Pouch cells are a popular choice for battery manufacturers. That’s because the cell is highly efficient—achieving 90-95% packaging efficiency, one of the highest among battery packs. These cells are often used to make batteries for electric vehicles (EVs), but they can also be used in consumer electronics such as cell phones and tablets, or small devices like drones. Pouch cells differ from cylindrical or prismatic cells due to their flexible and lightweight design. This allows for a higher energy density and better space utilization than cylindrical cells.
However, the assembly and testing of pouch cells presents its own set of challenges, from the cells’ fragile, flexible structure to their sensitivity to high temperatures. Through meticulous handling, early validation, precision welding, and quality checks, battery manufacturers can ensure their product’s performance now and in the future.
Common Challenges in Pouch Battery Assembly & Testing
Assembly of pouch batteries presents several unique challenges that require careful handling and special processes to ensure their reliability. Some of these challenges include:
- Fragility: Pouch cells are delicate and lack the dimensional stability of cylindrical or prismatic cells. These layered batteries, which are enclosed in foil—which is less robust than the rigid cases used in cylindrical and prismatic cells—are more susceptible to damage during handling and assembly in comparison.
- Material Handling: Special considerations are needed for material handling to prevent damage. Vacuum handling is often used to manipulate pouch cells to avoid distorting the foil seam or stressing the tabs.
- Tab Handling: The interface between the tab and the cell internals is also fragile. Manufacturers must take care when bending or forming the tabs to avoid causing damage or stress.
- Compression: During the compression process, the cells are subjected to controlled pressure to ensure they remain flat and uniform. This is essential for the batteries’ performance and longevity, as it helps eliminate air gaps or inconsistencies within the cell layers, which could affect cell efficiency and stability.
- Welding and Bonding: It’s critical to ensure stable electrical connections through welding and bonding. However, the area where the weld needs to occur can often be fragile. Excessive weld power will quickly penetrate thin pouch cell tabs and potentially damage substrate material. Too little power, and the bond won’t form correctly. This process requires precision and testing to avoid compromising the cell’s integrity.
Pouch Battery Assembly Steps and Considerations
Incoming Pouch Cell Validation
The first step in pouch assembly is incoming cell validation. This step ensures the quality and reliability of the cells before they proceed to further stages of assembly. Cell validation involves a series of inspections and tests to verify the cells meet the required specifications and standards.
Critical aspects of incoming cell validation include:
- Checking for physical defects.
- Measuring cell dimensions.
- Conducting electrical tests to assess the cell’s capacity, voltage, and internal resistance.
By validating incoming cells, battery manufacturers can identify and address issues early on. This can reduce the risk of defects downstream and improve the overall performance and safety of the final battery pack.
Pouch Cell Tab Trimming & Formation
Tab trimming and formation are critical to present the tabs within the required parameters for success downstream. If this critical process is not executed properly, the risk dramatically increases a thermal runaway event. Poor electrical connection or physical damage during final tab assembly steps are all present risks that can lead to significant safety concerns.
In this process the tabs, which extend from the pouch cell, are carefully trimmed to the required length and shape.
Then comes the formation step, where the tabs are bent or shaped to fit the battery’s specific design requirements. Precision is crucial in this stage to avoid damaging the fragile interface between the tab and the cell internals. Proper tab trimming and formation also maintain the cell’s performance and reliability, stabilizing electrical connections and minimizing the risk of mechanical stress or damage.
Pouch Cell Sequencing & Stacking
Another essential step is sequencing and stacking. This is especially important for applications requiring multiple cells, such as EVs. During sequencing, cells are arranged in a specific order to optimize performance and balance within the battery pack.
Stacking involves carefully aligning and layering the cells to form a cohesive battery pack. Precise stacking mitigates misalignment and secures proper cell connections.
Pouch Cell Compression
Compression maintains the shape and integrity of pouch cells. During this step, the cells are subjected to controlled pressure to ensure they remain flat and uniform. An adhesive and compression absorbing layer is often applied between the cells, which helps secure them in place and keep them aligned during the compression process.
However, to avoid damaging the cells, manufacturers must carefully manage the variables during compression, including the amount of pressure applied and how long the process lasts. Proper compression techniques ensure the pouch cells meet the required standards.
Pouch Cell Busbar Assembly & Tab Formation
At the module stage, forming electrical connections for pouch cells involves using busbars to create stable and reliable connections between the cells. This process ensures the cells function as a unit. Meanwhile, series connectors link multiple cells together, allowing for the desired voltage output of the battery module.
Pouch Cell Busbar Welding
Busbars are typically welded or bonded to the pouch cell tabs to maintain a secure and stable electrical connection. During busbar assembly, the tabs of the pouch cells are carefully bent or shaped to fit the battery pack’s specific design requirements. Correctly aligning and securely connecting the busbars minimizes the risk of mechanical stress or damage and maintains performance and reliability.
Precision in welding also helps battery manufacturers avoid compromising the cells’ integrity and ensures durable connections. The welding process must be carefully controlled to prevent damage to the fragile interface between the tab and the cell internals.
Thermal Interface Material Dispensing & Cooling Plate Considerations
Managing the heat generated by pouch cells during operation increases the longevity of the battery. Thermal interface material (TIM) dispensing and cooling plates are a common solution, applied between the cells and cooling plates to improve thermal conductivity and heat dissipation. Proper dispensing ensures uniform coverage and prevents air gaps, which can cause hotspots and lower performance.
Cooling plates, often made of materials with high thermal conductivity, maintain even heat distribution across the pouch cells. Manufacturers must carefully design and place these cooling plates to ensure they effectively manage the thermal load without adding excessive weight or bulk to the battery module.
Battery Assembly Quality Checks & Pack Assembly
The final stage of pouch assembly involves a series of rigorous inspections and tests to verify the modules meet the required specifications and standards before enclosing them in the pack for further quality checks.
Key aspects of these quality checks include:
- Visual inspections for physical defects.
- Thorough weld quality inspections.
- Electrical tests to assess capacity.
- Voltage and internal resistance.
- Thermal evaluations to ensure proper heat management.
By conducting thorough quality checks, battery manufacturers can address issues before deploying the batteries, ensuring the final product’s safety and efficiency. Often, battery assembly lines will have both in-line and end-of-line tests. In-line tests help reduce scrapped parts and identify process steps that need refinement. End-of-line tests are focused on ensuring only the best quality batteries are used in the final product.
Charging Up Pouch Assembly & Testing Lines
The assembly and testing of pouch cells are intricate processes that require meticulous attention to detail and precise handling. From incoming cell validation to final quality checks, each step plays a crucial role in ensuring the reliability and performance of the battery.
By collaborating with an automation partner that understands the challenges and considerations involved in battery assembly and testing using pouch cells, battery manufacturers can optimize their processes early on and produce higher-quality batteries that meet the demands of rapidly evolving technologies.
Every battery project is unique. Allow us to listen to your challenges and share how automation can launch your project on time.
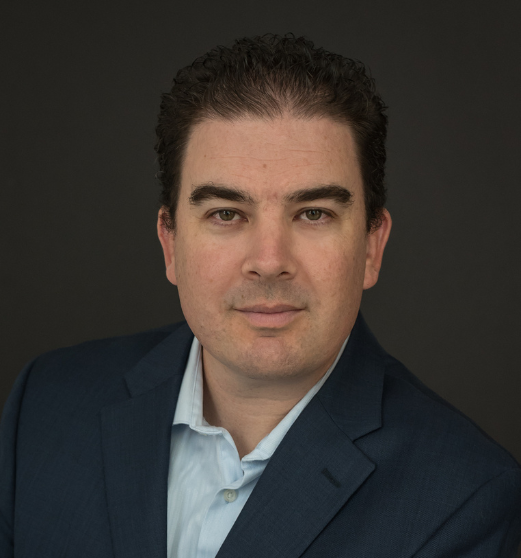
Cameron Bruce
Direktor für Ingenieurwesen
ATS Industrial Automation
Cameron arbeitet mit Kunden zusammen, um durch Entwicklung und Optimierung von Automatisierungssystemen die Produktion zu erweitern und die Betriebseffizienz zu steigern. Cameron hilft seit über 18 Jahren Unternehmen aus zahlreichen Branchen dabei, die Produktion zu automatisieren und zu optimieren.