As one of the most important outcomes of battery production, battery quality is the result of not only the assembly and testing processes of the physical production line, but also the interconnected data management systems that document how it all comes together. With the mandatory adoption of the Battery Passport in Europe by February 2027, it will become increasingly important for battery manufacturers to maintain a comprehensive record of the battery’s provenance, production history and quality tests.
One of the Battery Passport requirements is a supply chain due diligence policy that outlines sustainability practices and operational transparency. For battery manufacturers, this means battery quality begins with provenance, long before production begins. Suppliers of raw materials will need to provide visibility into how they source the materials, manage data, protect systems, and manage controls for each battery. This will require significant systems that can record all of this information and associate it with individual battery units, preferably in real-time and eventually, available to the consumer who buys the vehicle in which the battery is placed.
One of the systems enabling this could include a Manufacturing Execution System (MES) that tracks, documents, and controls the manufacturing process of goods, from raw materials entering the factory to finished product. The MES is the foundation for manufacturing operations, linking the production floor to enterprise management systems by providing insights about production volume, scrap rate, OEE, etc. But an MES is only as good as the data that feeds it – including battery assembly test results from the production line.
Building on a Foundation of Quality Assembly Processes
The assembly process is what people think of first in terms of quality – and quality starts with the battery cell. At the front end of the assembly process, automated high-speed testing and sorting of barcoded cells, including detecting and rejecting failed cells, needs to occur quickly and accurately. These tests focus on the cell’s internal integrity, namely its capacity, charge, voltage, and internal resistance; for example, AC/DC Internal Resistance (IR), Cell Self Discharge, HiPot DW Insulation Resistance, and more.
Now, multiply this by thousands. A single EV battery pack can have 6,500 cells, requiring 13,000 individual zero-gap laser welds. First, the intelligent laser processing and welding system will detect and align parts within expertly designed welding clamps or horns. Then, using a combination of robotics, vision monitoring sensors, and laser welding, it will verify the depth of each weld in real time, issuing an immediate weld pass or fail result.
Given the different sizes of battery modules, and the intricacy of putting them together, battery modules require numerous tests to assess the discrete connection points among cells, and their integrated performance and durability. More tests validate the physical robustness and safety of the module, including temperature, weld and busbar resistance, leak tests, mechanical vibration, and Battery Management System (BMS) tests (the latter is also tested for battery packs).
A BMS is a mandated component of a finished EV battery, where it monitors and manages the temperature, current, and voltage of the battery during charging and discharge. It determines the State of Charge (SoC) and State of Health (SoH) of the battery, managing its internal operating conditions to maintain performance and safety and prolong battery life. SoC and SoH Estimation Methods such as Open-Circuit Voltage (OVC) and Electrochemical Impedance Spectroscopy (EIS) tests are essential for evaluating the operation of the BMS within the battery pack before it leaves the production line.
Managing Battery Test Requirements and Protocols
Knowing what tests to conduct is just one part of the quality equation; knowing the complex requirements and protocols for those tests is another. Test results are measured against parameters and pass/fail thresholds that are configured and managed with software such as the ATS Test Executive Suite.
These are defined by the battery manufacturer to meet the specific measurement and control requirements for each component and process of the assembly process, as well as the finished battery module or pack. Traceability product test reports, process event logging, version control, and other data management features provide a detailed record of the battery’s test history.
However, the accuracy and repeatability of test results depends on the calibration of test equipment and verification and validation of the test protocols. The ATS Test Executive Suite, for example, has built-in diagnostic and analysis tools to automate sensor calibration and provide statistics on process capability index (Cpk) and gauge repeatability and reproducibility (GR&R) studies for detecting variability of measurement systems.
Information from the ATS Test Executive Suite can be integrated with an MES via a common control architecture. In effect, this data integration closes the loop on the battery’s production from raw material to finished (tested and validated) product, with that traceable history housed in the MES, SCADA, QMS, and other manufacturing systems as required.
Every battery project is unique. Allow us to listen to your challenges and share how automation can launch your project on time.
Getting Data-Ready for the Battery Passport
All EV and industrial batteries will require a Battery Passport in Europe by February 2027. This standardized and regulated digital record that must include information about the battery’s durability, performance, SoH, manufacturing site(s), supply chain due diligence policy, and more. Information that was documented during the procurement process, and collected throughout the battery’s production and testing lifecycle, will comprise a majority of the Battery Passport.
In particular, the battery’s durability, performance, and health are key indicators of its overall quality, which is tied directly to its assembly and testing, and the traceability and management of those test results. It underscores the importance of having interconnected assembly, testing, and data collection processes and workflows, and robust yet flexible data management systems that bring it all together.
With 45+ years of automation experience, and expertise in dozens of testing services and solutions, our team of assembly and test experts can help you build a comprehensive end-to-end battery production program. Let us know if you’d like to talk about your unique situation.
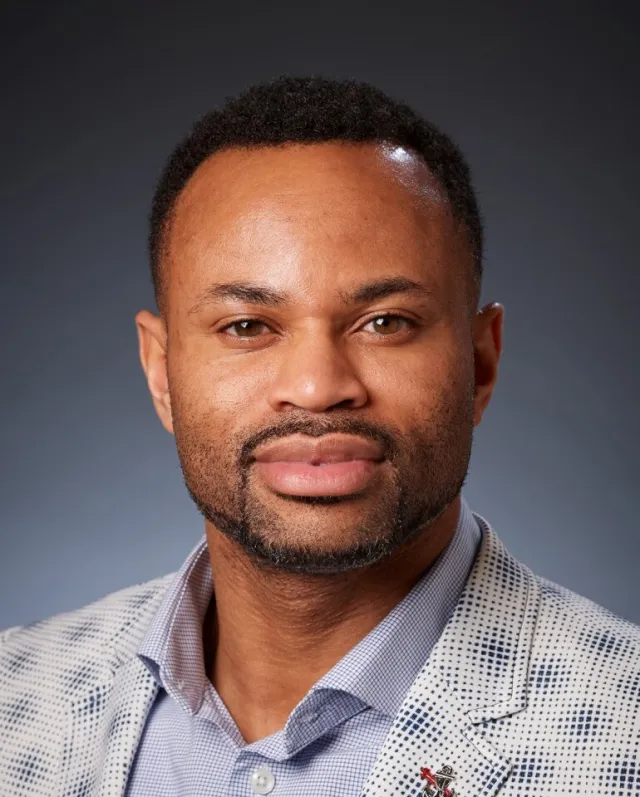
Peter Adeyemi
Sales Account Manager
ATS Industrial Automation
Peter has helped companies across numerous industries to automate and optimize their testing and validation processes. Peter works with customers to configure testing systems to build and scale production and drive operational efficiency.