Battery fires, although rare, are intense and hazardous, presenting safety risks to workers and consumers. In battery manufacturing, preventing thermal runaway events is not just a priority—it’s a necessity.
As global demand for electric vehicles (EVs) continues to rise and regulations around safety evolve, manufacturers face the challenge of balancing rapid assembly with the precision and careful handling required to consistently ensure proper thermal management. Understanding and addressing these challenges can pave the way for safer and more efficient battery manufacturing processes.
Understanding Thermal Events
Thermal runaways in battery manufacturing refer to incidents where excessive heat is generated within a cell, potentially leading to battery failure. This has the unfortunate possibility of cascading heat to adjacent battery cells, causing further battery failures and leading to a potential catastrophic event, including fires and explosions. These incidents can create serious risks to life and cause extensive property damage.
The primary causes of thermal runaways include:
- Overheating: This occurs due to high ambient temperatures or excessive current flow.
- Overcharging: The battery is charged beyond its capacity.
- Physical Damage: Punctures, crushing, or other physical damage can compromise cell integrity.
Implementing stringent safety measures and protocols during battery production is crucial to mitigating these risks. This includes precision material handling to avoid physical damage during assembly and robust testing and monitoring of battery temperatures.
Material Handling Considerations
Manufacturers must ensure each battery cell and module is transported carefully during assembly and testing. A primary challenge is managing the delicate interface between the tab and cell internals. Any damage to the interface can compromise cell functionality and performance.
Unique handling considerations are required to manufacture different battery cell types and help prevent thermal runaways. For pouch cells, this includes:
- Using Vacuum Handling: This technique helps minimize compression and avoid damaging the delicate components of pouch cells.
- Maintaining Alignment: Ensure the correct sequence is kept during the stacking process to prevent cell damage.
- Monitoring Tab and Cell Interface: Pay close attention to the connection of the battery internals to prevent any damage that could lead to thermal runaway events.
- Implementing Proper Compression Techniques: Mechanical pressure methods help maintain the shape and integrity of cells without causing damage.
- Careful Handling During Assembly: Avoid potential damage by handling the cells with precision throughout key production steps, such as tab formation, stacking, and compression.
Compression & its Importance
Proper compression approaches play an essential role in ensuring cells remain structurally sound and function efficiently. During compression, battery manufacturers must consider variables such as the amount of force applied, the duration of compression, and the uniformity of pressure distribution. Applying too much or uneven force can damage the cells, leading to potential safety hazards. By controlling these variables, manufacturers can prevent physically altering the cells and maintain their integrity. These techniques also reduce the risk of overheating, overcharging, and other issues that could lead to dangerous thermal runaways.
Cooling & Thermal Management
Cooling is another important component that can prevent thermal runaway by dissipating excess heat generated during the operation of pouch cells. These methods include the use of thermal interface materials, which enhance heat transfer between the cell and the cooling system. Cooling plates can also be used to provide a direct cooling surface for the cells. These help maintain optimal operating temperatures, ensuring the cells do not exceed safe temperature thresholds.
Balancing High-Speed Assembly & Careful Handling
Achieving stability between production and meticulous transport is required to prevent thermal runaways in battery manufacturing. Innovations in automation and material handling technologies play a key role in reaching this balance, ensuring high-speed assembly can be maintained without sacrificing the precision and care needed to produce safe, reliable batteries.
At ATS Industrial Automation, we have delivered over 110 battery assembly and test lines and understand thermal management challenges when scaling battery lines. Our team of experts is ready to support your battery production needs—contact us to discuss your project today.
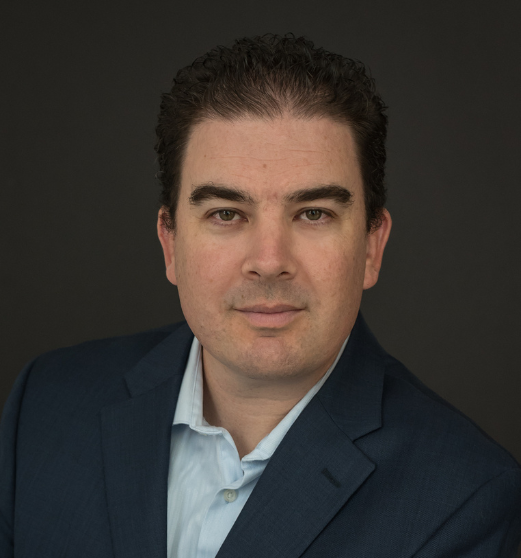
Cameron Bruce
Director of Engineering
ATS Industrial Automation
Cameron works with customers to design and optimize automation systems to build and scale production and drive operational efficiency. Cameron has helped companies across numerous industries to automate and optimize production for over 18 years.