Since October of 2023, the United States Grid Deployment Office (GDO) has announced up to $7.6 billion in funding for Grid Resilience and Innovation projects across the United States. Grid battery energy storage systems (BESS) play an integral role in improving grid resilience projects. As grid BESS’ continue to grow in importance for organizations, funding and grant programs aimed at innovating and strengthening the electricity grid are becoming more prevalent. However, navigating the complex world of funding applications can be daunting and time-consuming.
This is where a grid battery manufacturing partner can make a big difference. From comprehensive testing and validation, and strategic planning and future-proofing, a trusted manufacturing partner can be invaluable to proving BESS manufacturing technology and creating a stronger grant application. Keep reading to learn how an experienced manufacturing partner can help you secure funding to take your grid battery business to the next level.
Preparing Successful Grant Applications
Setting up a winning grant application involves understanding the various types of funding sources available to grid battery manufacturers. These can include grants from federal or state governments, venture capital and private investment funds, global funding organizations, and private foundations or non-governmental organizations (NGOs) focused on clean energy. Each type of grant has specific criteria, requirements, and deadlines set out by the funder, making it essential to stay up-to-date with each. Regular monitoring of grant details ensures grid battery manufacturers submit applications on time and meet the funder’s evaluation criteria.
A manufacturing partner can be invaluable as you develop compelling grant proposals. While some partners have extensive experience in the grant application process and understand what funders look for, the most valuable part of engaging an experienced partner is the pre-automation process, which includes early stage risk mitigation through comprehensive testing and validation. By conducting proof of principle (POP) studies and producing specialized reports, grid battery manufacturers can better showcase their grid battery technology, further strengthening their grant applications.
An experienced partner can also offer advanced manufacturing and test technologies, and provide access to facilities that grid battery manufacturers may not otherwise have. The ATS Industrial Automation Proof of Principle Lab and Laser Labs, for example, enable companies to produce samples and gain real-time feedback from subject matter experts. This collaboration demonstrates the viability of the innovation, making it more attractive to funders, and strengthens the grant application.
Comprehensive Testing and Validation
End-to-end product and process testing and validation play a crucial role in improving energy grant applications by demonstrating that the product and manufacturing process are feasible. This involves rigorous testing and validation to ensure the end product meets industry standards and specifications. By incorporating design for manufacture and assembly (DFMA) principles and POP studies a manufacturing partner can identify potential issues early in the product development phase.
Utilizing DFMA principles is vital because they help optimize both the manufacturing and assembly processes from the outset. DFMA combines Design for Manufacture (DFM), which focuses on simplifying manufacturing and reducing manufacturing costs, and Design for Assembly (DFA), which aims to simplify the assembly process and reduce the cost of assembly. By integrating these principles early on, companies can identify potential design improvements that will reduce variation, and simplify the overall production of grid batteries. This proactive approach not only strengthens grant proposals by demonstrating a commitment to efficient and cost-effective manufacturing, but also improves product viability for high-volume production, making it more attractive to funders.
POP studies are essential for evaluating product designs and establishing process capabilities during the early stages of product development. These studies test and validate whether proposed automation can execute required product assembly and test processes, optimizing product performance for scalable production. By addressing automation uncertainties early, POP studies mitigate risks, save time during equipment integration, and establish the foundation for high-volume production. Conducting POP studies with a manufacturing partner provides valuable insights, solutions to challenges, and specialized reports that help secure funding.
Improve Funding Success with a Trusted Manufacturing Partner
With the rising demand for BESS, grid battery manufacturing companies must consider grant opportunities in their overall funding strategy to drive growth. Engaging an experienced manufacturing partner can be a game-changer in navigating the complex process.
A manufacturing partner’s industry expertise, technologies, knowledge, and credibility can empower businesses to design with manufacturing in mind. Additionally, they offer rigorous testing to determine a product’s viability – or any revisions that might be needed – before scaling production to higher volumes. By leveraging proven expertise, tools, and technologies, energy companies not only improve their chances of securing funding, but also ensure their product is built for long-term market success.
Ready to learn more about the BESS manufacturing lifecycle? Complete the form to download our eBook today.
Download our Free eBook to learn more about navigating challenges in the battery manufacturing lifecycle.
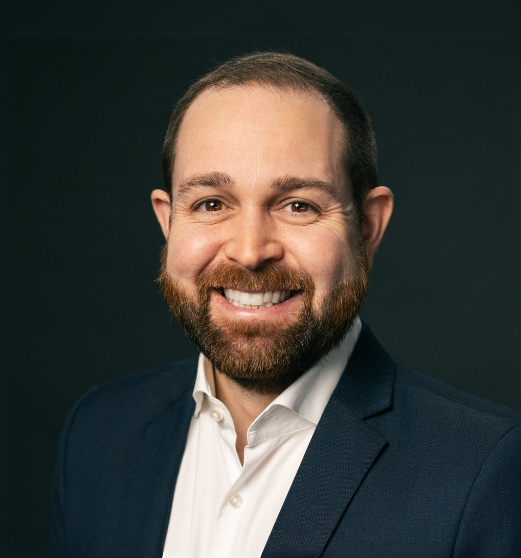
Ryan Tavares
Director, Pre-Automation Services
ATS Industrial Automation
For over 20 years, Ryan has helped top-tier manufacturers and industry innovators transform their operations through automation and process optimization. Ryan empowers manufacturing businesses to enhance efficiency, improve product quality, and scale production to drive sustainable growth and maximize returns.