When a product delay can cost between 15% to 35% of the product’s net present value, finding ways to reduce or eliminate production delays is imperative. As a result, companies are rethinking how they design products using a design for manufacturability (DFM) approach that considers manufacturing processes early in a product’s design phase. The goal is to simplify production, enhance product quality, reduce costs, and prevent production delays.
Common Causes of Production Line Delays
Understanding the root causes of production line delays is crucial for ensuring a smooth and efficient manufacturing process. Products that were successfully manufactured in a prototype or low-volume setting may encounter issues when scaled up to high-volume production. The more products being assembled at faster rates, the higher the chance of problems within the assembly line.
This is because processes that worked well in earlier stages often fail to meet standards when scaled up. If assembly process steps cannot scale correctly, they can create product defects. Often times processes need to be reworked and potentially require new assembly and testing equipment.
Addressing these issues early in the product design phase by implementing a DFM mindset is essential for a smooth production line launch.
Implementing Design for Manufacturability (DFM)
DFM focuses on designing products so they are easy to manufacture. By incorporating DFM principles early in product development, companies can identify potential manufacturing issues before they arise, for an easier transition from prototype to high-volume production.
To effectively implement DFM during the ideation and proof of concept stages of a product lifecycle, consider the following:
- Early Integration of DFM Principles: Incorporate DFM in the ideation phase. Can parts be standardized? Is the design compatible with available assembly line processes and equipment? Are tolerances and specifications realistic? What is the cost of production, and can the process be scaled? This helps ensure products are designed with efficient manufacturing in mind.
- External Feedback: Engage external assembly and testing experts to provide feedback that the design and proposed manufacturing process is suitable for high-volume production.
- Simplify Design: Focus on simplifying product components, materials and assembly processes to reduce complexity and enhance manufacturability. However, it is also crucial to maintain the product’s unique features or intellectual property (IP). This balance can be achieved by carefully evaluating which components and processes can be simplified without affecting the core attributes that define the product’s uniqueness.
Utilize Proof-of-Principle Testing
Proof-of-principle (POP) testing plays a crucial role in reducing production delays and physically validating the results of DFM. By conducting POP tests, companies confirm that designs are not only theoretically sound but also feasible for high-volume production.
Physically Validate DFM Results:
- Real-World Testing: POP testing involves conducting real-world tests on prototypes to validate that the design can be manufactured as intended. This physical validation ensures the design meets manufacturability standards and can be produced without issues.
- Feedback and Refinement: The results from POP tests provide valuable feedback that can be used to refine the design and manufacturing processes. This iterative process helps ensure that the final design is optimized for manufacturability and can be produced efficiently and cost effectively.
- Risk Mitigation: By validating the design through POP tests, companies can mitigate the risks associated with scaling up production.
Let’s Look at a Real Use Case for DFM
An automotive original equipment manufacturer (OEM) was facing significant challenges in scaling the laser welding process for its new battery module.
During the early stages of production, the laser welding process worked well. However, scaling from 100 modules a day to 1,000 introduced more variables. The battery module used a hybrid welding process to join two different metals together, which increased the heat generated near the battery cells and heightened the risk of thermal events. These risks could compromise the safety of employees and the integrity of the battery module.
The automotive OEM partnered with ATS Industrial Automation to utilize DFM to evaluate and refine its laser welding process without compromising the battery’s unique design.
The ATS Industrial Automation laser lab played a pivotal role in running sample trials and providing valuable recommendations for process changes. Using DFM principles, the ATS team recommended changing the material of the module case to reduce the heat during the welding process, which would lower the risk of a thermal event. The automotive OEM took the results of the POP study and modified their battery design to optimize it for manufacturability.
Streamline Your Production Line Development Today with DFM
Ready to streamline your production line, reduce the risk of delays, and save money due to rework costs with DFM? For expert assistance and guidance, reach out to ATS Industrial Automation. Our team of assembly and testing experts can provide valuable insights and support to optimize your manufacturing processes.
Every project is unique. Allow us to listen to your challenges and share how automation can launch your project on time.
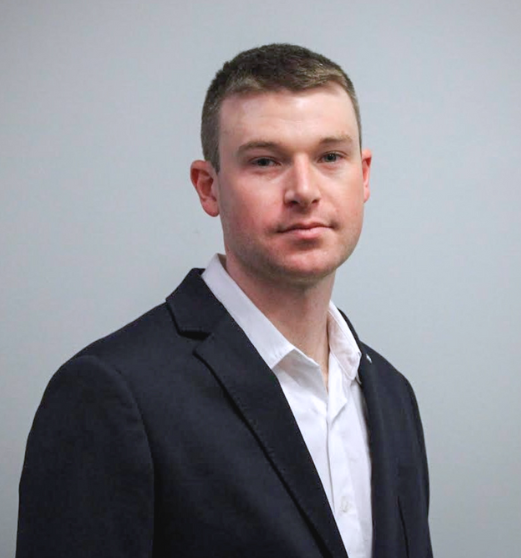
Kevin Peake
Key Account Manager
ATS Industrial Automation
Kevin has helped companies across numerous industries automate and optimize production. Kevin has a Bachelor of Science in Aerospace Engineering and Mechanical Engineering, he loves robots and has built them in his basement for fun. He enjoys helping customers configure systems to build and scale production and drive operational efficiency.