Acceptance criteria serve as a scorecard to determine whether a piece of automated equipment performs the tasks it was designed to do. They include metrics such as cycle time, the number of faults, and machine availability.
Clearly defined criteria help manufacturers save resources and verify that the delivered machine meets the expectations of the customer and project team, without requiring costly modifications. The criteria also help teams avoid project delays and communication issues, both of which are common pitfalls in the manufacturing industry. By setting detailed acceptance criteria early in the project lifecycle, manufacturers can ensure that their equipment meets the desired quality standards and operates efficiently, ultimately leading to successful outcomes.
According to a study by the Project Management Institute (PMI), 37% of project failures are attributed to a lack of clearly defined objectives and milestones to measure progress. This statistic highlights a significant issue: many assembly line and equipment purchases are delayed due to the need for rework, especially when criteria are not properly identified from the start. Poor communication further exacerbates this problem, with 30% of project managers citing it as a primary cause of project failure. When selecting your automation partner a lack of discussion around acceptance criteria could be a red flag. When acceptance criteria are not clearly established, it leads to misalignment between the customer and automation partner. This can result in equipment that does not meet required standards and necessitates costly and time-consuming adaptations.
What is a “Correctly Made Component”?
In manufacturing, it’s crucial to know what constitutes a “correctly made component”. It ensures that all stakeholders know what a good part looks like. Otherwise, subjectivity can result in parts that do not meet quality standards, leading to increased scrap rates. For instance, specifying “no scratches” on a part might seem straightforward, but it requires detailed parameters to avoid unnecessary costs. A human eye can only see scratches of a certain size, while a machine can consistently detect even the smallest imperfections.
Without clear acceptance criteria, the process becomes subjective, leading to inconsistencies and additional work. Ultimately, it’s essential to define a correctly made component to achieve high-quality, cost-effective production.
Challenges of Defining Acceptance Criteria
While agreeing on acceptance criteria is important to the outcome of the project, clearly outlining this criteria often presents several challenges Such as under-defining or over-defining these parameters. Under-defining can lead to equipment that fails to meet quality standards, while over-defining can drive up costs. It is crucial to find a balance by setting clear, realistic criteria with your automation partner that align with the project’s goals and any possible limitations. An experienced automation partner can help manufacturers identify these specifications, leveraging their expertise to help leaders avoid common pitfalls.
When it comes to line requirements, the product development team, manufacturing team, and automation partner must be on the same page to ensure the equipment meets the specific needs of the project.
Clear communication is vital to achieve agreement between all parties. The customer should ask specific questions, including:
- What are the end goals for the product and automation equipment?
- How many parts do we need by the end of the year?
- What are the current scrap rates? What quality standards need to be met?
These questions help teams define achievable acceptance criteria, so each piece of equipment performs as expected. By maintaining open and transparent dialogue, teams can work together to understand and achieve these important specifications, ultimately leading to successful project outcomes.
Common Acceptance Criteria in Automation
There are several essential benchmarks that teams can use to evaluate whether the automated equipment will meet the desired performance and quality standards. These criteria typically include metrics such as cycle time, machine availability, and the number of faults.
Overall Equipment Effectiveness (OEE)
Overall equipment effectiveness (OEE) is a key metric used to evaluate manufacturing equipment. It combines three critical factors: availability, performance, and quality. These provide a comprehensive picture of how well each piece of equipment is operating. Companies use OEE to identify areas for improvement and optimize production processes. When using OEE as an acceptance criterion, it is important to set targets that align with project goals and constraints. For instance, world-class equipment typically operates in the 85-90% range, but setting a target that’s too high, such as 99%, can drive up costs and lead to unnecessary complexity in design. Clear communication can help teams set realistic OEE targets.
Pass and Fail Criteria
Pass/fail criteria can help manufacturers determine whether a component or product meets predefined quality standards in an automated manufacturing process. These benchmarks ensure that only components that meet the required specifications proceed to the next stage of production, maintaining quality and reducing potential defects. When defining pass and fail criteria, teams must consider the product’s unique requirements, such as dimensional tolerances, surface finish, and functional performance. Clear parameters help manufacturers avoid subjective judgments and drive consistency in production. Additionally, it is important to match criteria with the overall project goals and share them with all stakeholders. This ensures that equipment is designed and built to meet the manufacturer’s specific needs.
Cycle Time
Cycle time is a critical equipment acceptance criterion in manufacturing. It refers to the total time it takes to complete one cycle of production, from the start of one unit to the start of the next. Manufacturers use cycle time to measure the efficiency and productivity of their equipment and optimize production processes to meet demand. When defining cycle time, it is important to consider the line’s specific requirements, including the desired output rate, the complexity of the tasks involved, and the capabilities of the equipment. Setting realistic cycle times helps maintain a balance between speed and quality, avoid unnecessary strain on the equipment, and facilitate consistent production.
Testing Criteria and Specifications
Testing parameters are essential components of equipment acceptance criteria. They define the specific tests and measurements that a piece of automation equipment must pass to be considered acceptable. Manufacturers use these benchmarks to verify the machinery meets required performance and quality specifications, thereby reducing the risk of defects and ensuring consistent production workflows.
When defining testing benchmarks, it is important to consider the exact requirements of the product and manufacturing processes. This includes determining the types of tests needed, such as pressure, continuity, or volumetric tests, and specifying acceptable ranges for each one. Clear criteria help leaders avoid subjective observations and evaluate the equipment accurately.
Safety Factor Communication
Safety factor communication refers to the practice of incorporating a margin of safety into the equipment’s design and behavior, accounting for uncertainties and potential variations in performance. Manufacturers use safety factors to ensure each piece of equipment operates reliably under a range of conditions, minimizing harm to workers and the risk of failure while enhancing safety.
When defining safety factors, the manufacturer must consider any specific equipment requirements, the potential risks involved, and acceptable levels of performance variation. Clearly communicating safety factors helps everyone align on the expectations of the equipment, leading to successful project outcomes—and ultimately, a stronger production environment.
Choosing an Automation Partner
Manufacturers that want to achieve their internal and external manufacturing targets must consider engaging a trusted partner, rather than a supplier. An experienced automation partner brings a collaborative approach, working closely to understand each customer’s unique needs, challenges, and goals. This partnership enables automation solutions to be tailored for specific manufacturing targets, such as reducing critical downtime and enhancing product quality or specific processes. By aligning each step of the automation strategy with the manufacturer’s objectives, an experienced partner helps drive continuous improvement and long-term market success.
An automation partner will also prioritize effective communication so all stakeholders can agree on project requirements, timelines, and expectations. This helps identify any potential challenges early on and develop strategies to address them. Regular updates and feedback between teams can also lead to better decision-making and successful project outcomes. By working with an automation partner who prioritizes ongoing communication and aligns with the manufacturer’s strategic goals, businesses can ensure their automation initiatives will support their production targets.
Every project is unique. Allow us to listen to your challenges and share how automation can launch your project on time.
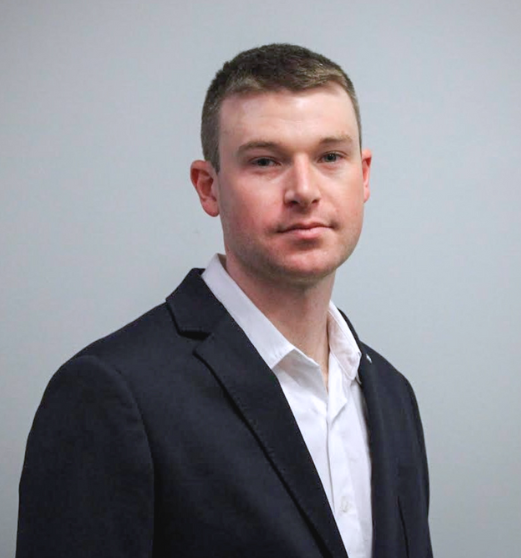
Kevin Peake
Key Account Manager
ATS Industrial Automation
Kevin has helped companies across numerous industries automate and optimize production. Kevin has a Bachelor of Science in Aerospace Engineering and Mechanical Engineering, he loves robots and has built them in his basement for fun. He enjoys helping customers configure systems to build and scale production and drive operational efficiency.