Reducing the time it takes to launch new products is crucial for product manufacturers that want to stay competitive and meet customer demands. According to a survey from Gartner, Inc., 45% of all product launches are delayed by at least one month. Launch delays can lead to disappointed customers, unhappy investors, increased costs, and a negative impact on brand reputation.
Using tools like proof of principle (POP) testing can keep product launch schedules on track to meet demand. A design for manufacturability (DFM) approach also helps streamline product development, identify potential manufacturing issues early on, and ensure a smoother path to market.
What Causes Delays in Launch Times?
One of the main causes of launch delays is incorporating incomplete processes into the final assembly and testing solution. Sometimes, manufacturers only discover an ineffective, unfeasible, or incorrect process as the project moves into material requirements planning (MRP) implementation.
Strategies to Prevent Launch Delays
To mitigate delays, operators can use several strategies at different stages of the project lifecycle. During the ideation, proof of concept, and sample production phases, processes need to be fully developed and tested before implementation. This can happen through POP testing or simultaneous engineering, which helps identify and address potential issues early on.
When Can Upfront Engineering Help Reduce Time to Launch?
Upfront engineering, also known as concurrent or simultaneous engineering, involves creating detailed 3D models, engineering drawings, and small-scale physical prototypes early in the project’s lifecycle. The method helps identify possible issues and design requirements before building full-scale manufacturing equipment. Doing so allows engineers to detect problems early, which reduces the need for rework and ensures the final product meets specifications. This proactive approach helps significantly reduce the time and costs associated with product development and launch.
Upfront engineering is particularly beneficial when dealing with high-risk areas or components with long lead times. For example, if a manufacturer needs to determine the size of a press for a specific task, upfront engineering can help project leads make this decision earlier in the process. This means they can order necessary equipment sooner and compress delivery timelines. Upfront engineering also prevents manufacturers from using ineffective solutions in final designs, further reducing the possibility of delays.
When Can Proof of Principle Testing Help Reduce Time to Launch?
POP testing, sometimes referred to as proof of concept or proof of principle testing, can significantly reduce launch delays by swiftly addressing potential production issues. During the ideation, proof of concept, and sample production phases, POP studies allow teams to test the feasibility and viability of ideas and processes. By building test stands or product samples and conducting sample production runs, engineering teams can identify and resolve issues before they become major problems during full-scale implementation.
POP studies also help prevent rework by detecting high-risk areas early within assembly workflows and providing empirical physical results. This can save both time and resources. Additionally, POP studies can help leaders make informed decisions about equipment and process requirements, shortening the overall delivery timeline.
How to Set Up a Proof of Principle Study for Success
The key to a successful POP study is communication. If leadership miscommunicates the purpose behind the study or doesn’t set clear success criteria, this will lead to misunderstandings about what an effective study looks like. It may also lead to unnecessary study iterations.
Develop a Clear Problem Statement
It’s crucial to determine the question for a POP study because it clearly defines the problem that needs to be solved. This clarity ensures all stakeholders mutually understand what constitutes an effective study, and the number of iterations or attempts required. Lacking a well-defined question can lead to ineffective solutions and wasted resources.
Some examples of bad problem statements include:
- Can a robot pick a product out of a bin?
- Why is this a bad problem statement? This statement does not have enough constraints around the problem. We do not know how much time must be allocated for the process, how much floor space is allocated for the system, or whether there are different bins. We also don’t know how consistent the problem is. Does it occur every time or once every 30 times?
- Can we join these two components together?
- Why is this a bad problem statement? It does not define what the process is, what materials are involved, the size of the parts, whether we can change or alter any materials, or whether any process controls must be in place. How is success defined for joining these parts together?
Some examples of good problem statements include:
- Can we pick a three-pound round product out of a bin using an industrial robot once every 10 seconds? Can we place it onto a conveyer within a half-inch tolerance within an allocated 60 square feet?
- Can we ultrasonic weld these one-inch plastic components within five seconds without deforming the plastic and pass a pull test of 20 pounds?
Determine the Level of Communication
Original equipment manufacturer (OEM) leaders must build a communication process for their POP study. Are weekly email updates needed? Should we hold monthly meetings to discuss current findings? Committing to regular, documented communication ensures all parties clearly understand the project’s goals, progress, and any challenges that may arise. Effective communication also helps those involved understand the scope of work. This may include specifying the documentation package—such as reports, photos, videos, or 3D computer-aided design (CAD) models—and recognize limitations for each process.
Determine the Proof of Principle Testing Team
A POP study is only as strong as the information provided for it. For a successful study, managers should determine which internal team members can answer any questions the POP team may have. The most effective studies often have a collaborative approach: the manufacturer can provide detailed information about product or process challenges and the POP team can offer effective solutions.
There are several potential setups for a POP team, including:
Collaborative Team Setup | Consultative Team Setup | Independent Team Setup | |
---|---|---|---|
The manufacturer works directly with the POP team, often including one of their team members. | The POP team provides expertise and solutions while the manufacturer focuses on other aspects of the project. The manufacturer’s staff must be responsive to any questions the POP team has about the problem or product. | The POP team works to solve the problem, with minimal involvement from the manufacturer. Like the consultative team setup, the POP team needs all the necessary inputs from the manufacturer for the study to be effective. | |
Advantages | This approach allows for continuous feedback and adjustments, ensuring the POP study addresses specific issues. | This method can free up the manufacturer’s resources and allow them to concentrate on core activities. | This setup can be efficient and quick, since the supplier can focus solely on the POP study without any distractions. |
Risks | This setup requires a significant time commitment from both parties and won’t free up the internal team to complete other projects. | This approach may lead to the supplier not fully understanding the problem or product, as they are not as involved in day-to-day activities. | This approach may lead to miscommunication and misunderstandings, as the supplier may not fully understand the manufacturer’s needs or specific requirements. |
Reduce Launch Delays with Collaborative Engineering Practices
Manufacturers that want to maintain a competitive edge and meet customer expectations must reduce the time it takes to launch new products. Leveraging POP testing and upfront engineering empowers manufacturing companies to streamline product development processes and identify potential issues early on. These strategies also improve cost efficiency and overall product quality management. Embracing these approaches can lead to successful product launches and enhanced customer satisfaction. Get in touch with us today to learn how our collaborative POP study approach can help you strengthen your product and presence in the market.
Every project is unique. Allow us to listen to your challenges and share how automation can launch your project on time.
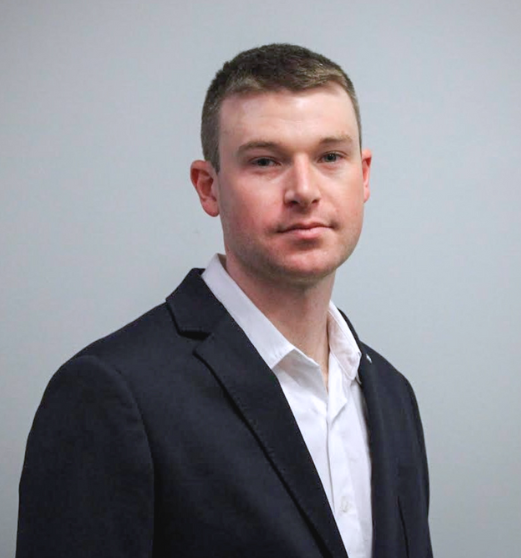
Kevin Peake
Key Account Manager
ATS Industrial Automation
Kevin has helped companies across numerous industries automate and optimize production. Kevin has a Bachelor of Science in Aerospace Engineering and Mechanical Engineering, he loves robots and has built them in his basement for fun. He enjoys helping customers configure systems to build and scale production and drive operational efficiency.