Machine-level virtualization has long been a cornerstone of efficient resource utilization and operational flexibility in today’s rapidly evolving technological landscape. This technology has revolutionized manufacturing by allowing multiple operating systems (OS) to run on a single physical machine.
However, as systems become more interconnected and complex, real-time performance is critical, and the limitations of machine-level virtualization are increasingly apparent. Issues such as resource allocation inefficiencies and performance overheads often hinder its effectiveness. So, how can machine-level virtualization advance to meet the demands of today’s high-precision manufacturing processes?
The Evolution of Virtualization
The concept of digital twins in manufacturing began to take shape in the early 2000s. A digital twin is a virtual representation of a physical object or system designed to accurately reflect its real-world counterpart through concurrent data and simulations. These were based on CAD-enabled 3D models, which offered a virtualized view of the design and facilitated faster iterations than paper and pencil could. Initially, digital twins would create virtual models to simulate simple machine cycles and motions.
Today, operations often require even faster iterations and more collaboration across multiple facilities. Manufacturers need to apply digital technologies beyond a single machine level and into entire production systems and workflows, enabling real-time data integration and more sophisticated simulations that drive informed decisions, optimize workflows, and save critical resources.
The Need for System-Level Virtualization
By only virtualizing individual machines, original equipment manufacturer (OEM) leaders miss out on the broader picture of their workflows, leading to inefficiencies such as bottlenecks in production lines, increased downtime, and higher maintenance costs. System-level virtualization can address the limitations of digital twins through an integrated view of the entire manufacturing line. The approach ensures all components, including machines, robots, and software systems, work together efficiently. This can optimize intricate digital environments, improve collaboration between teams, and enhance predictive capabilities—improving overall performance and reducing operational costs.
Digital Twins Evolve to Become System Twins
System twins are an evolution of digital twins, designed to provide a comprehensive, digital view of entire production systems rather than individual components. Unlike digital twins—virtual replicas of single physical assets—system twins mimic the equipment, robots, software, and other components within a manufacturing line. This includes their physical attributes, behaviors, and interactions within the operational environment.
By creating virtual systems that integrate various components of a manufacturing line, operators enable a seamless flow of information and coordination among each part of the system. System twins significantly enhance efficiency by identifying bottlenecks. A shared, accurate virtual model of the entire system lets teams see the same processes from anywhere, improving communication and collaboration. Additionally, system twins offer enhanced predictive capabilities for system performance and maintenance, allowing operators to proactively identify and resolve potential issues before they impact production. Furthermore, system twins enable the simulation and optimization of system changes. This helps ensure any modifications are thoroughly tested and refined in a virtual environment before implementation, minimizing risks and maximizing line productivity.
Take Machine Level Virtualization to the Next Level
System twins have been successfully implemented across various industries, including automotive, nuclear, and manufacturing. Companies have utilized system twins to optimize their production lines, resulting in significant efficiency and cost savings.
In the automotive industry, companies use system twins to simulate and improve the assembly of complex components, leading to better predictive maintenance and reduced downtime. By integrating system twins, one automotive manufacturer was able to reduce the overall power consumption of their production lines by 30%, demonstrating a substantial impact on operational expenses.
Finally, in the manufacturing sector, system twins have enabled companies to virtually replicate and refine lines or systems, ensuring any changes are thoroughly tested before executing them in production. This has led to measurable improvements in performance.
As manufacturing systems increase in complexity, OEMs need digital solutions to save critical time, enhance throughput, and reduce costs. System twins enable teams to bring their systems a step closer to becoming a digital factory and meet market demand.
Discover how to leverage the power of system twins today.
Download our Free eBook to learn more about why System Twins are Eating Complexity for Lunch (And dinner. And breakfast.)
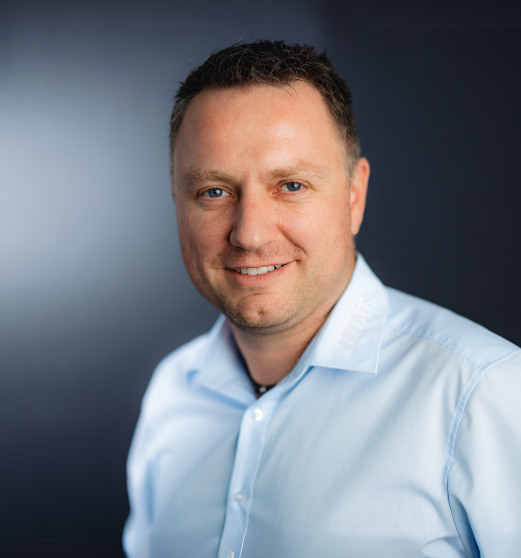
Roland Echter
General Manager - Digital
ATS Industrial Automation
Roland has helped companies across numerous industries to automate and optimize production with digital solutions. Roland works with customers to configure services, systems, using digital tool strategies to build and scale production and drive operational efficiency.