October 4, 2021
EV Battery Modules are evolving at a rapid pace. Chemistry, packaging, welding, material handling, software, and more make managing and testing EV batteries complex. Efficient battery testing must also evolve to support the growing demand and technology advances. Flexibility, modularity must be built-in, and the industry approach to battery module testing needs to shift its approach dramatically.
In this recording from the ATS Virtual Expo 2021, Jack Porter explains how:
- Testing a battery is not just ‘testing a battery.’
- Why breaking existing battery production assembly and testing biases is critical to success.
- Pathways for successful battery assembly validation.
Watch “The Key Element: EV Battery Testing” Webinar Now
Speaker
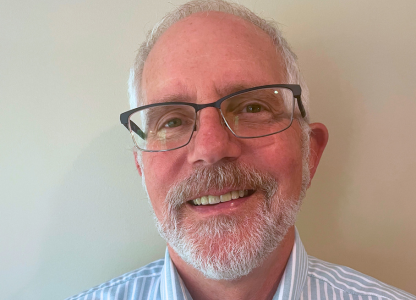
Speaker
Jack Porter
Applications Engineer Technical Specialist; ATS Industrial Automation.
Transcript
My name is Jack Porter. I am an applications engineer at ATS. I have spent almost my entire career developing production test processes and equipment and systems for leading OEMs. Over the last decade or so, my concentration has been on the electrification of just about everything. Most notably, most recently, this has been with respect to electric vehicle powertrains, power generation, power conversion, and power storage. And over my many years of production testing, I have been through a few battles, got a few scars to prove it. And I have learned a few things. Two of my favorite things that I have learned is first, Ohm’s law really works, and second, that the only constant is change; I know it is a cliche, but it is especially true today with respect to production, testing and batteries.
The Impact of Constant Change
Today, we will talk about all this change and ask:
What does it mean for the electric vehicle market?
And what does it mean for what we need to do for production testing?
If we look around at the press releases and trade journals, we go to different shows, we see exciting changes occurring everywhere and across a lot of different directions with respect to the electric vehicle market and batteries. We see changes in the baseline chemistries, in the end application usage, be it mobility applications or storage applications or range extension. We see changes in the packaging, how these products are put together, what is their form and function for their end use, the system connections in terms of what the interconnects are, what needs to happen to these in order to integrate them in terms of what their application is, and ultimately, the charge and discharge requirements, because that is what the endgame is here, in terms of how we electricity-out in order to drive our application and how we recharge it. Question:
With battery technology improving at this rapid pace, what effect does this have on us?
Well, we have a convergence of technology and timing. We see that technology is changing all over, the timing is based on the demand that we are seeing today. Let us look.
A typical battery assembly process might take two to three years from the project start, with a request for proposal (RFP), to a full production ramp up. This timeline is too long for the existing demand, and the changes that are happening would make that project a moving target if we actually took that long, based on the evolutions that are occurring today.
ATS looked at how to transform existing manufacturing spaces, or spaces that will be produced, to reach full production in a shorter timeframe, but not being able to rely and leverage on the mature technologies and processes that we had in the past. The technologies being used to transform existing manufacturing spaces are not mature technologies, and new processes are being developed to implement them.
Due to this pace of high speed, we need to look how to adapt and how to deploy this within our organizations. Question:
What does it mean for production testing, to ensure our success?
A shift in perspective is needed. We can look at what we already have, our organizations, our capacities, and what limitations we have there. We have lots of good people who work for us, with lots of knowledge and the ability to scale up or down as required, based on the products that we are looking to produce. So, we need to focus on the areas we must learn and modify and adapt with that.
If we look at how we interact with other companies with respect to suppliers or end users, we must ask:
What teams do we have in place?
How does that work today?
How can our teams handle something when things are changing quickly?
The changes will have a ripple backbone, both from between tooling suppliers, between manufacturers and between end users; we need to look at this and understand this as a background as we go, to adapt touch processes we are going to deploy.
Let us take a few minutes and look at those parameters and processes. These things are evolving. If we walk through some of the change areas, we can see that chemistries are changing, packaging is changing, and monitoring is changing, which is in this case mostly intelligence in terms of what we can do, what do we have to monitor as part of the end-use for this product, what we can monitor in terms of producing this product.
We put this on top of our short timeframes, which means that many times we had to adapt the laboratory and design methodologies directly into the high-volume production process. This can present some real difficulties in separating product design validation parameters from production testing parameters. So, we must ask:
What are the parameters that count for us to ensure that we built the battery correctly, not necessarily that the battery was correctly designed?
We look at some of the existing battery test parameters.
We have some defacto standards with respect to the state of charge. Key considerations are:
Where is the battery?
How much current capability does the battery have?
The state of health is a longer-term thing that we look at, to ask how the battery is performing. Is there any degradation occurring? If yes, how much?
What is the expected lifetime of the battery?
What can I do to maximize that lifetime?
What is it that we test for to determine those things? Leak tests.
We have a lot of thermal processing within these parts. Typically, when you have any kind of power moving around, there are new inefficiencies that generate heat; we certainly had that within the battery pack. And, we have a lot of systems in place for trying to manage that energy. Where are those and how many are required is kind of unique and what we need to pay attention to.
If we look at these changing conditions, we must figure out how we are going to handle them while doing a design and training system. For example, on the slide, we show just some of the changes across the electric vehicles over a short time. We see that some functionality comes and goes, interconnects are changing, and this is what we are going to have as we go to walk through and design our test systems.
We look at these products and end-of-line testing. The end-of-line testing says, ‘ship the product, it is good, it is ready to go to its intended use.’ These products are rather large, bulky, and expensive and we cannot succeed if the only test we do is at the end of the line. We must look at in-process control testing.
In-process control testing is going to result in a greater first-time capability at the end of the line and will identify issues or defects in the part sooner, earlier in the value stream, providing feedback, which we will use to correct those defects in the build process, ultimately minimizing scrap and rework while maximizing our uptime and overall equipment effectiveness (OEE).
The in-process test enhances the end-of-line test; to succeed you must have both. A key way to deal with the convergence of battery timing and technology is using the same test equipment across the line. Another good way to do this would be to have a single point of contact for all test functions, and dedicated engineers who will understand the part to its build process, ultimately leading to a deeper understanding of the part characteristics by all involved with this line.
“A single company is your best bet for supplying both your in-process and end-of-line tests.”
Jack Porter,
Applications Engineer Technical Specialist; ATS Industrial Automation
ATS does both in-process tests and end-of-line tests. It is very important that we do the in-process testing and the line, but the challenge is to find the right locations and procedures for that test. ATS is here to help you do that.
The place to start is to look at what is our part process, what is the part, how it is going to be built. We must be keenly aware to break any biases we might bring from previous programs, especially if we are coming from a place that does not deal with some of the uniqueness of a battery product.
The first thing that always impresses me is the number of parts that are involved throughout the process. When we start, we have something, and we are processing parts at a per second rate. We start out with pouches or cells, and we need a tremendous number of them to make up a completed battery.
We start out with thousands of them in a product and that means we need to be testing thousands of them at the start. As you move down the assembly process, these products are highly modular, built up little packs or sections, or modules, that consist of some number of cells or pouches or energy storage devices. Maybe it is three hundred or five hundred per section or module. Now, our rate that we need to process and run tests on starts to slow down; we now look at the number of seconds per parameter we are going be dealing with. When we get to the end, we have a single completed pack, and we are looking at maybe minutes per part. Not only do you have to look at the quantity of parts, but the intermingled processes.
Not all these processes are purely discrete processes. We start up at the battery formation end and we have processes that go on, processes that could take hours or days to complete, and they are not necessarily very active, but might be kind of passive once you control for environmental factors. Or maybe there is just some monitoring that we are doing on the part. Then, as we go down, we might have some cure time for some sealants or some thermal materials; we plan around this part. And so, we kind of get this very high, very quick going and then we have these interleaved in there, where we have long periods of time when the part is not actively being operated on per se. Additionally, we are talking about acting on the part as we go down, and we have part handling that changes; we start out at the beginning of the line with something that is very small and light, and at the end of the line we have something that is very large and heavy.
Parts connections change. If we look at testing across for these parts, we are testing the same physical quantities as we go down the line. We have different connections for doing this; we have high-voltage DC connections, typically more towards the end of the line as the voltage just gets built up, and we have low voltage DC connections that are usable for controlling per charge discharge. Also, we have different fluids that are placed into the battery, that we are using for the thermal materials or adhesives. Finally, we have physical changes in terms of the form factor of these connections, so we must look at this with respect to our tests. We look at the part connections at the beginning of the line, they tend to be very dense and very small areas to which we are connecting. As we go down the line, the number of channels we need to connect to starts dropping, but the connection size starts to increase. So, we get this continual flux that goes through. Our key today is to figure out how to handle this with our test equipment, our test connections, to make this easy, and something that can handle the adapting changes.
Not only do we have these physical changes going on, the part also was increasing the amount of port power that it is storing. This is a stored energy device and as you go down the line the amount of stored energy sitting in front of you is increasing. We look at all these connections, we must ask:
Do I do this manually until I do this automated?
Can I physically do it manually?
Perhaps we look at being on the line and we are in very small, very tight connections to be made, so perhaps we cannot do that automated, but maybe some tooling is needed to do that. Historically, we would take low-volume production or pilot builds and do that manually, due to the capital expense, and then we go to automate it when we ramp up production volumes.
With the rate and demand that is going today, we need to be able to plan how we can flex this, how we can go from manual to automatic or baby-straight, to automatic or manual tooling that is adapted and ready to plug into automation. To answer these questions, we have to understand what the tests are.
Testing
Let us look a little deeper at testing.
In the production of electric vehicle batteries, battery testing is not just testing a battery, the battery is just one element. This is a complex system. We have a lot of assembly validation and these are things that sometimes people consider them tests, and sometimes they are, and sometimes they are more validation that the part was put together. There is usually an overlap between these.
If we look at what we have today, there is a wide range of existing technologies that we can use for many of these functions, but perhaps applied to some different scenarios than what we are used to. Some notables would be welding. How do we make contact and define non-rigid structures earlier in the process that might be interconnected up and become stiff later in the process? Additionally, we are going to have some technology crossovers, perhaps from other industries.
So, we look at the different things we are doing for validating the assembly, we might want to look to the electronics industry where they are used to high-density part placement in interconnects. We may want to look to the chemical industries for what they do with respect to electrochemical impedance spectroscopy for determining what we are dealing with. We look at the dispense of chemicals and how that occurs. When we look at this, we will have a lot of things that will be on the line, and we must determine what is required for measurement versus just validation. As we do this, I want to point out that there may be some safety issues associated with this part being active, that might preclude some simple solutions that we think we might be able to use.
So, looking at our testing deployed across the various different systems on the battery, this diagram has the assembly validation type systems color coded in orange. And these may or may not have data associated with them. Usually there is limited data, sometimes it is as simple as something is there or not there or something achieved a specific measurement. The things that are in green are things that tend to have a more detailed measurement capability, which I would define as having more complex analysis, greater accuracies, perhaps some inter-variable data analysis or some stimulus and measurement response.
Now, if you look across the different tests that we do on this, some interesting things occur. We talked about how the part is built, it starts out small and gets larger at the end. And this is similar for the measurements as well. We said we have the comparable measurements physically in terms of the physics going across voltages, currents, that kind of thing. And as we look at what we are doing in the production line, we see that the magnitudes of our measurements are going up as we start out. We start out small at the beginning of the line with single digit voltages and currents, and by the time we get to the end of the line, we have increased by three orders of magnitude. Is it possible we can get some test equipment that can handle this range? That depends on the accuracies that you need, based on your product and where its capabilities lay.
Additionally, for structural integrity, we have looked at that a little bit on assembly validation. But in this case, the structure may not just be, and typically is not, just for protecting the part, it is also part of the electrical system we use for binding and for isolation. So, we probably need to test that as well, to prove the voltage correctly. We can do that in our assembly validation. But then we need to electrically verify with a test that that is indeed the case.
Leak tests are key. There is almost always a coolant or fluids associated with cooling these products. We charge and discharge large amounts of power, and as efficient as these are, most of the power that does not get converted properly due to inefficiencies turns into heat. So, when you look at the leak tests on this, we usually have cooling channels, and that may go to the modular portion of this where we have our different sections. And we probably want to test those, when we get a section complete before we put it together in a pack, to make sure within a given section we have no problems. Then, as we interconnect a bunch of sections, we are going to need to leak test to make sure that the interconnects between sections are correct. When we finally get to the pack, we need to make sure that the connections from all those sections to the outside world is correct and does not leak.
Additionally, in terms of leak testing, not only do we want to leak test the coolant channels, we also want to make sure that the pack enclosure does not leak. And this would be to make sure that any gases that are contained within are only outgassed as appropriate, or that the part is protected from any environmental considerations, in terms of where it is going to be used and its end application.
Using Inherent Intelligence
A key element about these parts is that they are smart parts, and we find that we have some intelligence on them with respect to battery management systems.
We typically find these down at the section level. So, we have something that is monitoring a section, some number of batteries in terms of their actual voltages, perhaps the resistances, some charge management structure for allocating the distribution across and maximizing life. And we want to test that at the section level, we want to make sure that is all working good at that point in time.
Some key things to look at is, can I use that information, that resident intelligence, as part of my test to generate data? You are going to get status information and diagnostics information and we are going to want to incorporate that into our tests. Of course, we must go through and prove that our intelligence is not lying to us and it is giving us good data first. Once we have proven that, then we can use all that data as part of our test sequencing and part of our stating that the part is correct.
As we go from the sections, we come up to the overall pack. Usually, there is a communications architecture of between the sections, up to a battery management system. And so, similar kind of considerations we talked about for the sections, we want to do that up at the top end with the battery management system. The battery management system typically will also have some interface for whatever are the end applications, and we need to test those as well.
Some notables would be the safety interlocks that are associated with this. So, we look at all this and we have to understand, and we have to try and figure out the impacts required to test this. And we look across the entire lane, and our best bet to impact is to look at using high-accuracy equipment across the board; this will allow for changes due to the evolving nature, to be able to flex up or down and still get us the data we need to say, ‘good part’ or ‘bad part.’
Scalability is highly desirable, and we can do that, maybe not across the entire production line, but certainly within sections, and certainly within battery packs. We can take the amount of power that we can put into a battery and demand power would take out of a battery, and scale that up or scale that down and still get usable, good data and prove that these parts are correct.
Lastly, a key that is coming online more, especially with the intelligence on these parts.
What is it that we can do with respect to more intelligence on these parts? Sometimes that’s a product design issue as much as a test issue, which goes back to what we were talking about.
Our key considerations are, in terms of how is your team set up, how do you interact with the other avenues, within your organization, within your supply base, with your end user, in order to be able to leverage that, and come up with things that allow us to be able to do what we need in the factory, and still protect for the part?
So, we need to come up with a different strategic initiative for testing our batteries. We need to remember our shifts in perspective. Take a look at what we have on the slide; the left-hand side shows things that are going from a prototype stage to a manual, small-volume production stage, to a high-mind stage. The issue we have today is that these things could be happening on top of each other, we could be trying to design the final highly automated high-volume line, while at the same time, we are still proving things back in the lab. So, our proof of principles and the timeline is highly compressed, and often on top of each other.
We need to identify issues and problems quickly, and this was a solve early for failure. We need to be able to take our equipment and flex it from our pilot line to our production volumes; scalability is key for this. The difficulty we will have here is in trying to make sure that we do not bring those design validation measurements into our production. And this could be heard early on. And maybe it is a kind of thing that as we ramp up, we phase out what is required for that, and get in what is required for this. But to do that, perhaps we need some other tools at our disposal.
Some other considerations to look at are illustrated on the right side here, where we talked about the scalability and being able to take things up and down a little bit. We talked about some of the safety protocols and what is required to handle these parts properly. What to do if we have thermal events occurring? These kinds of considerations. And then, what is the effect on our facilities? We are talking about a lot of power we are putting into these parts and taking out. Do I have the power grid within my existing facility to be able to handle it? Most of the time, we are able to take the discharges off the batteries and consume it within our plant, which is great, to reuse that electricity. If not, is my discharge large enough that I am going to overwhelm my facility? And do you try and push that on to the local utility, through the point of connection? You get an idea and plan for that, and this is especially important when we go from small production to a large production quickly. To make sure, of some of those things can take a while, to get in place we can get that going quickly.
You look at the intelligence that is inherent on these parts and taking advantage of that. And this is where some of the newer technologies that are coming in with respect to the industrial Internet of Things (IoT) and the inter-connection, the data that we can grab there and use to increase our capabilities, to modify and change as things are changing. We take a look at artificial intelligence or deep learning type algorithms and systems, and this is beyond just logistics and delivering product to the line; this is in terms of trying to resolve between those test parameters from the design validation phase versus the production phase, which ones are important. And not only that, but the feedback from the continuous learning process that was extended out there in time, we need to bring that back in sooner. And this is where some of these deep learning and artificial intelligence processes may be able to help us to reduce this quicker, accelerate that and make it so that we can win.
ATS Industrial Automation Is Your Ideal Partner
ATS is uniquely suited to provide a solution throughout the entire lifecycle of a product.
We have a great team of people and a lot of skill and knowledge. We produce great products and we like doing stuff. We are good at it. We have been doing it for a long time. We have a great staff of people with respect to project management and installation service, in terms of getting projects executed and built and installed and maintained. We have a global footprint; we are located around the world, so wherever you are, wherever you want to do your product testing, we are there for you. We are financially stable, have been around a long time, and we are not going anywhere. Couple our people and our company structure with our depth of experience in battery, assembly, storage, and test systems, and it is a winning combination for everybody. Every day matters.
Every project is unique. Allow us to listen to your challenges and share how automation can launch your project on time.