Maintaining part and product quality in manufacturing presents a unique set of challenges, especially as production complexity increases and customer expectations rise. From minor imperfections to critical failures, defects can significantly impact production timelines, costs, brand reputation and increase a company’s liability. Every manufacturer should ask, “How confident are you in catching issues in production and mitigating them before they escalate?”
Addressing issues early is key to maintaining both product quality and profitability. The 1-10-100 Rule reinforces the importance of early intervention: preventing defects from occurring is far cheaper than correcting them, and both are less costly than managing failures after the fact. This applies to all industrial product manufacturing, from battery energy storage systems and nuclear components to consumer goods. Companies can significantly reduce defects by identifying risks early in the production process. Below are key strategies to improve quality and ensure defect-free manufacturing.
1. Design for Manufacturability
To reduce defects, adopt a Design for Manufacturability (DFM) approach. DFM involves designing products in a way that makes them easier to manufacture. By analyzing factors like production methods, assembly requirements, materials, tolerances, and machinery, teams can identify issues early and resolve them before they affect part assembly and product manufacturing.
For instance, you may need to make slight adjustments to part tolerances, so they are more forgiving during assembly to avoid misalignment or breakage. Conversely, tightening tolerances for features that need to be highly repeatable can ensure consistency across a production line. Or incorporate location features in the product design to help guide and orient parts, making it easier to handle and assemble components to reduce errors.
At ATS Industrial Automation, our experts have a DFM mindset. We can apply this to all process stages – discovery, requirements, design, integration, testing, and final production line. Our experts work with customers to detect and fix problems throughout the design-to-manufacturing process. This results in an efficient and cost-effective assembly line process that produces high-quality products that meet function requirements.
2. Conduct Proof of Principle (POP) Studies
Introducing new processes or automation requires Proof of Principle (POP) studies to simulate and verify how a product will behave on the production line. Using digital twin technology, engineers can create virtual replicas of machines, test performance and emulate components on a virtual manufacturing line. Teams can analyze, debug, troubleshoot issues, and test change requests virtually before construction begins.
This is especially beneficial for first-of-its-kind automation or new products, where potential defects can be identified and addressed during the simulation stage. POP studies help fine-tune processes, ensuring the final product meets quality standards.
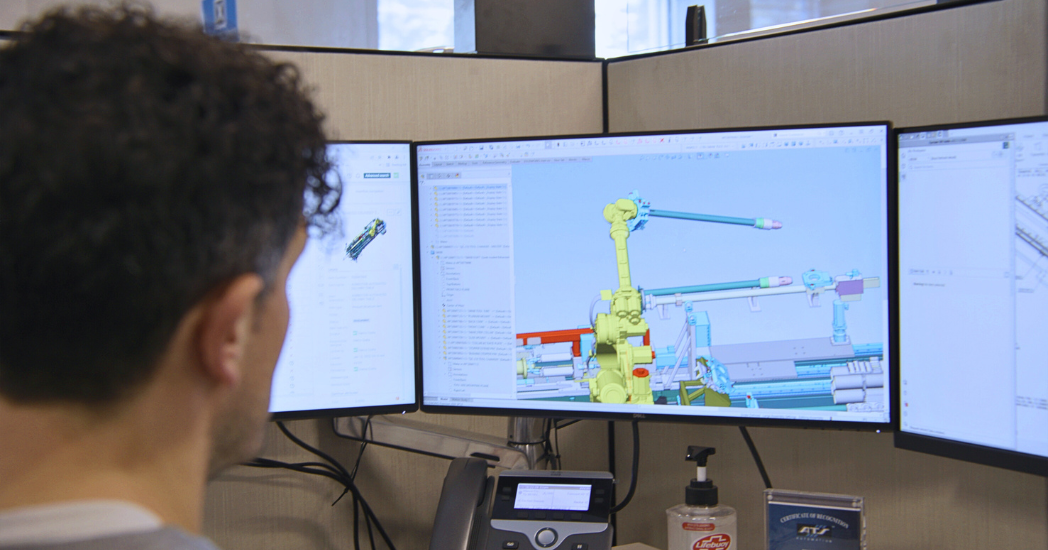
3. Test Early, Test Often
Frequent testing is critical to catching defects before they cause costly recalls or delays. The earlier and more often testing is conducted, the more opportunities there are to prevent issues from escalating. Depending on the product, testing might involve material handling, component validation, end-of-line tests, or simulations of tool interactions. Depending on the product requirements, you may need a combination of electrical, mechanical, fluid dynamics, or BUS communication tests. Factory Acceptance Testing (FAT) is another vital step, verifying that production systems can consistently meet required functionality and quality standards before the equipment is installed.
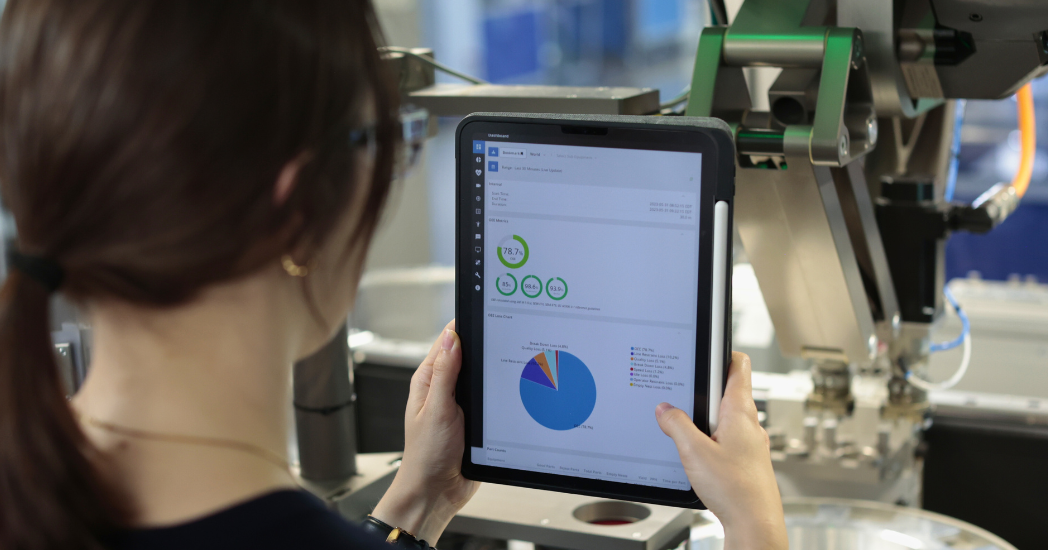
Manufacturers can work with their automation partners early in the design process to develop assembly testing systems and validation programs that are robust, reliable, and customized to your requirements.
Not only does ATS provide testing systems and equipment, but our experts also work with customers to design and map test methodologies and specifications to help validate and identify issues early in the manufacturing process.
4. Prioritize High-Risk Processes
While testing is crucial, it’s not feasible to test every process in great detail. Therefore, manufacturers must focus on the processes that pose the highest risk. Conducting risk assessments early in a project can help identify areas where defects are most likely to occur. High-risk processes should receive extra attention during testing, ensuring that potential issues are caught and addressed.
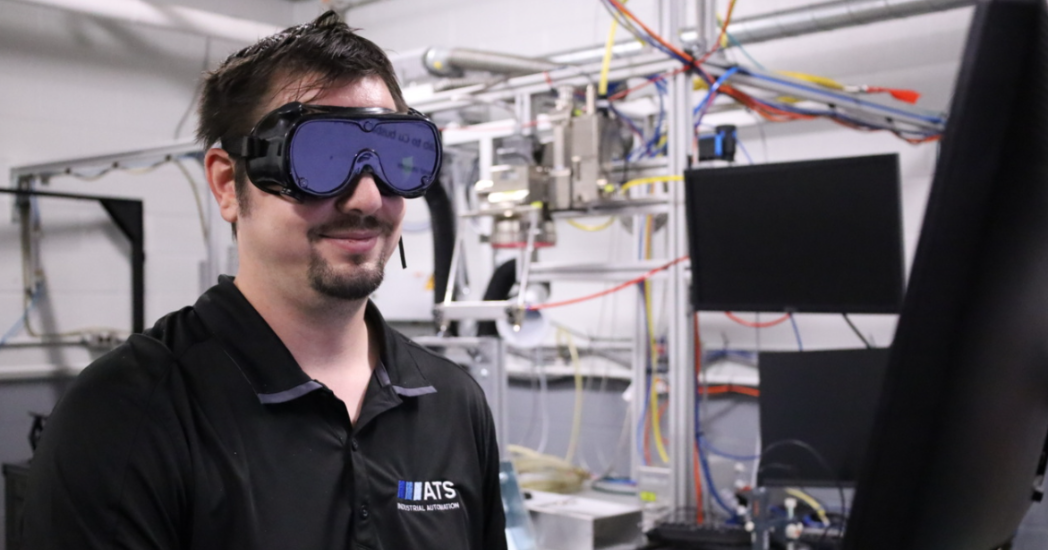
For example, processes like laser welding are often considered high-risk. At ATS Industrial Automation, we invest in specialized laser labs where welding parameters can be fine-tuned before they are applied to the full production line, reducing the chance of defects in high-risk processes.
5. Anticipate Changes
Late-stage changes to product designs or specifications can lead to rework, delays, and an increased risk of defects. By collaborating with automation partners early in the design process, manufacturers can identify and address potential challenges early. Any change request can be implemented into the manufacturing process with minimal disruption. Strong communication between teams ensures that changes are managed smoothly, minimizing disruptions and preventing defects from creeping into the final product.
Proactive Strategies for Success
Avoiding product and part defects requires a holistic approach, including DFM, early testing, risk assessment, and clear communication. The earlier manufacturers identify risks and potential issues, the better positioned they are to deliver high-quality, defect-free products when they start full-scale production.
By investing in these proactive strategies, manufacturers can reduce costs, improve quality and production uptime, and limit their risk.
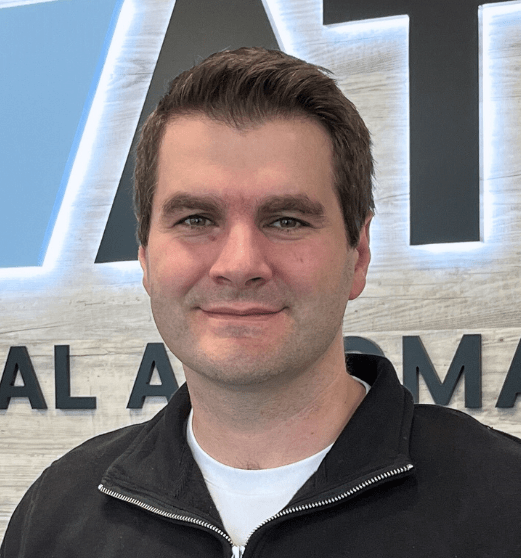
Ken Aarts
Manager, Controls Engineering
ATS Industrial Automation
Ken has helped companies across numerous industries automate and optimize their assembly and testing lines. Ken specializes in configuring control systems for the expansion and optimization of production lines and to drive operational efficiency.