In 2015, approximately 64% of global manufacturing-related activities were automatable with existing technology. Today, across industries, about half of the tasks that workers perform can be automated.
Automation engineering, which involves using control systems to operate equipment with minimal human intervention, has dramatically transformed industries over the past century. From the early days of manual drafting and mechanical controls to today’s sophisticated, artificial intelligence (AI) driven systems, the evolution of automation engineering is a testament to human ingenuity and technological progress.
Understanding this journey of automation and digitalization technology is crucial to appreciating current advanced capabilities, such as real-time data integration and predictive maintenance. These improvements continue to push the boundaries of efficiency and innovation in various sectors.
The Early Days of Automation Engineering
Manual drafting was the cornerstone of design work in the 17th and 18th centuries, with Oliver Evans’ flour mill being the first fully automated production line. In these early days of automation design, engineers relied on tools like pencils, vellum paper, T-squares, and compasses to create detailed technical drawings by hand. This labor-intensive process required significant skill and precision, as any changes meant redrawing entire sections of the design.
The introduction of Computer-Aided Design (CAD) in the 1960s revolutionized this field by automating many of these tasks. CAD software allowed engineers to create, modify, and optimize designs digitally, significantly reducing the time and effort required. It also enabled the creation of 3D models, providing a more comprehensive view of the design and facilitating better analysis, quicker design iterations, and team collaboration. This shift also enhanced the accuracy and complexity of engineering designs.
Digitalization Technology: The Rise of Digital Twins
A digital twin is a virtual representation of a physical object or system that accurately reflects its material counterpart through concurrent data and simulations. Digital twins incorporate these dynamic capabilities with CAD models, enabling manufacturers to level up design work and optimize production. This technology also allows for predictive maintenance and quality management, ultimately improving productivity.
The concept of digital twins in manufacturing began to take shape in the early 2000s. Experts often credit Dr. Michael Grieves with introducing the idea in 2002 and applying it to product lifecycle management. Initially, digital twins would create virtual models of products to replicate their behavior and performance throughout the lifecycle. Over time, advancements in technology have expanded their capabilities. Now, manufacturers can apply digital twin technologies to entire production systems and workflows, enabling real-time data integration and more sophisticated simulations that empower manufacturing leaders to make data-driven decisions quickly.
The Emergence of System Twins
System twins are advanced digital representations integrating multiple digital twins, which emerged as a concept in the 2010s. Today, manufacturers are finding value in this newer technology, since it provides a comprehensive view of interconnected manufacturing systems. Unlike digital twins, which virtually replicate individual physical entities, system twins encompass all of the machines, devices, and processes within a manufacturing line or other complex network. This integration allows for a more dynamic simulation of how multiple components interact with one another, offering a more detailed perspective on potential production issues.
Integrating multiple digital twins to form a system twin involves combining data from various sources to create a unified model. This reflects the entire network’s real-time status and behavior. The process is complex, as it requires synchronizing data from different machines, sensors, and control systems to ensure accurate and consistent representation. However, the result provides invaluable insights into the overall efficiency and functionality.
System twins also enhance operational efficiency by providing a broad understanding of the entire system’s performance , allowing for predictive maintenance in manufacturing before failures occur. This can extend the lifespan of equipment, minimize disruptions, and increase cost savings.
Challenges & Future Directions
Several emerging trends could shape the future of automation engineering, with the integration of AI and machine learning (ML) at the forefront. These technologies may enable even more sophisticated, autonomous systems.
AI/ML can analyze vast amounts of real-time data. This means systems can learn from past performance, adapt to new conditions, and continuously improve efficiency and effectiveness. Integrating AI with digital twins and system twins will further enhance these technologies’ capabilities, providing even more accurate simulations and insights.
As automation engineering continues to evolve, we can also expect to see increased collaboration between humans and machines. AI-driven systems will take on more complex tasks as well as ongoing menial tasks, freeing up staff to focus on higher-level strategic activities. This shift will improve productivity, enable innovation, and open doors to new opportunities across industries.
Step into the Future of Automation Engineering
Over the decades, transformative digitalization technologies such as CAD drawings, digital twins, and system twins have shaped automation engineering. As we enter the exciting future of automation engineering, manufacturing leaders must stay updated on the latest advancements in the field. The integration of AI and machine learning with these technologies promises even greater capabilities, driving innovation and efficiency to new heights. By embracing these advancements early, industry leaders can continue to push the boundaries of what’s possible, ensuring they remain competitive in an ever-evolving landscape.
Every project is unique. Allow us to listen to your challenges and share how automation can launch your project on time.
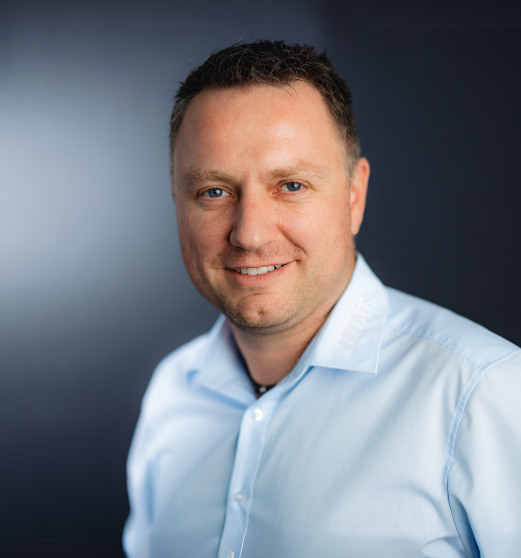
Roland Echter
General Manager - Digital
ATS Industrial Automation
Roland has helped companies across numerous industries to automate and optimize production with digital solutions. Roland works with customers to configure services, systems, using digital tool strategies to build and scale production and drive operational efficiency.