In the rapidly evolving world of battery technology, manufacturers must understand the differences between cylindrical, pouch, and prismatic cells to make informed decisions based on their battery application.
Each battery type offers unique advantages and faces specific manufacturing challenges. Cylindrical cells are known for their robustness and high energy density, making them ideal for high-performance applications like electric vehicles (EVs). With their flexible and lightweight design, pouch cells are widely used in consumer electronics and small devices. Meanwhile, prismatic cells combine high energy density, durability, and cost-effectiveness, making them a popular choice for EVs and battery energy storage system (BESS) applications.
But what makes each of these cell types unique, and what are the challenges associated with manufacturing these batteries? In this blog, we’ll unpack the pros and cons of each form factor so you can decide which one is best for your needs.
What Makes Each Cell Type Unique?
Cylindrical Cells
Cylindrical cells have been in the EV space for many years; they’re not too different from the AA batteries we’re all familiar with as consumers, albeit with much higher energy densities. They have a durable, can-like structure that offers mechanical stability and safety. Cylindrical cells are popular due to their robustness and suitability for various high-performance applications.
One of the primary applications is in EVs. The cylindrical shape allows for efficient packing and cooling. Cylindrical batteries play an increasingly important role in BESS, where their durability and long lifecycles are a reliable solution for energy management.
Pouch Cells
Pouch cells differ from cylindrical or prismatic cells due to their flexible and lightweight design, allowing for a higher packing density and better space utilization.
Consumer electronics such as cell phones and tablets, plus small devices like toy drones, often contain batteries made from pouch cells.
Prismatic Cells
Prismatic cells are characterized by their flat, rectangular shape and rigid casing, providing high energy density and power output. Unlike cylindrical cells, which are small and round, and the flexible, flat design of pouch cells, prismatic cells offer durability and efficiency. They’re also more durable during the welding process—unlike cylindrical cells, where the weld occurs right behind the electrode, causing a high risk of pentation.
With their larger size, high energy capacity, and cost-effectiveness, prismatic cells are a primary choice in applications that require substantial power, such as EV or hybrid cars and energy storage systems. They may also be cheaper in large-scale production. If considering a cell-to-pack approach, prismatic cells are durable enough to do away with the otherwise necessary module step. This can lead to savings in both material and production costs.
Battery Assembly Considerations
Cylindrical Battery Assembly
Cylindrical cells present several challenges that manufacturers must consider to ensure the reliability and safety of the final product. Some challenges include:
- Weld Optimization: One primary issue is to avoid penetrating the outer casing of cylindrical cells. This is crucial because any penetration could lead to electrolyte leaks and potential safety hazards. Precise welding can mitigate this risk.
- Handling Exposed Terminals: Cylindrical cells’ exposed terminals require careful handling during assembly and testing to prevent damage or safety risks to tooling. This adds an extra layer of complexity to the assembly process.
- Thermal Management: Another significant challenge is ensuring cells properly cool within the battery module or pack. The cylindrical shape can make it difficult to achieve uniform thermal management, which is essential to maintain the battery’s longevity.
- Dimensional Variability: Cylindrical cells’ dimensional variations complicate the assembly process. Manufacturers need to implement stringent quality control measures to ensure consistency within cylindrical cells. This is true for both the discharged and fully charged state of the battery.
Pouch Battery Assembly
Pouch cell assembly requires careful handling to ensure the battery’s reliability and performance. Key challenges include:
- Fragility: Pouch cells are delicate and lack the dimensional stability of cylindrical or prismatic cells. They are essentially layered batteries with a thin foil shell, which makes them more susceptible to damage during handling and assembly.
- Material Handling: To prevent damage, operators must handle pouch battery materials with special consideration. Vacuum conveying ensures pouch cells remain flat. Vacuum also helps avoid distorting the foil seam or stressing the tabs.
- Tab Handling: There’s a fragile interface between the tab and the cell internals. Manufacturers must take care when bending or forming the tabs to avoid damaging or stressing the pouch cell.
- Compression: Manufacturers can use compression to maintain the shape and integrity of pouch cells. Cells are subjected to controlled pressure to ensure they remain uniform. Manufacturers must carefully manage any variables that may occur during compression, such as air gaps or inconsistencies within the cell layers, to avoid damage and maximize the battery pack’s performance.
- Welding and Bonding: Manufacturers must ensure stable electrical connections due to the vulnerable state of pouch cells. This process requires precision welding and bonding to avoid compromising each pouch cell’s integrity. Welding through multiple tabs is often required; in addition to welding challenges, tab bending and clamping are essential to a good process.
Prismatic Battery Assembly
Prismatic cell assembly offers unparalleled flexibility and efficiency. Still, common challenges include:
- Cost and Density Problems: The rigid casing of prismatic cells can lead to density loss, compared to other cell types.
- Sealing Integrity: Prismatic cells need to be airtight to prevent cell damage and maintain battery safety.
- Swelling: Prismatic cells are susceptible to swelling, especially under high temperatures or improper charging and discharging. Due to cell swell, battery manufacturers must administer the right amount of compression to mitigate this.
- Thermal Management: Due to their rigid casing, prismatic cells don’t cool as well. Integrating cooling plates and thermal interface material (TIM) helps manage heat distribution.
Each battery type—cylindrical, pouch, and prismatic—offers unique advantages and has its own set of challenges.
Cylindrical cells offer robustness, high energy density, and suitability for high-performance applications like EVs. However, they’re challenging when it comes to weld optimization and thermal management.
Pouch cells offer a flexible and lightweight design, allowing for higher energy density. The main challenge is fragility, which presents problems in material and tab handling, compression, and cooling.
Prismatic cells’ high energy density, durability, and cost-effectiveness make them a growing option for EVs and BESS applications. Their flat shape allows for efficient stacking and space usage. However, they have swelling and thermal management challenges.
Each battery manufacturer must consider which form factor to use based on the application at hand—as well as the benefits and challenges each cell presents. An experienced battery assembly and testing partner can help battery startups and original equipment manufacturers (OEMs) navigate these challenges at every stage of product maturity. ATS Industrial Automation has delivered more than 110 EV battery assembly and test lines.
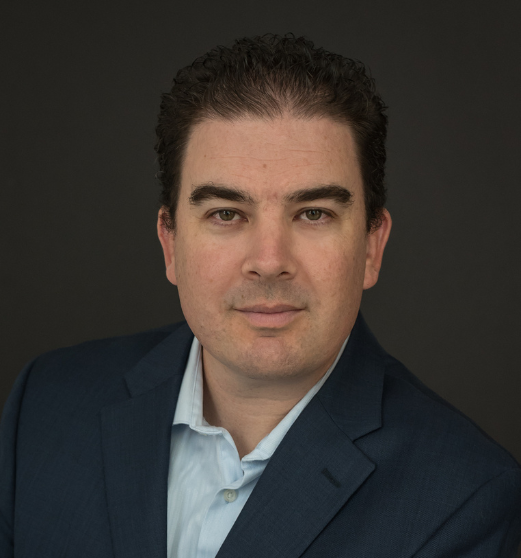
Cameron Bruce
Director of Engineering
ATS Industrial Automation
Cameron works with customers to design and optimize automation systems to build and scale production and drive operational efficiency. Cameron has helped companies across numerous industries to automate and optimize production for over 18 years.