With the global market for lithium ion batteries expected to grow by over 30% annually, keeping workers safe during battery assembly has never been more critical. In recent years, the Occupational Safety and Health Administration (OSHA) has fined companies for putting their employees at risk. In fact, a lithium battery fire in October 2023 revealed that a major manufacturer failed to adequately train employees or educate them about safety hazards. Manufacturers can avoid incidents like this by understanding and prioritizing safety.
Battery safety extends far beyond the final product. The battery’s design must prioritize consumer safety and minimize harm to the environment. It’s a multifaceted approach that includes production workflows, rigorous risk assessments, and adherence to global safety standards. Comprehensive measures can protect employees from potential hazards such as chemical exposure and electrical accidents, meet regulatory standards, and ensure the reliability of the batteries produced.
Prioritizing Safety in Battery Manufacturing
Battery manufacturing requires meticulous attention to various aspects of the operation. From understanding the production footprint and equipment to conducting thorough risk analyses and following global safety standards, each step plays a crucial role in maintaining a safe and efficient manufacturing environment.
Manufacturing Footprint and Equipment
The facility’s layout, machinery placement, and workflows all play a significant role in minimizing risks and enhancing safety. Properly designed equipment from an experienced automation partner will adhere to safety standards that can prevent accidents and ensure smooth operations. By thoroughly analyzing manufacturing spaces, battery companies can identify potential hazards and implement measures to remove or mitigate them—like optimally placing equipment to prevent damage. This creates a safer working environment for employees.
Risk Analysis
Risk analysis in battery manufacturing can also identify and mitigate any risks associated with battery chemistry. This involves a comprehensive assessment to pinpoint the materials used in each production, and the potential interactions between components. Hazard analysis, failure mode and effects analysis (FMEA), and safety audits are commonly used. By regularly performing risk assessments, manufacturers can ensure the overall safety and reliability of the end product.
Global Safety Standards
Manufacturers must also make sure their equipment aligns with global safety standards. Properly designed equipment minimizes worker risks by incorporating features that prevent injuries, including ergonomic designs and fail-safes that shut down operations in case of a malfunction.
ATS Industrial Automation designs and builds equipment that’s compliant with local occupational safety regulations in North America, Europe, and Asia. This commitment means the equipment meets and often exceeds the required benchmarks. By adhering to stringent standards, ATS ensures the equipment is safe to operate. This global approach to compliance underscores the importance of maintaining high standards across sites, protecting employees and creating a safe production environment.
Safety in the End Product
Ensuring the safety of the final battery requires a comprehensive approach. Manufacturers can achieve safer and more reliable battery designs by leveraging past experiences, understanding battery chemistry, and collaborating with battery assembly experts who can help them navigate challenges or possible hazards.
Understanding Chemistry and Product Attributes
Each battery chemistry has unique characteristics and potential risks that teams must carefully manage. Manufacturers must possess a deep understanding of these attributes to design reliable, safe batteries. This includes knowledge of the materials used, the interactions between parts, and potential hazards. By thoroughly understanding battery chemistry and product attributes, companies can develop designs that minimize risks and enhance their product’s overall performance.
Collaboration with Experts
As production workflows and battery technologies become more complex, it’s essential for manufacturers to partner with industry experts. This partnership can help optimize the safety and effectiveness of battery designs and processes. Battery and automation specialists bring a wealth of knowledge and technical expertise that can help manufacturers address complex or specific issues and ensure the final product meets safety and performance requirements. They can also offer insights into occupational safety, helping mitigate hazards that employees may regularly face. By engaging experts, manufacturers can benefit from industry know-how and best practices, ultimately leading to a safer workplace and more reliable battery designs.
Ensuring Battery Manufacturing Safety for the Future
ATS Industrial Automation leverages its extensive experience delivering 110+ EV battery assembly and test lines to provide valuable input that ensures the safety of the end battery and the well-being of production workers. ATS offers customers insights and recommendations that help battery manufacturers identify potential safety issues and implement effective solutions. This involves working closely with customers to understand their specific needs and challenges and ensuring the final product meets the highest safety standards. By collaborating with ATS Industrial Automation, manufacturers can navigate the complexities of battery safety and achieve reliable, safe designs that meet market demand.
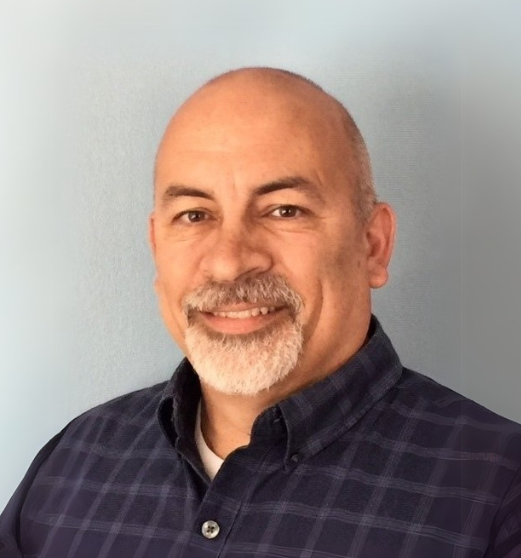
Russell Burton
Heath, Safety, and Environmental (HSE) Manager
ATS Industrial Automation
With over 19 years in the HSE field, Russell is committed to workplace safety. A certified safety management professional and instructional trainer, he has helped numerous government agencies, companies, and nonprofits cultivate safe, compliant work environments.