Taking a product idea from concept to full-scale production is no easy task. Launching a “first of its kind” product can take months, years, or even decades, depending on the industry. As manufacturers move from ideation to design to proof of concept, they can begin planning for the next stage – building low- to high-volume automated production lines.
At this stage, any production launch delay can have significant consequences. Delays increase costs, harm reputations, and frustrate stakeholders. By understanding the most common causes of delays and implementing strategies to mitigate them, manufacturers can stay on track and deliver products on time.
Causes of Production Delays
In recent years, supply chain disruptions have been significant contributors to production delays, whether due to a pandemic, extreme weather events, transportation issues, material shortages, or geopolitical events. Production grinds to a halt when the supply of critical components doesn’t arrive on time, or they arrive damaged or fail to meet quality standards.
However, supply chain and quality issues are just two factors that can cause production delays. When planning production lines, consider the following:
Insufficient Workforce: It can take time to attract and train skilled workers. This is especially true if you build innovative, new products such as EV or grid storage batteries. Without enough trained workers, the production launch and ramp-up process cannot be efficient.
Functional Requirement Failures: During line testing and low-volume production, products may fail to meet functional requirements, such as power, voltage, or torque specifications. These failures could be caused by poor-quality parts, equipment issues, or control processes. Troubleshooting these problems can be time-consuming as parts, equipment, and specifications must be verified.
Moving at a Blazing Speed to Market Can Be Hard to Predict: Overambitious deadlines can derail production if teams are operating toward unachievable goals. Additionally, evolving market or customer demands—common in emerging industries like grid energy or electric vehicles—can alter product designs and functional requirements, impacting equipment and schedules.
Getting industrial product manufacturing right the first time is hard to achieve. Developing automated production processes and machinery can be complex, especially if it’s never been done before. By anticipating the common causes of delays and planning accordingly, manufacturers can better manage their production processes and avoid costly setbacks.
Best Practices to Stay on Track
With over 45 years of experience in automated manufacturing, ATS Industrial Automation excels at designing and building high-speed automation systems tailored to specific product and manufacturing needs. Our expertise ensures that production systems meet functional requirements while helping customers avoid potential issues.
Here are our best practice tips to minimize launch delays and keep your production lines running smoothly.
1. Leverage Subject Matter Expertise
While companies can isolate issues or requirement gaps into a few areas, resolving it may require specialized expertise. At ATS, our experts specialize in various technologies—dispensing, welding, testing, or another discipline— and have in-depth practical knowledge of the challenges, technologies and solutions related to their field. Our experts collaborate closely with customers to troubleshoot and identify solutions to the most challenging production issues.
2. Create Virtual Manufacturing Line Simulations
For complex or first-of-its-kind production lines, virtual simulations using digital twin technology can accelerate line development. Virtual testing allows you to simulate machine performance and emulate the operative components of the physical line. Testing, integration, and commissioning — generally done after the line is physically built — can happen sooner. Companies can run operational scenarios and identify and correct potential issues early, avoiding costly delays further down the road.
3. Develop Comprehensive Operator Training
Detailed staffing and recruiting plans are crucial, but proper training ensures success. Partner with your automation provider to build robust training programs that include onsite sessions, detailed documentation, and immersive virtual reality simulations.
ATS’s UReality software allows for the quick creation of 3D training simulations, which can be shared across teams, ensuring consistent learning and onboarding for new employees. Workers can feel confident they are properly trained on equipment and know-how to maintain and troubleshoot equipment, reducing downtime.
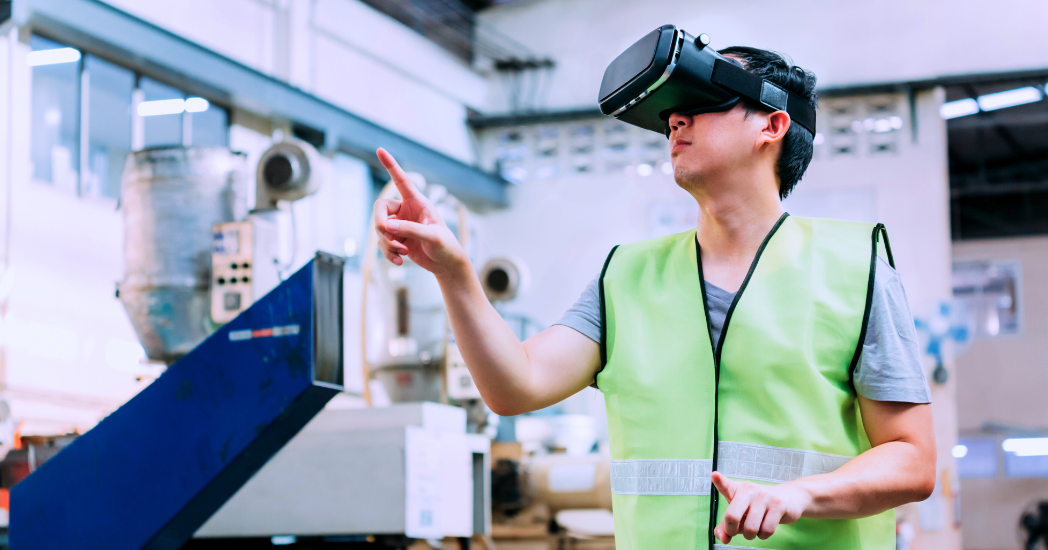
4. Adopt Modular Assembly Solutions
Changes to product designs or specifications late in the planning process can lead to production delays. Implementing modular assembly equipment and digital technology, such as the SuperTrak CONVEYANCE™ Platform with SYMPHONI™ technology, makes it easier to scale up and adapt to process changes or new products. This gives manufacturers greater agility, flexibility, and utilization to ensure that products launch on time.
5. Implement Production Monitoring Software
Successful production lines rely on real-time monitoring tools like Illuminate™ Manufacturing Intelligence software to provide data-driven insights into equipment line performance.
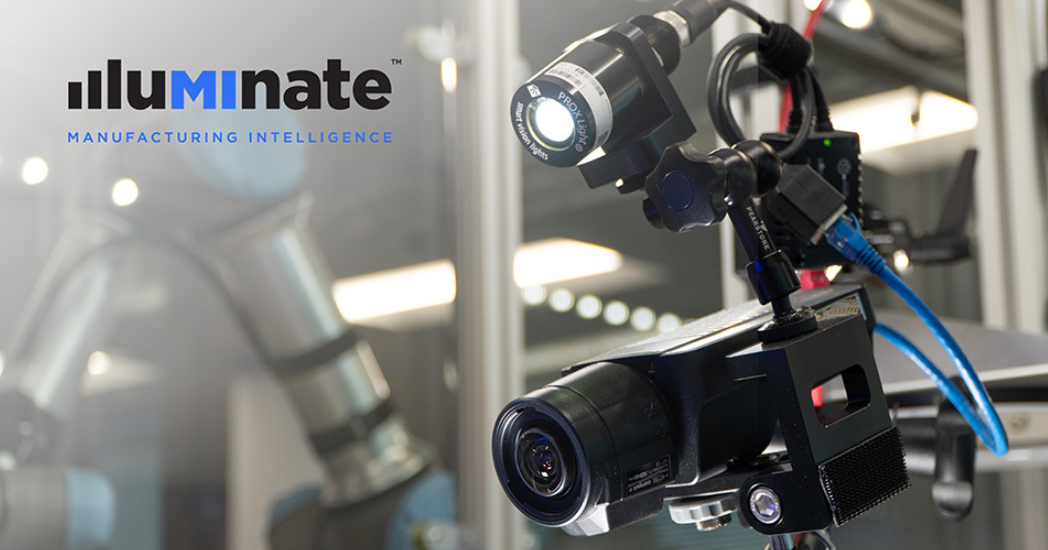
Our machine builders use this software to fine-tune assembly systems before delivery, and then it remains with the system throughout its lifespan. It tracks key metrics such as uptime, availability, and yield and helps identify bottlenecks and underperforming stations. With monitoring software, companies can improve machine reliability and minimize disruptions, creating more efficient production lines.
Stay Ahead of Delays with the Right Strategy
Production delays can lead to costly setbacks and in turn cause product launch delays, but with proactive strategies and realistic timelines, companies can stay on schedule. Investing in real-time monitoring, tapping into expert knowledge, utilizing digital twin simulations, and providing effective training will help companies avoid common pitfalls. At ATS Industrial Automation, our extensive experience delivering over 3,000 production lines has equipped us to work with customers through every stage of assembly line automation, ensuring high-quality outcomes and timely product launches.
If you need help keeping your automated manufacturing lines on schedule, are experiencing functional failures, or are developing a new line, we can help. Contact us today to schedule an informal discussion.
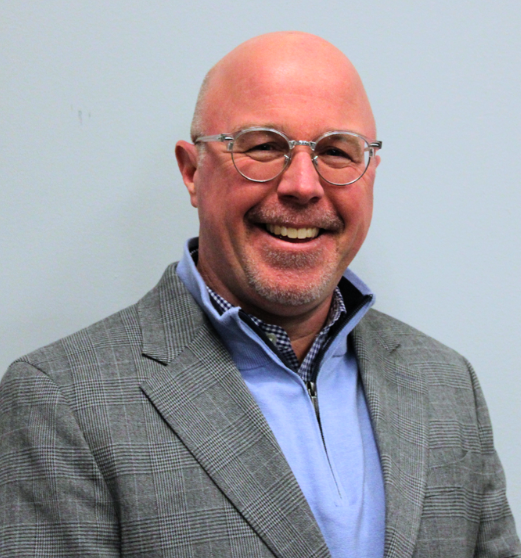
Kirk Blair
Director of Sales, Mobility
ATS Industrial Automation
Kirk has helped companies across numerous industries to automate and optimize production lines for over 20 years. Kirk works with customers to configure systems and service strategies to build and scale production and drive operational efficiency.