Medical Device Manufacturing Case Study Highlights
Company
Medical Device Manufacturer
Industry
Medical Devices
Region
North America
Customer
A medical device company specializing in the development and manufacturing of surgical instruments and sutures.
Challenge
Faced with the challenge of optimizing its suture manufacturing process, a medical device company needed a manufacturing solution for producing sutures just 0.05 mm in diameter or roughly the thickness of a human hair. All quality control measurements would need to be conducted at the micron level.
The company needed a solution that would enhance the efficiency and precision of their operations while maintaining strict standards.
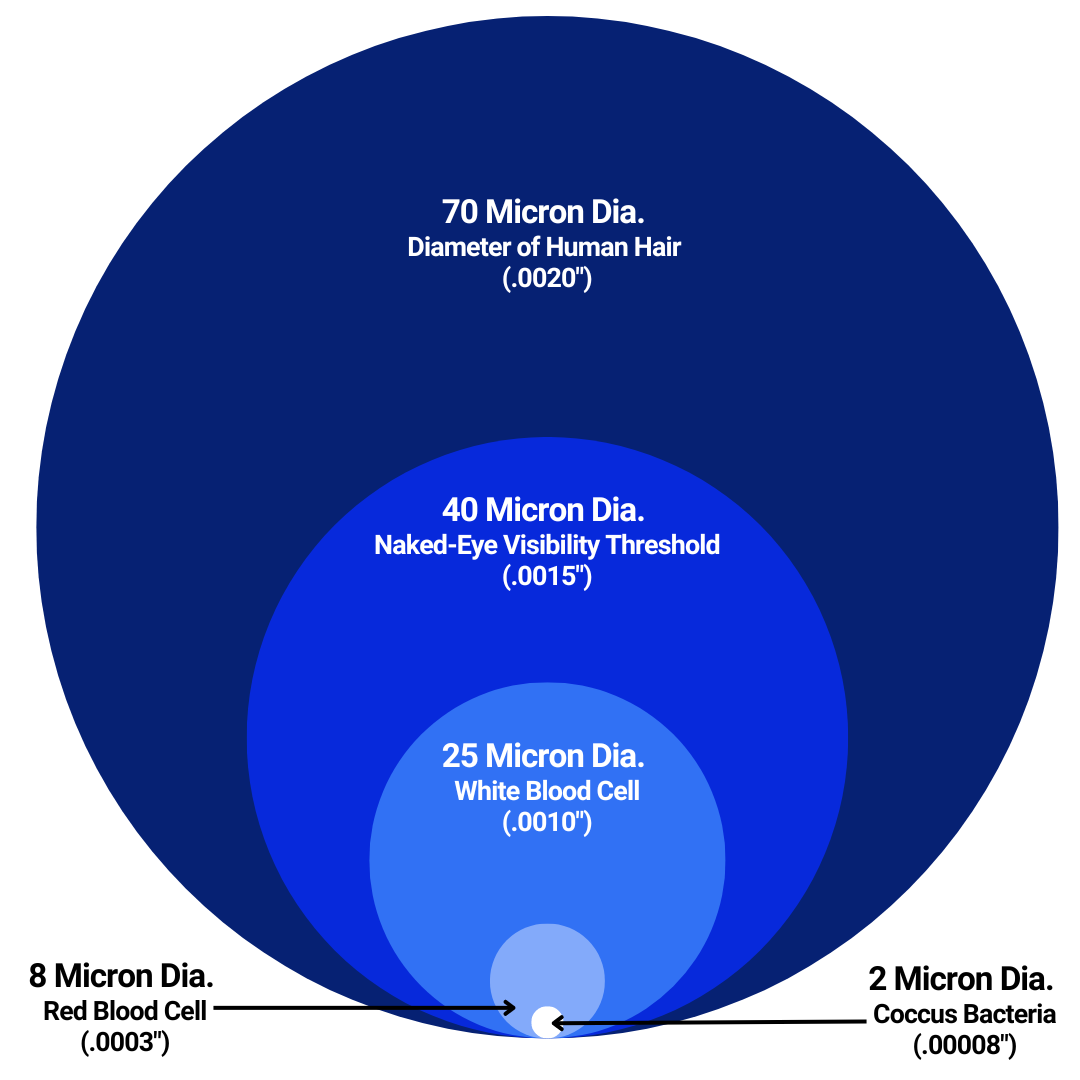
This meant developing a lean system capable of producing high-quality surgical sutures with micron-level accuracy, while reducing the footprint of the manufacturing cells. This required advanced automation, precise vision systems, laser micrometers, and real-time monitoring technology to achieve the desired outcomes.
The device manufacturer turned to ATS Industrial Automation to design and build an automated production line optimized to its unique product needs. Our experience supporting high-precision manufacturing across other industries provided us with the knowledge, skills, and technology needed to meet stringent requirements and deliver an effective and reliable solution.
Solution
ATS Industrial Automation partnered with the medical device manufacturer to develop and evolve this cutting-edge technology.
The automation technology used in this project was pivotal in bringing the solution to life. To ensure micron-level accuracy, the assembly system combines advanced vision systems, laser micrometers, and robotic automation. The system uses large spools, allowing the cell to run autonomously for 30-60 minutes, reducing the need for constant operator intervention. The suture material is drawn from the spool and a rotating blade, spinning at 2,500 – 3,000 RPMs, creates the angled slice on the surface of the suture. The vision system measures the depth of each angle every 30 milliseconds for quality control.
The suture is handed over on a pallet to the SuperTrak CONVEYANCE™ line, where primary and secondary loops are formed and secured in a weld nesting tool. The primary loop of the suture is ultrasonically welded using a welding horn that measured to a tenth of a millimeter, or about 4 grains of salt, fitting into a slot that is only 1.5 mm wide. This precise positioning ensures the highest standards of quality and accuracy. Microscopic cameras monitored the ultrasonic welding in real-time, allowing for adjustments to the positioning of the weld horn as needed. A non-destructive pull test is conducted to test the weld’s hold before the suture is threaded into a needle using a Swage machine and transferred to the finished goods bin.
To make this a cost-effective assembly solution, the team optimized the footprint of the manufacturing cells by building them in a vertical configuration, achieving a 30% space savings for the customer. Additionally, the need for only one operator to maintain the system and the SuperTrak line further reduced operational costs.
Results
The new assembly line reliably produces 1 part every 5 seconds. It significantly improves the efficiency and precision of the customer’s suture manufacturing process, while maintaining micron-level accuracy in the production. Creating this lean system with a reduced footprint of the manufacturing cells allows the cell to run autonomously before requiring operator intervention. The use of large spools and the vertical configuration further contributes to efficiency gains.
According to the customer, the ATS Industrial Automation team met deadlines and collaborated with other suppliers to ensure the timely delivery of components. To ensure a smooth transition and consistent maintenance of the equipment, our team provides comprehensive service after delivery, including real-time monitoring, in-process quality assurance checks, and the use of digital tools such as the ATS Smart Vision System for monitoring needle pick positions. This approach ensures that the equipment remains in optimal condition and that any issues are promptly addressed to maintain the high quality and efficiency of the production line.
Every automation project is unique. Allow us to listen to your challenges and let us show you how virtual reality training can help.