Imagine a world where you can test and perfect your manufacturing processes without touching a physical product. Welcome to the era of digital twins, where virtual replicas of production lines, products, and even entire supply chains are digitized—revolutionizing how teams design, optimize, and maintain manufacturing operations.
With only 29% of global manufacturing companies already implementing digital twin strategies, it’s clear this technology isn’t just a futuristic concept but a present source of advantage, or even leverage.
1. Digital Twin Applications in Product Design
Digital twins play a significant role in product design, serving as virtual prototypes. Digital twins can test unlimited simulations or designs before manufacturers invest in a solid prototype. This approach to product design saves time and critical costs by reducing the number of physical iterations needed before production.
2. Derisk Automation Investments with Virtual Commissioning
Digital twins can be used to enable virtual commissioning, which can then be used to test a new automation system’s performance, such as takt time and throughput, in a simulated environment. Virtual commissioning enables the identification and resolution of potential issues before the physical line is built, reducing the risk of downtime and ensuring a smoother transition to installation and ramp-up of the system.
3. Process Optimization with Digital Twin Simulations
Digital twins also enhance process optimization. They create a structural and operational view of what will happen when changes occur in the future state. This lets engineers see how adjustments impact the system digitally—before implementing them in real life.
Digital twins in manufacturing also support live systems. By using sensors on a production line, a digital twin can analyze essential performance indicators at a more granular level. Adjustments can help teams identify new ways to optimize production, reduce variances, and practice root-cause analysis.
4. Digital Twins are Enhancing Training
Traditional training methods struggle to stay relevant in an increasingly digital world. Digital twins optimize training by enabling virtual reality (VR) training, transforming how we learn and overcoming the limitations of traditional methods. With virtual training, employees can access flexible, immersive, and interactive learning experiences anytime, anywhere.
5. Remote & Predictive Maintenance with Digital Twin Technology
Digital twins can predict when components of the line are close to failure, alerting operators or even triggering automatic re-orders for spare parts and maintenance procedures. Remote functionality also contributes to machine uptime. Using sensors on the machine, experts can remotely access and diagnose failures, then resolve them through remote-controlled software or by guiding an on-ground specialist through corrective tasks. Remote monitoring can also predict maintenance needs or future fault scenarios, so plant managers can request spare parts ahead of time.
Enhancing Quality & Efficiency in Manufacturing with Digital Twins
Digital twins are revolutionizing the manufacturing industry by enhancing product design, process optimization, quality management, virtual reality training, and predictive maintenance. As more companies embrace digital twin applications, the benefits become increasingly evident.
According to a study by Research and Markets, 36% of executives across various industries understand the advantages of digital twin technology, and about half of them plan to implement it in their operations by 2028. This growing adoption underscores the transformative potential of digital twins in driving innovation, efficiency, and sustainability in manufacturing, especially as manufacturers scale up to meet increased demand. The half who level up their digital twin technologies will be positioned to outperform the rest.
Get in touch with us today to learn how digital twins could transform your production workflows at scale.
Every project is unique. Allow us to listen to your challenges and share how automation can launch your project on time.
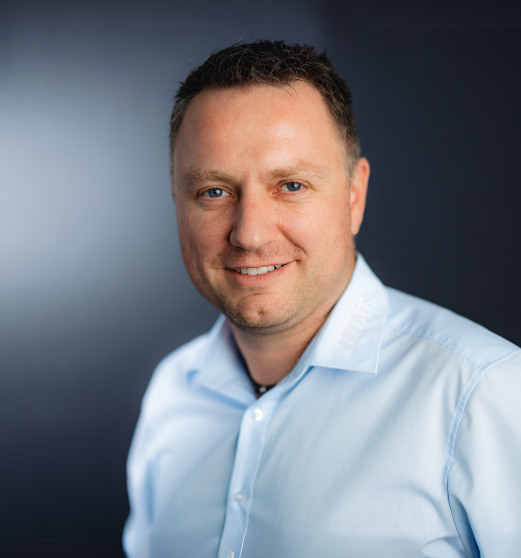
Roland Echter
General Manager - Digital
ATS Industrial Automation
Roland has helped companies across numerous industries to automate and optimize production with digital solutions. Roland works with customers to configure services, systems, using digital tool strategies to build and scale production and drive operational efficiency.