Automation roadmaps and smart factory integrations are pivotal in modern manufacturing, guiding the strategic implementation of advanced technologies to enhance operational efficiency and productivity. Roadmaps outline the vision, goals, and steps necessary for manufacturers to use automation solutions that align with business objectives. Smart factory integrations seamlessly incorporate Internet of Things (IoT) devices, digital twins, artificial intelligence (AI)-driven analytics, virtual reality (VR) training, and automated machinery into existing processes, creating a more connected and intelligent production environment.
Digital transformation also plays a crucial role in this context, enabling manufacturers to stay competitive by leveraging real-time, data-driven insights. By embracing digital transformation, manufacturers can optimize performance, reduce downtime, and continuously improve operations while responding to market demands.
Understanding Automation Roadmaps
An automation roadmap serves as a strategic guide for manufacturers to integrate automation technologies into facility operations, ensuring alignment with overall business strategies. The roadmap aims to provide a clear, structured plan that helps manufacturing organizations navigate the complexities of automation implementation, from initial planning to deployment.
Key components of an effective roadmap include a thorough assessment of current processes, identifying opportunities to add automation, and a detailed implementation plan. It must also encompass timelines, resource allocation, and performance metrics to track progress and measure long-term success. Additionally, stakeholder engagement and change management strategies are crucial to ensure smooth adoption and minimize challenges along the way.
A well-defined automation roadmap offers numerous benefits. It improves efficiency by streamlining processes and reducing manual intervention, leading to increased productivity, elevated product quality, reduced operational costs, and shorter time to market. Furthermore, a clear roadmap helps mitigate risks in automation projects by providing a structured approach that ensures all critical aspects are considered and addressed. Ultimately, roadmaps enable manufacturers to stay ahead of the competition by leveraging the full potential of automation technologies.
The First Step to Digital Automation
The initial steps of digital automation involve conducting a comprehensive evaluation of current processes and identifying areas or workflows where automation can bring the most value. This foundational analysis sets the stage for a focused approach to digital transformation, ensuring all efforts align with the manufacturer’s business goals and resources are allocated effectively. A digital production assessment also provides a clear picture of specific operational workflows—including logistics, manufacturing processes, controls strategies, and overall production performance.
Digital twins play a pivotal role in automation by creating virtual replicas of physical assets, processes, or systems. With real-time monitoring, simulation, and analysis, teams can optimize performance, predict maintenance needs, and make faster, data-informed decisions. Digital twins let manufacturers gain deeper insights into their operations, reduce downtime, and enhance overall efficiency. It’s essential to integrate this technology into an automation roadmap to achieve a seamless and effective digital transformation.
Smart Factory Integrations
Smart factory solutions involve smoothly incorporating advanced technologies and systems into current manufacturing workflows to create a more connected, efficient, and intelligent production process. This integration typically includes IoT devices, AI-driven analytics, and automated machinery, all of which work together to enhance operational visibility and control. By connecting machines, processes, and data, smart factory integrations lead to a more agile and responsive manufacturing setup.
The benefits of smart factory integration are substantial, including improving efficiency through optimized production workflows and reducing downtime through predictive maintenance. Enhanced data analytics provide valuable insights into production performance, so teams can better allocate resources and improve processes. Additionally, smart factory solutions minimize human error and ensure precise control over manufacturing parameters, leading to more consistent, high-quality products.
Risk Mitigation in Automation
It’s critical to identify and mitigate risks during the integration process. This helps drive the success and sustainability of automation in any manufacturing facility. Risks can arise from various sources, including technical challenges, operational disruptions, and stakeholders’ resistance to change. An automation expert can help manufacturers proactively identify these risks in an automation roadmap and develop strategies to address them before they escalate into significant issues. This approach safeguards the project and enhances its overall effectiveness.
Continuous improvement and risk management are integral to the automation journey. A robust risk management framework involves regularly monitoring, assessing, and updating mitigation strategies. This includes conducting periodic reviews of automation systems, analyzing performance data, and incorporating stakeholder feedback. Fostering a culture that is committed to continuous improvement encourages teams to identify potential risks early and develop innovative solutions to mitigate them.
Several manufacturers have successfully managed risks in their automation projects through an automation roadmap and strategic implementation. One manufacturer faced challenges while adding new automation technologies into current production lines. By conducting thorough risk assessments and involving cross-functional teams in the planning process, they were able to identify potential bottlenecks and develop contingency plans, resulting in a smooth transition and minimal disruptions to operations.
Another manufacturer implemented predictive maintenance systems to reduce downtime and improve equipment reliability. By leveraging real-time data and advanced analytics, they could anticipate and address maintenance issues before any costly breakdowns actually occurred, ultimately enhancing the facility’s operational efficiency and productivity.
For a more in-depth discussion about automation roadmaps and smart factory integrations, listen to the full episode on the Enabling Automation podcast.
Every project is unique. Allow us to listen to your challenges and share how automation can launch your project on time.
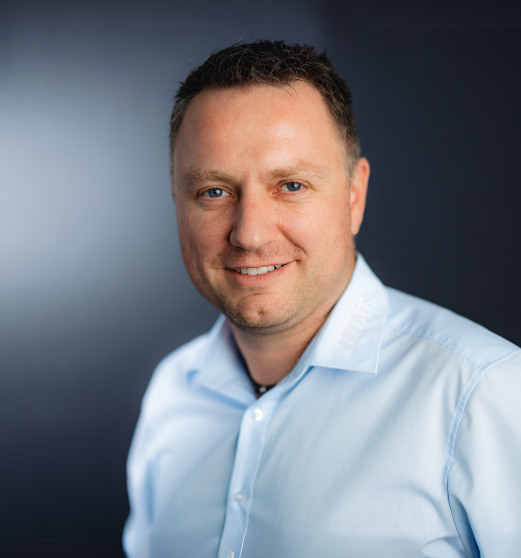
Roland Echter
General Manager - Digital
ATS Industrial Automation
Roland has helped companies across numerous industries to automate and optimize production with digital solutions. Roland works with customers to configure services, systems, using digital tool strategies to build and scale production and drive operational efficiency.