The shift from module-based to cell-to-pack assembly in battery technology is revolutionizing the electric vehicle (EV) industry. The transition eliminates the need for intermediate modules, which means manufacturers can directly integrate individual cells into the battery pack. This approach can increase volume utilization by up to 50% and reduce the number of parts by 40%. It also saves manufacturers significant time and resources.
Despite this promising approach, there are several factors manufacturers must consider while navigating cell-to-pack assembly. Without the guardrail that modules provide, manufacturers need to carefully plan for a strong thermal management strategy, rigorous testing, and an increased focus on quality control.
Considerations for Cell-to-Pack Assembly
Because cell-to-pack assembly doesn’t require modules, this method significantly enhances energy density. By avoiding the modular structure, the design allows more cells to be packed into the same volume, increasing the overall capacity. With fewer structural components needed to hold the cells together, this approach also reduces the weight of the battery pack.
With fewer parts to assemble, the production line becomes more streamlined, reducing the time and cost associated with cell-to-module-to-pack assembly. This efficiency may be crucial for manufacturers to meet a growing demand in the battery production industry.
However, it can be challenging to maintain optimal temperature without modular barriers. The absence of modules means fewer guardrails for heat dissipation, which can lead to uneven temperature distribution within the pack. Product teams must implement effective thermal management strategies to ensure all cells operate within safe temperature ranges.
Another critical consideration is ensuring the pack’s structural integrity without modules. The design must include robust structural elements that can withstand mechanical stresses to maintain the battery pack’s durability and avoid thermal runaway events.
Fewer interconnects in the cell-to-pack design can also reduce potential failure points. While this enhances the reliability and safety of the battery pack, there needs to be a robust design to ensure the electrical connections between cells are secure and able to handle operational stresses.
Challenges Associated with Module-Free Structures
Designing battery packs without modules introduces significant complexities to the process. The absence of modular structures requires innovative approaches to maintain performance and safety.
A cell-to-pack design can increase the risk of thermal runaways due to a closer proximity of cells. Without the separation modules provide, cells are more susceptible to overheating. A strong thermal management strategy can mitigate these risks and confirm the final battery pack is safe for consumers.
Quality control also becomes more challenging without the presence of modules. Ensuring consistent quality and performance across cells without modular separation requires rigorous testing and stringent inspection processes to ensure the pack’s overall reliability.
Maintenance and repair can also be difficult in a cell-to-pack design. It’s a more complex process to replace individual cells than modular designs, where operators can more easily swap faulty modules. Still, it’s not impossible to repair a cell-to-pack design battery — it just necessitates a more meticulous approach.
Finally, cell-to-pack designs normally require cell handling with a larger motion platform, as manufacturers now need to distribute cells over a larger area in a pack compared to a module. Particular attention needs to be paid to pack level transportation and accuracy to precisely position and bond individual cells over a much larger area.
Prismatic Cell Use Case
With their rectangular shape and robust aluminum casing, prismatic cells are well-suited for cell-to-pack assembly. Their design allows for efficient stacking and better space utilization, enhancing overall energy density while simplifying manufacturing.
In a cell-to-pack line, prismatic cells present unique material handling considerations, including wrapping and compression. These cells often require wrapping for additional protection, which adds a layer of complexity to the assembly process. Compression also manages the swelling of cells during operation, keeping them securely in place and maintaining overall structural integrity.
Cooling techniques and thermal interface materials (TIMs) are critical to manage the heat that prismatic cells generate. These materials help remove air gaps and improve thermal conductivity, which helps maintain the battery pack’s optimal temperature.
Battery Assembly for Cell-to-Pack Lines
Cell Preparation and Testing
In the cell-to-pack assembly process, cell preparation and testing are critical steps to make sure every cell meets the required standards before being integrated into a pack. Initial inspection and quality control measures can identify any cell defects or inconsistencies. This involves a thorough visual inspection to check for physical damage and automated testing solutions to verify each cell’s dimensions and overall conditions.
It’s crucial that teams test for capacity, voltage, and internal resistance. When each cell undergoes rigorous testing to measure its capacity, manufacturers can confidently validate that the pack can store the expected amount of energy. Voltage testing confirms that the cells operate within the specified voltage range, while internal resistance testing helps identify potential issues affecting performance and longevity. These tests, among others, prove that the cells can function reliably in the final battery pack.
Another important step is sorting and matching cells for uniform performance. Cells are sorted based on their test results to ensure that only those with similar performance characteristics are grouped together. This matching process helps maintain uniformity within the battery pack. By only including cells with similar capacities, voltages, and internal resistances, the manufacturing team can prevent imbalances that could lead to reduced efficiencies or premature failures.
Pack Assembly Process for Cell-to-Pack-Lines
The pack assembly process for cell-to-pack lines involves several critical steps to ensure the battery pack is reliable. The first step is arranging the cells in the desired configuration to maximize space and optimize performance.
Once the cells are positioned, they must be held in place. Teams typically do this with brackets, adhesives, or other mechanisms that prevent the cells from shifting during operation.
The final step in assembly is connecting the cells according to the design. By creating electrical connections between the cells to form a complete circuit, the pack can deliver the required power output.
Effective thermal management and insulation are crucial during pack assembly so cells can operate within safe temperature ranges. Cooling systems, such as liquid cooling or thermal interface materials, help dissipate heat away from the cells. Proper insulation also protects the cells from external temperature fluctuations and maintains a stable operating environment, enhancing the battery pack’s overall safety and longevity.
Quality Control and Testing of Assembled Packs
The final inspection involves thorough quality control and testing of the pack to identify any physical defects or inconsistencies. This includes checking the integrity of the connections, cell alignment, and the pack’s overall structural soundness. Automated systems can assist in this process to ensure precision and consistency during operations.
Additional testing measures that aid in quality control include:
- Performance testing, which involves checking the battery pack for capacity, cycle life, and thermal performance
- Capacity testing to ensure the pack can store and deliver the expected amount of energy
- Cycle life testing to evaluate how well the pack maintains its performance over charge and discharge cycles
- Thermal performance testing, which assesses the pack’s ability to safely manage heat during operation
Stringent testing to verify the pack meets performance, safety, and environmental standards is essential to comply with industry guidelines and requirements set by regulatory bodies.
Optimizing Battery Packs: The Shift to Cell-to-Pack Design
Innovations in battery technology are driving significant advancements in battery assembly. Advancements in materials science are also driving the creation of more efficient and durable battery components. Meanwhile, innovations such as silicon anodes and advanced electrolytes are enhancing the performance and longevity of batteries, making them suitable for a wider range of applications.
Continuous improvement and quality assurance are paramount in the battery manufacturing industry, especially with cell-to-pack designs. Production teams must focus on refining processes and implementing rigorous quality control measures to ensure every battery pack meets the highest performance and safety standards. Regular testing, monitoring, and analysis of designs and processes can help teams identify any adjustments needed and maintain consistency in production. By prioritizing continuous improvement, manufacturers can stay ahead of industry trends.
Choosing an experienced automation partner for battery assembly and testing offers several advantages. Our automation and precision engineering expertise ensures battery packs are assembled with the highest accuracy and efficiency. A partner that offers an integrated approach to testing and assembly also helps guarantee that each battery pack undergoes thorough inspection and performance evaluations before it hits the market. By ensuring compliance with industry standards and regulations, battery manufacturers can produce their designs with confidence and deliver a high-quality battery that consumers trust.
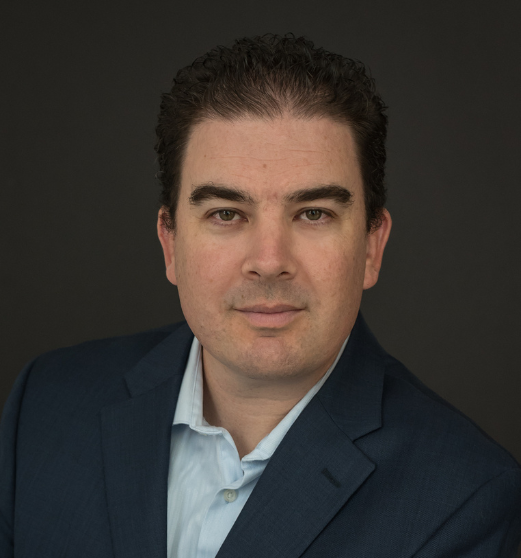
Cameron Bruce
Director of Engineering
ATS Industrial Automation
Cameron works with customers to design and optimize automation systems to build and scale production and drive operational efficiency. Cameron has helped companies across numerous industries to automate and optimize production for over 18 years.