, this lays the foundation for improving equipment serviceability by identifying common failure points and content that will require regular preventative maintenance.
Cost Risk Mitigations
- Minimize Initial Financial and Resource Investment: This allows for early engagement in new programs, accelerating key milestones and reducing the risk of costly delays.
- Prioritize Manufacturing Production Requirements: A POP study offers early insights into these requirements, aiding in planning CAPEX investments necessary for successful program execution.
- Identify Changes Earlier: Driving potential revisions to production requirements early on can minimize cost and timing impacts downstream. In addition, it promotes conversations related to Design for Manufacturability (DFM) and Assembly that are often overlooked. This helps reduce unplanned costs driven by Change Orders later in the lifecycle.
Seizing the opportunity to obtain tangible learnings from physical products at any early stage in the product development cycle is critical to setting the framework for a successful program. Occasionally, significant financial investment early on is restricted due to ongoing changes in product design or lack of fixed market demand. However, it is important to remember that the benefits detailed above can be achieved with minimal investment.
Scaling Proof of Principle Solutions
Common focuses for any EV battery assembly project are electrical testing and leak testing, both in-process and end-of-line (EOL). These tests validate that the product meets the specified performance and safety requirements prior to moving to the next manufacturing stage or final installation into the vehicle. Designing scalable solutions for these testing processes is essential for EV Battery projects. The goal of any POP study is for the developed concepts and solutions to be effectively scaled to a production environment.
To start, utilize temporary bench-top setups or another similar approach to minimize CAPEX investment. Try to leverage industry-standard instrumentation equipment to validate product and production assumptions. Then, additional complexity and customization can be added to the solution to build a final concept. As the results of the POP study are collected, further iteration can be done, or, in some cases, a complete shift in technical approach is identified. Through this process, the requirements for the equipment are defined, along with the associated procurement costs, which can vary by order of magnitude. Providing an early definition of the costs will help in the alignment of project budget targets.
In addition to instrumentation equipment, scaling a POP study developed for a battery cell, module, or pack to a comprehensive production system demands a definition of repeatability requirements and refinement of critical design concepts such as tooling, fixturing, and connectors. Ensure process repeatability is at the forefront when evaluating scalability. This will drive important discussions on allowable test times, pass/fail targets, and operational expenses. Other critical design concepts mentioned above are also typically evaluated at this stage to better understand how the equipment will interface with the device under test (DUT) and what customization and complexity may be required.
Battery Proof of Principle Study Results
The EV and hybrid battery customer was able to leverage product development advances driven by the POP study to evaluate instrumentation hardware requirements early and laid the framework for scaling to full production capacity. In this example the appropriate battery impedance meter with the target measurement accuracy range and resolution was selected, and the production cycle time impact of simultaneously testing multiple battery cells was assessed.
The POP study provided a better understanding of the necessary process takt times to achieve specifications and helped the company determine production equipment requirements that met target volumes. This approach accelerated the overall program timeline, advancing initial milestones ahead of schedule and improving speed to market.
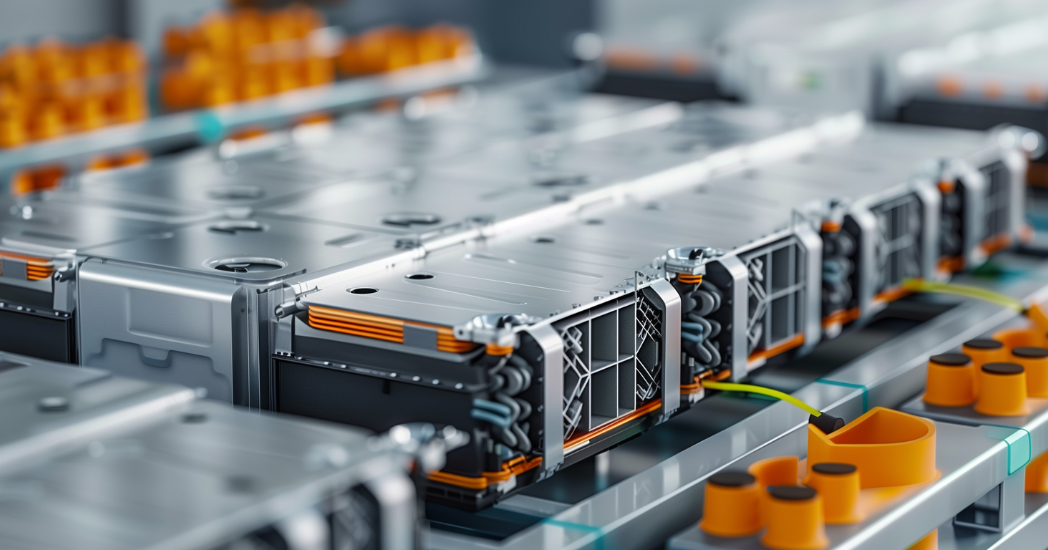
In another example, the execution of a POP study identified requirements for a low-throughput modular electrical test solution, allowing for initial product design validation and confirmation of specifications. Using the findings from the POP study, the proposed test solution was designed to accept a wide range of product types. This provides the company with enough flexibility for the expansion of capabilities with minimal impact on the system. This solution was scaled to a complete production system to help the factory meet market demand.
Preparing for Market Growth with Scalable Solutions
The value of investing in a POP study is quickly realized in the EV Battery market, especially when you consider the rate of technological advancements, development, and changing production volumes. The ability to review product requirements and validate or correct assumptions that drive CAPEX investment and Total Cost of Ownership (TCO) should not be overlooked.
The complexity and scale of battery assembly and test projects will continue to grow as the market share of EVs increases around the globe. Investing in production solutions now is crucial in preparing for potential market growth. The question to ask is: “What tools can be leveraged to help position the business now to be ready to capitalize on the growing market demand of the future?”
Every project is unique. Allow us to listen to your challenges and share how proof of principle testing can launch your project on time.
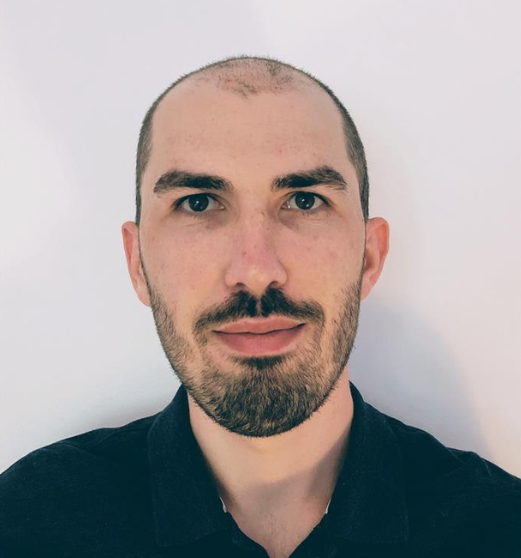
Patrick Tabis
Applications Group Lead
ATS Industrial Automation
Patrick helps companies across numerous industries with planning and deploying automation projects on a global scale. Patrick works with customers to optimize the technical design of production lines to drive operational efficiency.