The demand for nuclear energy is on the rise. Communities and businesses across the globe are demanding access to affordable, reliable, clean energy. According to the Nuclear Energy Institute (NEI), President and CEO Maria Korsnick, last year grid planners across the globe, nearly doubled the 5 year growth forecast. During her State of the Nuclear Energy Industry 2024 address, she also claimed that a recent study from Grid Strategies predicts the grid will need to add 38 GW, or more, of new electricity during the next five years, driven by advanced computing, artificial intelligence, and the electrification of the manufacturing and transportation sectors.
This demand could mean hundreds of new reactors coming into operation over the next several years, with many projected to be advanced or small modular reactors (SMR). SMRs offer several potential benefits but must overcome several challenges to become a reality for a broader market. Technology, including automation, plays a pivotal role in overcoming these challenges.
What is a Small Modular Reactor?
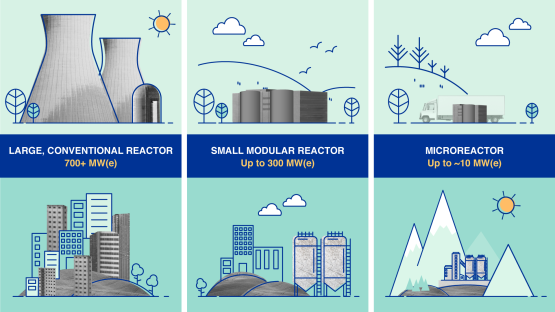
SMRs are advanced nuclear reactors that have a power capacity of up to 300 MW(e) per unit, which is about one-third of the generating capacity of traditional nuclear power reactors.
SMRs are envisioned for markets such as industrial applications or remote areas with limited grid capacity and aim to produce large amounts carbon-free electricity.
Benefits of Small Modular Reactors
Many of the benefits of SMRs are inherently linked to the nature of their design – as their name suggests, they are small and modular. Given their smaller footprint, SMRs can be located in areas not suitable for larger nuclear power plants. Additionally, prefabricated units or modules can be manufactured in a factory setting and then shipped and installed on site, making them more affordable to build than large scale power reactors, which are often custom designed for a particular location; this often times leads to construction delays and cost overages. SMRs offer savings in initial capital cost and construction time, and they can be deployed incrementally to match increasing energy demand.
SMRs offer the promise of inherent safety features, simplification and standardization that could make nuclear capacity far easier and more economic to deploy, and significant advancements in terms of the overall flexibility of nuclear energy in meeting future energy needs.
But can this vision become a reality? And what role will technology play?
Challenges Small Modular Reactor Designers are Facing
Difficulties encountered by recent nuclear projects based on traditional large nuclear reactor designs, have offered valuable learnings but also highlight the need for alternative nuclear technologies such as advanced reactors and SMRs, that are more affordable and easier to construct.
The current phase of SMRs in development are already exploring and benefiting from various technological solutions as a means to help overcome challenges.
Let’s explore these challenges in more depth and better understand how technology is helping them overcome many hurdles.
Small Modular Reactor Design and Construction Overview
According to a report published by the Nuclear Energy Agency (NEA), currently there are at least 75 SMR concepts at various stages of design and development and there are significant differences being seen across the major types. The degree of modularization also varies across designs, adding a layer of complexity when it comes to approvals and licensing compliance in this highly regulated industry.
Fortunately, SMRs should see shortened learning curves when it comes to the design, build, and deployment of their reactors in comparison to larger reactors due to higher degrees of modularization, design simplification and standardization. Furthermore, SMRs will benefit from “series construction”, such as seen in the aircraft industry, where factory fabrication provides enhanced quality control and reduced construction risk through the introduction of newly automated manufacturing techniques.
As mentioned above, SMRs are modular in nature which makes them particularly suitable for factory assembly. SMR builders will fabricate major components of the nuclear reactor in a factory environment and ship to the end location for final assembly. Factory construction allows higher quality components to be produced in a tighter timeline whereas, large scale nuclear power plants are typically constructed in the field at the final location of the power plant. Field construction requires the specialized workers to travel to and be located on-site, leading to increased costs and longer timelines.
Introduction of Automation – Cost Management and Project Timelines
The goal for SMRs is to limit on-site or field construction. This in turn, will substantially reduce the lengthy construction timelines typical of larger units. Due to their modularity and small size, it is predicted that SMRs will offer shorter delivery times, improved quality and efficiency, and reduced upfront investment.
SMRs are also enabling more ambitious manufacturing techniques and are opening the door to leverage how factory automation can play a larger role in optimizing their processes. Once a stable and repeatable process has been established, the introduction of automation allows for additional modules to be easily added incrementally as demand for energy increases.
Though SMRs are projecting to have lower upfront capital cost per unit, their economic competitiveness on a levelized cost of electricity basis, is still to be proven in practice once they are deployed. Automated technologies, however, are being credited as a tool for increased efficiency, resulting in keeping upfront costs down and project timelines on track.
How Automation Facilitates a Reduction in Technical Complexity
In many cases, SMR designs are typically simpler compared to existing reactors. But because the designs are new, an innovative approach is required and often involves some form of technology or automation as seen in the example above.
Another good example of design simplification is the refueling process. Many current SMR designs require the reactors to have reduced fuel requirements, or in the case of NuScale’s VOYGR™ SMR plant, the refueling process has been made much more efficient through automation.
As part of the VOYGR project, NuScale partnered with ATS to develop a first of a kind technology called MAEB or Modular Assembly Bolting Equipment. MAEB is a key piece of equipment used in the process to disassemble and reassemble the Power Modules for routine maintenance, inspection, and refueling.
The system is comprised of 12 Manipulator tools which work in symphony to autonomously perform the assembly tasks of the NuScale Power Module with efficiency and reliability.
The toolset will apply the necessary force to each of the studs to ensure proper assembly. Operating remotely, fully submerged in the refuel pool, it will service each of the multiple reactor modules, which are part of the NuScale plant design.
Learn more about how it works.
Minimizing outage time is critical for NuScale as it ensures that they are maximizing electrical production for the grid. Their design improves upon traditional nuclear plants by having multiple small reactors instead of one large reactor. This approach allows for shorter outages and requires only one of the (up to 12) modules to be refueled at a time, this enables continuous power production. The design of the NuScale plant and the refueling process allows for a significant reduction from a typical refueling outage and demonstrates how automation was used to increase efficiency and demonstrate feasibility of the SMR technology to a larger market.
Streamlining SMR Safety and Compliance with Technology
Although there has been a strong focus on how technology is aiding in construction, it can also impact what is arguably one of the largest challenges currently facing SMR designers; regulatory and safety compliance.
Much like the traditional reactor landscape, the SMR space is governed by stringent regulations, involving intricate licensing requirements and significant regulatory commitments that must be fulfilled. As mentioned earlier, with over 75 current design concepts under development, covering a wide range of technological approaches and maturity levels, this further complicates the approval process. Although headed in the right direction, large scale deployment of SMRs requires considerable effort in order to come to fruition.
Where we see technology playing a significant role here, is helping to fast-track licensing compliance through feasibility studies, digital twins, simulations, pilot facilities and the development of proof-of-concept technologies.
While simulation technology has been used in the nuclear space for quite some time, it seems to be gaining traction in the SMR space. This includes the use of high-fidelity simulations to support regulatory agency acceptance as well as for upfront engineering and design, optimization, and ongoing O&M.
Referring back to the MAEB project completed for NuScale Power, a high-fidelity simulation was created to demonstrate the full systems cable behaviour and ensure optimal functionality of the system early in the design phase.
Building off the simulation, a proof-of-concept system was developed and tested; and could now be used to validate design approval. It will also showcase NuScale’s innovative approach to advanced reactor technology and potentially help to attract additional funding in order to scale up subsequent manufacturing capabilities.
The simplified design features inherent to the compact size of an SMR enhance its overall safety appeal. However, the limited experience with these new designs presents challenges in demonstrating their safety and obtaining necessary approvals.
Furthermore, because many SMR facilities are expected to be constructed in remote areas with limited on-site resources, remote monitoring and diagnostics capabilities could be an ideal solution—provided the associated cybersecurity and regulatory challenges are addressed.
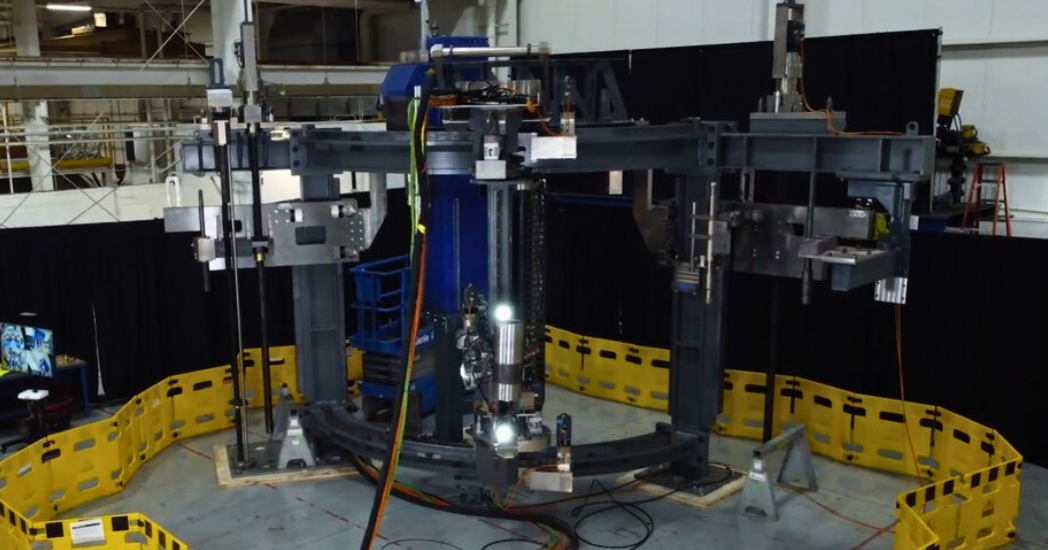
SMRs can play an important role in the progression to renewable, carbon-free power generation. They represent an exciting opportunity for new forms of nuclear generation and are making steady progress in becoming commercially viable nuclear power.
However, significant challenges remain. Fortunately, there is immense potential for technological innovation at multiple levels to address these hurdles. From cutting-edge automated manufacturing techniques and plant optimization to the development of simplified design concepts and the creation of advanced simulations and proof of concepts, technology will undeniably be pivotal. With strategic technological advancements, the industry can overcome these obstacles and revolutionize the future of SMRs.
Talk to a member of our Nuclear team to learn more about how our automated solutions can help solve your refurbishment challenges.
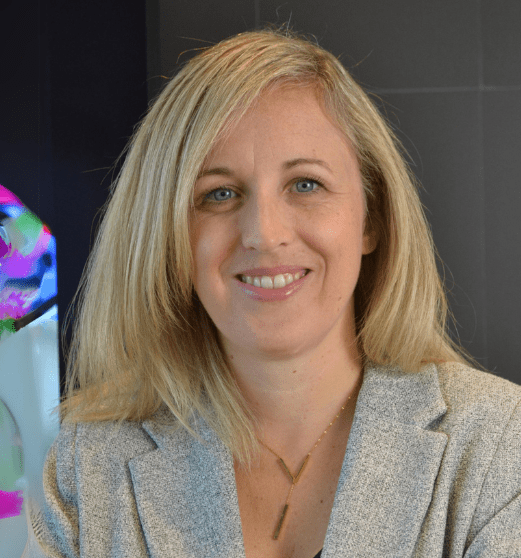
Holly Ritchie
Nuclear Marketing Manager
ATS Industrial Automation
Holly Ritchie is the Nuclear Marketing Manager at ATS Industrial Automation, bringing over 20 years of marketing experience across diverse industries, including health and safety and automation technology. She holds an Honours degree in Communications and Sociology, along with a postgraduate degree in Public Relations.