In automation, precision isn’t just a technical specification—it’s imperative to succeed. When tolerances drop below one millimeter, the margin for error disappears. Every micron matters.
Precision assembly is the process of joining or manipulating components with extremely tight tolerances—typically less than one millimeter. These assemblies are common in industries like medical devices, electronics, and battery manufacturing, where even the smallest misalignment can lead to product failure, regulatory violations, or massive scrap costs.
But precision isn’t the only challenge. When manufacturers attempt to scale these processes—especially at high speeds—the complexity increases exponentially. Synchronizing fine motor movements, maintaining consistent quality, and minimizing downtime all become significantly harder. If a problem isn’t identified and corrected quickly, the consequences can be severe: lost product, lost time, and lost revenue.
The Challenges of Precision Assembly
Precision assembly presents a unique set of engineering and operational complexities, especially when it comes to speed and sophisticated components.
Low-Speed Precision Assembly
At slower speeds, the challenge is achieving consistent accuracy. Even without high throughput, manufacturers must finely tune the system to avoid damaging delicate parts or introducing variability. This often requires specialized tooling, fine motor actuators, and rigorous quality control.
High-Speed Precision Assembly
With speed in the equation, the difficulty multiplies. High-speed systems must synchronize intricate movements with minimal variation. If tolerances drift or components misalign, the result can be disastrous—especially when dealing with valuable parts. A scrap rate of just 0.5% in a high-volume environment can mean millions of dollars in lost product annually, extended downtime, and missed production targets.
In both cases, the stakes are high. Since precision assembly is often used for high-value products, even small errors can lead to significant financial losses.
Quality Control in Precision Assembly
This part of the process isn’t optional in precision assembly—it’s essential. The tighter the tolerances, the greater the need for in-line and end-of-line testing.
In-Process Testing
For high-risk processes, in-line testing helps catch issues before they escalate. Common methods include:
- Vision systems or vision alignment, defect detection, and surface inspection.
- Force and distance monitoring for pressing or joining operations.
- Laser weld monitoring for consistency and penetration.
- Leak and pressure testing for sealed components.
- Electrical Testing for continuity and functionality.
These checks help ensure each step of the process meets required standards, reducing the risk of downstream failures and costly rework.
End-of-Line Testing
For high-risk assemblies, end-of-line testing provides a final safeguard. It ensures all components meet functional and regulatory standards before leaving the facility.
Managing Multi-Part Precision Assemblies
As the number of components in an assembly line increases, so does complexity. One of the biggest challenges is tolerance stack-up—the cumulative effect of small variations in each part. When multiple components are assembled, even minor deviations can lead to significant misalignment.
To manage this, manufacturers can:
- Define and control tolerances for each part.
- Use in-process testing to catch drift early.
- Design systems that can adapt to variations.
- Consider flexible fixturing.
An automation partner can support this process by offering design-for-manufacturing (DFM) guidance, digital tools like simulation, and proof of principle testing to validate concepts before implementation.
High-Speed, High-Precision Tools
To scale precision assembly, manufacturers need more than good design—they need the right tools. ATS Industrial Automation offers three digital technologies that play a critical role in enabling high-speed, high-precision automation:
SuperTrak CONVEYANCE™
This linear motion platform offers precise, independent shuttle control. It enables high-speed part movement with minimal mechanical complexity, reducing tolerance stack-up by eliminating the need for traditional indexing conveyors—which often introduce variability.
Symphoni™
Designed for speed and repeatability, this modular, cam-driven assembly platform allows for synchronized, precise movements across stations. Because it’s configurable, Symphoni™ can adapt to different products and processes—making it ideal for consumer product goods manufacturers.
Illuminate™ Manufacturing Intelligence
Illuminate™ provides real-time visibility into machine performance. In precision assembly, where scrap rates and downtime can escalate quickly, this manufacturing intelligence platform helps detect drift, identify root causes, and optimize performance through data-driven insights.
Together, these tools form a comprehensive digital manufacturing ecosystem that enables faster commissioning, higher throughput, and improved quality control.
The Role of Proof of Principle (POP) Testing
Proof of principle testing is a critical step in mitigating precision assembly projects. By validating high-risk processes early—before committing to full-scale equipment—manufacturers can:
- Confirm feasibility and repeatability.
- Optimize tooling and process parameters.
- Identify where in-process checks are needed.
- Reduce material waste during commissioning.
- Save time and costs during final integration.
POP testing also helps define the right quality checks, ensuring the system design meets real-world performance expectations.
Questions to Consider When Developing a Precision Assembly System
When planning a precision assembly system, manufacturers must ask a potential automation partner:
- What experience do you have with this type of assembly?
Manufacturers will want to look for a partner with demonstrated success in similar applications and industries. - What level of precision can your systems achieve—and how is it verified?
Determine whether the partner can support the solution with data and thoroughly validate processes to ensure tolerance requirements are met. - Can you support cleanroom or highly regulated environments?
If the product requires it, make sure the partner has experience with cleanroom design and compliance. - How do you manage tolerance stack-up in multi-part assemblies?
Ask the partner whether they use strategies like in-process testing, and modular tooling. - What’s your approach to risk mitigation?
Look for a partner that offers POP testing, simulation, and digital or system twins to identify and address risks early. - How do you support training?
Precision systems require skilled operators. Ask the partner what training programs, documentation, and support they provide to ensure a smooth ramp-up after the project ends.
Why an Experienced Automation Partner is Critical for Precision Assembly
Precision assembly is one of the most demanding areas of automation. It requires deep expertise, advanced tools, and a proactive approach to risk management. Our experts at ATS Industrial Automation bring all three.
From rigorous POP testing and simulation to high-speed platforms like Symphoni™ and SuperTrak CONVEYANCE™, ATS builds systems that are fast, accurate, and reliable—enabling manufacturers to assemble high-quality products while minimizing costly scrap or rework. Whether you’re launching a new product or scaling an existing one, ATS can help you build it right—down to the last micron.
Every project is unique. Allow us to listen to your challenges and share how automation can launch your project on time.
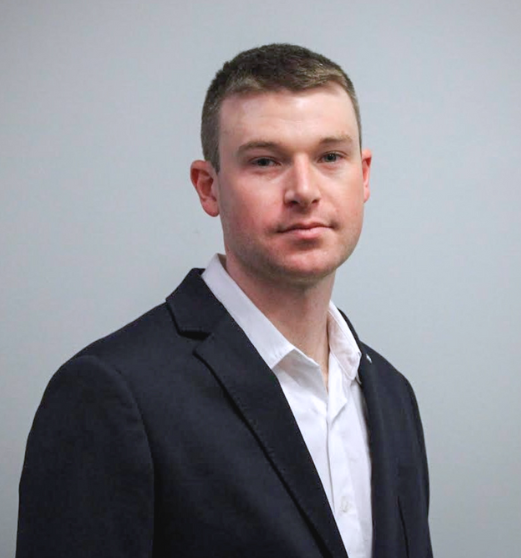
Kevin Peake
Key Account Manager
ATS Industrial Automation
Kevin has helped companies across numerous industries automate and optimize production. Kevin has a Bachelor of Science in Aerospace Engineering and Mechanical Engineering, he loves robots and has built them in his basement for fun. He enjoys helping customers configure systems to build and scale production and drive operational efficiency.