When it comes to energy production, few sources rival the efficiency, reliability, and sustainability of nuclear power. Yet, as the global demand for clean energy continues to surge with the goal of meeting net-zero emissions by 2050, some existing nuclear infrastructures face the challenge of aging facilities. Enter nuclear refurbishment— with increased government support and funding, this is a crucial process aimed at extending the lifespan and enhancing the performance of nuclear power plants.
However, nuclear refurbishment is not without its complexities. It involves intricate tasks, meticulous planning, and stringent safety and quality measures to ensure the integrity and efficiency of the plant. In this dynamic landscape, automation emerges as a transformative force, working with the trades to revolutionize the way we approach nuclear refurbishment.
Enhanced Safety and Efficiency with Automated Tooling
Automation, with its advanced technologies and intelligent systems, holds the key to streamlining operations, optimizing efficiency, enhancing safety, achieving consistent quality, and mitigating risks in nuclear refurbishment projects. From robotic inspections and remote tooling, such as the Automated Delivery Table at Bruce Power, automation offers a range of solutions to enhance safety, reduce downtime, and create reliable and repeatable processes that optimize performance and maximize the return on investment in nuclear facilities.
A First of a Kind for Bruce Power and ATS Industrial Automation
Now on the next phase of the MCR project, the Auto Calandria Tube Install project (AutoCT), set to be deployed early fall 2024, highlights the latest innovations supporting nuclear refurbishments. A first of its kind for both Bruce Power and ATS, the AutoCT project, marks the first time that a robot will be used to install critical CANDU reactor components. The installation process involves installing the calandria tube into a lattice site, verifying correct positioning on both reactor faces, then rolling the calandria tube, finishing with a leak test. During the installation process, a combination of custom designed tooling and a 6-axis robot are used reliably by trade operators remotely at the Re-tube Control Centre to install 480 calandria tubes in each unit.
This project is expected to not only improve radiological safety for the trades, but also enhance the quality and reliability by using predictable automated tools for what were manual tasks. Not only had this never been done before, but the project needed to be completed in a short time frame to help Bruce Power maintain their overall refurbishment schedule.
Partnering to Meet Net-Zero
As a world-leading automation company, ATS was able to leverage our breadth of knowledge from across multiple industries to bring this new innovation to light for Bruce Power. Using technologies such as the digital twin, allowed ATS to rapidly design and test the solution in an accelerated timeframe before the equipment was delivered to site.
Watch the full video here to learn more about the innovation AutoCT project between ATS Industrial Automation and Bruce Power.
The partnership between Bruce Power and ATS highlights the commitment from each company to continue to push the nuclear industry forward with new innovations as a means to continue to supply clean, dependable energy well into the future.
Talk to a member of our Nuclear team to learn more about how our automated solutions can help solve your refurbishment challenges.
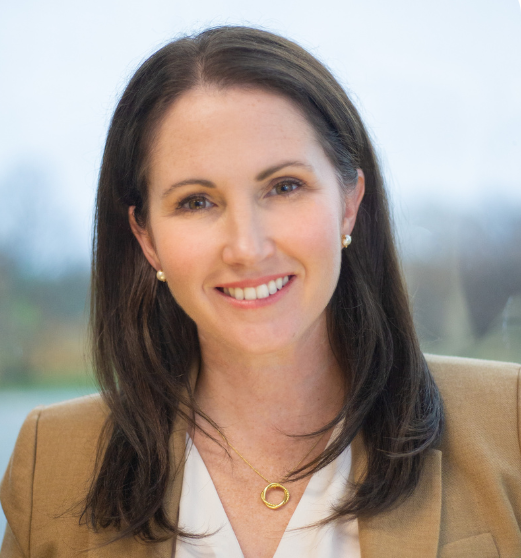
Emma Hauch
Director of Business Development
ATS Industrial Automation
Emma has helped nuclear facilities optimize and automate processes for over 18 years. Emma works with nuclear facilities to configure services, systems, and digital tool strategies to significantly reduce schedule, improve safety and quality, reduce human error, and improve overall performance.