Launching a new product in an emerging industry, such as electric vehicles (EV) or grid storage batteries, or even for established hyper-competitive markets, is challenging. Many companies are racing to develop next generation technology that powers a better future. Yet, designing a state-of-the-art product is only half the battle. Bringing it to market at scale requires working with partners to ensure manufacturability and having efficient, reliable manufacturing equipment.
A well-designed product needs to be supported by a well-planned approach to manufacturing. Companies must be proactive regarding manufacturability to ensure a successful product launch. Starting early and engaging with an automation partner are important steps in developing automated assembly lines to meet your production goals and stay on schedule and on budget.
Establish Well-Defined Requirements
When taking a product from concept to prototype and into production, many companies begin with manually assembled prototypes before shifting to fully automated production lines. However, moving from a manual process, where operators can guide and align parts with precision, to high-speed automated assembly introduces significant challenges, as machines lack the tactile feedback of human touch. Therefore, understanding both product design and process requirements is crucial when designing effective high-speed automated assembly lines.
Basic manufacturing specifications—such as product dimensions, materials, production volumes, and quality standards—are needed for automation partners to design and build equipment and assembly systems. Missing critical details or working with vague, unknown project specifications can easily lead to complications and uncertainty, creating delays and friction for both the manufacturer and their automation partner.
One way to refine product requirements is to focus on the desired quality of the end product and how it will be validated. By planning for automated testing at the end of the manufacturing line, manufacturers can establish the right requirements to guide the design of the assembly process. End-of-line product validation ensures that each product meets the quality standards expected by downstream customers. This approach allows manufacturing leaders to “begin with the end in mind.”
Setting clear, well-documented requirements help align all parties on the project scope, deliverables, schedule, and risks. This leads to a streamlined process of design and build, and can result in a more efficient assembly line.
Adopt a Design for Manufacturability Mindset
Another way to set clear requirements is to work with your automation partner to implement design for manufacturability (DFM) principles. The product design and equipment teams work closely together to co-develop product changes, making your product easier to manufacture. All parties can lean on their own expertise to come together with a solid understanding of production line requirements early in the development process.
Adopting a DFM approach from the start enables manufacturers and partners to anticipate potential challenges early, minimizing production delays. This method leverages each partner’s core expertise to design a product that is easier to manufacture using readily available parts, equipment, and proven processes. It also simplifies equipment needs, reduces downtime, and improves product quality.
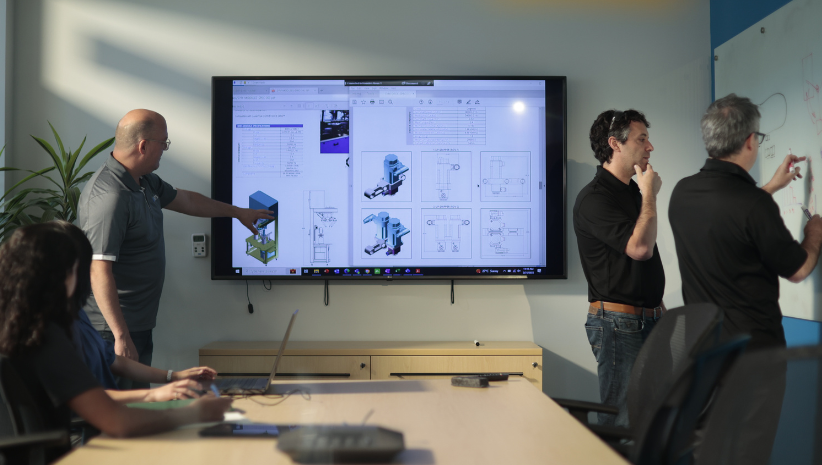
Evaluating assembly feasibility, material options, and manufacturing processes enables companies to address issues before they escalate. With simultaneous engineering, where design and development processes occur in parallel, companies can reduce the time it takes to get a product from concept to market launch. It involves bringing together engineers from design, manufacturing, testing, and quality control early in the development process. This collaboration between the product managers and the automation partner helps identify potential adjustments for the assembly line early, reducing the need for significant changes after the line is built.
Anticipate Change Requests
Even with a well-defined product design and set of requirements, change can and will happen—especially in emerging markets such as grid or EV batteries, where technology and materials constantly evolve. For example, updates to product dimensions, process changes such as welding and adhesives, or even materials can have a cascading impact down the assembly line, often requiring adjustments to systems, machinery, processes, testing protocols, or quality control measures. When this happens, all partners must reassess the completed work and ensure that it can be adapted to any new requirements.
Effectively communicating and managing change requests requires a defined process. This includes allocating time and resources to assess any change’s potential impact on downstream processes, deliverables, and costs before implementation. Each change should be documented, clearly outlining the responsibilities and the implications for the customer and the automation partner.
Digital twin technology can aid in evaluating and mitigating the effects of changes across the production line through simulations, allowing companies to test adjustments before physical implementation. This helps reduce integration efforts once changes are made and ensures modifications are feasible, reducing unnecessary investment in materials and time.
Change requests will happen. Setting clear procedures from the start helps prevent misunderstandings about the changes, who is requesting them, and any impacts of the scope changes . Well-defined and documented processes help manufacturers and their partners plan and make modifications to mitigate disruptions and confusion which can cause production line delays.
Delivering a Manufacturing Line to Schedule
Successfully delivering an automated assembly manufacturing line schedule requires a thoughtful approach that combines flexibility with a structured framework for managing changes. Success requires strong collaboration among all stakeholders and clearly defining project requirements from the outset. Companies and their automation partners can mitigate risks and prevent delays by emphasizing effective communication and early-stage design coordination, ensuring a smooth transition from design to full-scale production. This strategic approach to factory automation allows manufacturers to bring their products to market on time, even in fast-evolving industries where innovation and change are constant.
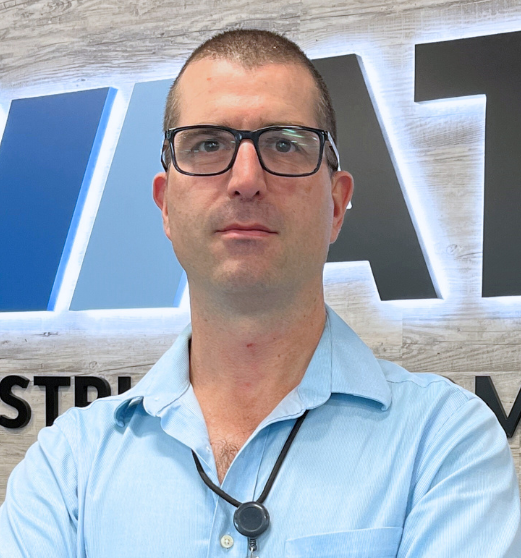
Rob Turton
Program Manager
ATS Industrial Automation
Rob has over 20 years of experience helping companies across numerous industries automate their assembly and testing lines. Rob specializes in managing large-scale programs and works with customers to optimize production lines and drive operational efficiency.