As battery manufacturing grows, companies are working to improve the many formats in which we need electricity to be stored. For example, charging electric vehicles (EVs) faster, helping battery energy storage systems (BESS) last longer, and making portable devices more reliable. One of the form factors for batteries in this solution set is prismatic cells. These robust powerhouses are changing the way battery manufacturers think about energy storage and consumption. But why are prismatic cells becoming the go-to choice for large battery applications?
Characterized by their flat, rectangular shape and rigid casing, prismatic cells provide high energy density and power output. Unlike cylindrical cells, which are small and round, and pouch cells, which have a flexible, flat design, prismatic cells offer durability and efficiency due to their rigid casing.
Prismatic batteries are ideal for high-demand applications such as EVs and energy storage systems. Their larger size and higher energy capacity make them well-suited for products requiring substantial power.
Challenges of Prismatic Battery Assembly
Prismatic battery assembly comes with several challenges, including:
- Manufacturing Complexity: Due to the precision required to assemble a prismatic battery electrode layer, it can be more complex and costly than assembling other cell types.
- Swelling Problems: Like pouch cells, prismatic cells swell over time. If manufacturers don’t take proper countermeasures with compression, swelling can lead to the deterioration of the battery’s structural integrity.
- Energy Density Limitations: While the rigid casing of prismatic cells provides structural integrity, it can lead to greater density loss compared to other form factors.
Prismatic batteries are a compelling choice for applications that need to optimize efficiency and space. Still, due to their rectangular shape, manufacturing companies must carefully engineer and test prismatic cells to maximize their advantages, as module misalignment can lead to defects and a loss in efficiency.
The Prismatic Battery Assembly and Testing Process
Incoming Cell Validation
It’s crucial to ensure battery cells’ quality and reliability before they are assembled into modules or packs. Skipping or rushing through the testing process can lead to downstream challenges and safety issues with the product, including thermal runaway events. Incoming cell validation for prismatic cells involves a series of thorough tests to verify the cells’ electrical and physical properties.
Key tests include:
- Open Circuit Voltage (OCV)
- AC/DC Internal Resistance (IR)
- Electrochemical Impedance Spectroscopy (EIS)
- Cell Self Discharge
- Isolation Voltage
Based on these tests, cells are sorted and categorized, ensuring that only the highest quality cells proceed to assembly.
Electrical Array Formation
The electrical array formation process for prismatic cell assembly involves several critical steps to ensure the module’s performance and mitigate swelling, which can occur from a buildup of heat or gas. Initially, cells are built up into an electrical array using busbars, which connect them and form the module. This step helps achieve the desired voltage and amperage needed for the prismatic module. A cooling plate manages the heat generated during operation, and the dispensed thermal interface material (TIM) ensures efficient heat transfer.
Final Assembly & Testing
With the cooling plate in place, the entire assembly undergoes rigorous validation tests to confirm the integrity of the electrical connections and overall performance of the prismatic battery. These tests include DC internal resistance (DCIR) and high potential (Hi-Pot) tests, which verify the electrical performance and safety of the cells.
Testing is often found in the latter stages of prismatic module assembly. Modules are made into a battery pack by stacking them in series or parallel based on the manufacturer’s desired voltage, capacity, or power density. The final pack then undergoes end-of-line tests to ensure the battery fulfills the manufacturer’s specifications.
The Future of Prismatic Batteries: Cells to Packs
In some battery lines, manufacturers may merge the module and pack steps to save time, reduce weight, and optimize costs. Prismatic cells are particularly advantageous for cell-to-pack (CTP) applications due to their rectangular shape and rigid casing.
The design lets manufacturers bypass the traditional module assembly step, directly integrating the cells into a battery pack. By eliminating the need for modules, CTP reduces the number of components, simplifies assembly steps, and enhances the battery pack’s overall energy density. This approach not only optimizes space, but also improves thermal management, contributing to the final product’s reliability.
Building Prismatic Battery Assembly & Testing Lines
Prismatic cells represent a significant advancement in battery technology, offering a unique combination of high energy density, durability, and efficient space utilization. Their rigid, rectangular design makes them ideal for high-demand applications such as EVs and BESS. Despite production challenges, including meticulous alignment in module assembly and the risk of swelling, an experienced battery assembly and testing partner can guide manufacturers through each step of the process.
With 45+ years of automation experience and 110+ successfully delivered battery assembly and testing lines, our team of experts can help you build an end-to-end battery production program. Contact us today to discuss your unique battery project.
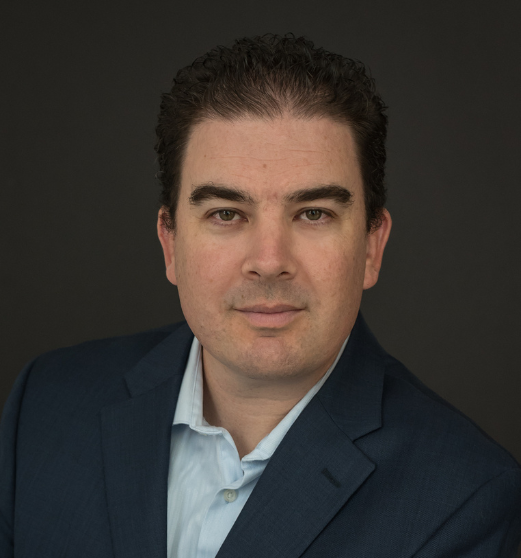
Cameron Bruce
Director of Engineering
ATS Industrial Automation
Cameron works with customers to design and optimize automation systems to build and scale production and drive operational efficiency. Cameron has helped companies across numerous industries to automate and optimize production for over 18 years.