SMR Case Study Highlights
Company
NuScale Power
Industry
Nuclear – Small Modular Reactors (SMR)
Region
North America
Customer
Nearly 20 years ago NuScale Power had a vision for a new type of reactor, a small modular reactor (SMR). In 2020, NuScale was the first SMR developer to receive U.S. Nuclear Regulatory Commission design approval.
Challenge
A Drive for Innovation to Produce Green Energy
NuScale needed a strategic partner that aligned with their vision and drive for innovation.
Minimizing outage time for the reactor was critical as it ensured that they were maximizing electricity production for the grid. Their design improves traditional nuclear plants by having multiple small reactors instead of one large reactor. This approach allows for shorter outages, and requires only one of the (up to 12) modules to be refueled at a time, which enables continuous power production.
NuScale needed to develop an automated toolset that could operate under demanding environmental conditions and would be responsible for the maintenance of the NuScale Power Module (NPM’s)in the VOYGR power plant.
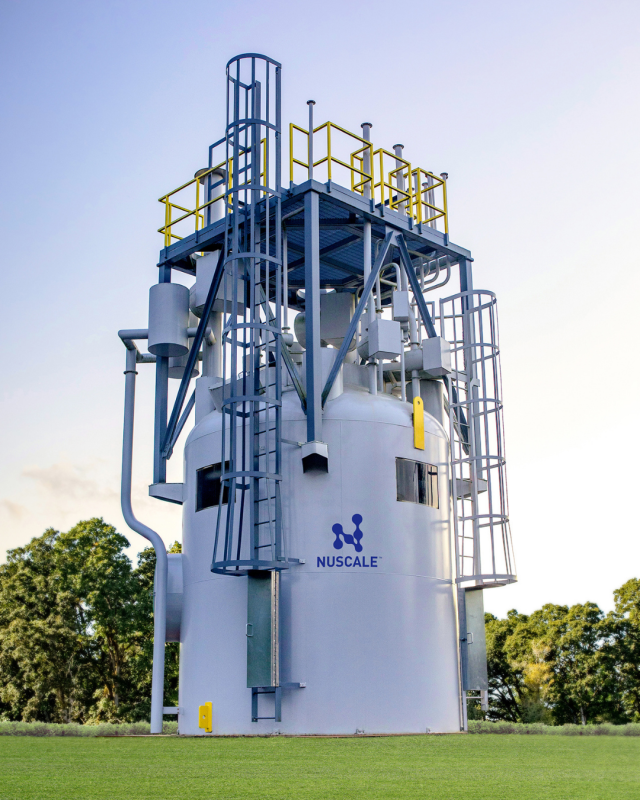
Solution
Fully Automated Tooling Offers Increased Reliability and Decreased Risk for SMR Developers
ATS Industrial Automation developed a fully automated tool set called MAEB or Modular Assembly Equipment Bolting. It is a key piece of equipment used in the process to disassemble and reassemble the Power Modules for routine maintenance, inspection, and refueling.
The system is comprised of 12 Manipulator tools, which work in symphony to autonomously perform the assembly tasks of the NPM with efficiency and reliability.
The toolset will apply the necessary force to each of the studs to ensure proper assembly of the vessels. Operating remotely, fully submerged in the refuel pool it will service each of the multiple reactor modules, which are part of the NuScale plant design.
How It Works
1. The MAEB system receives an NPM scheduled for refueling and begins the disassembly process by de-tensioning and removing the studs from the vessels. This toolset, which integrates a hydraulic tensioning system developed by Nord-Lock Group, is unlike any technology currently on the market.
2. The separation of the upper and lower vessels is what provides the plant operators access to the core, allowing it to be refueled. Other maintenance and inspection processes take place at this time.
3. Once complete, the MAEB system reassembles the lower vessels of the reactor to the upper vessel through stud installation and tensioning procedures, ensuring the critical pressure boundaries of the NuScale Power Module are achieved.
To kick off the project, ATS created a proof of principle simulation to validate NuScale’s requirements. Next a 1:1 proof of concept was developed at our site to validate the engineering design and further affirm that ATS was adhering to the functional performance requirements developed by NuScale.
Results
Nuclear Experience Leads to Strategic Partnership
This system is incomparable to any current technologies in the SMR space right now. The automated bolting system is designed to withstand any single failure with field replaceable unit concepts and addresses all contingency scenarios. The MAEB system provides an adaptable platform to facilitate additional auxiliary maintenance and inspection activities.
“ATS’s support and experience in the nuclear space was ultimately a driving factor for the partnership. They have the flexibility to meet our evolving needs and have continued to work with and support us for the lifecycle of this project.”
Dr. José Reyes
Chief Technology Officer and Co-founder of NuScale Power
ATS’s support and experience in the nuclear space was ultimately a driving factor for the partnership. They have the flexibility to meet NuScale’s evolving needs and have continued to work with and support the customer for the lifecycle of their project.
Discuss your unique SMR challenges with an automation expert in the Nuclear industry.