Integrating automated guided vehicles (AGVs) into a manufacturing plant can be a transformative step toward enhancing efficiency and productivity. AGVs, which seamlessly transport materials and products within a facility, have been shown to increase production by up to 33% in some large car manufacturing companies. This reduces the need for manual labor and minimizes errors during material handling. As industries continue to evolve toward smarter and more flexible manufacturing systems, the adoption of AGVs can aid original equipment manufacturers (OEMs) as they navigate ways to stay competitive in the global market.
What’s the Difference Between AGV, AMR, and AGC?
Understanding the difference between types of AGVs, autonomous mobile robots (AMRs) and automated guided carts (AGCs), is crucial to optimize material handling in modern manufacturing. Each system offers unique features and benefits that cater to specific applications and operational needs.
Automated Guided Vehicle
AGVs are widely used in industrial manufacturing and can be guided by lasers or tape and utilized throughout the assembly line, warehouses, or other production spaces.
AGVs have a wide range of applications in manufacturing, significantly enhancing operational efficiencies. They are commonly used to transport materials and products throughout the production line, from raw to finished goods.
AGV systems can handle repetitive tasks such as moving components between workstations, delivering parts to assembly lines, and transferring finished products to storage or shipping areas. They also support warehouse management, organizing inventory, selecting and placing items, and managing stock levels. By automating these processes, AGVs reduce the need for manual labor and ensure a smooth and continuous flow of materials within the manufacturing facility.
Automated Guided Cart
An AGC is a type of AGV designed to transport very heavy products within a manufacturing facility. AGCs typically use tape guidance to navigate through the production line. They are relatively simple, low-cost solutions, making them ideal for applications such as moving cars along an assembly line.
Autonomous Mobile Robot
An AMR is a more advanced type of AGV that moves smaller products within warehouses. AMRs usually carry payloads of less than 500 pounds and are equipped with smart navigation systems, including cameras and sometimes AI-driven software. They are commonly used for delivering parts to the production line and are particularly effective in environments that manufacture consumer packaged goods (CPG).
Benefits of Using AGVs
AGVs offer numerous benefits in today’s manufacturing environments:
- They significantly enhance movement efficiency, transporting materials efficiently and accurately throughout the facility. This leads to optimized workflows and reduced downtime.
- AGVs handle routine tasks that would normally place physical strain on workers. This improves employee well-being and allows staff to focus their time on more complex or value-added tasks.
- AGVs enhance precision and safety in operations compared to manually transporting parts or using forklifts.
How to Integrate AGVs in Manufacturing
Adding AGVs to a production plant is a complex process. The timeline for implementation can be daunting, especially since AGVs can’t be tested in the manufacturing environment until after the production line is installed. Teams must carefully plan these elements to avoid costly schedule delays. Key considerations include:
- Assessment and Layout Planning: The first step is to review the current manufacturing setup and identify specific tasks the AGVs can perform. AGVs’ advanced navigation systems can lead to challenges in complex environments. They also require sufficient space to move throughout manufacturing areas. Careful planning of the facility’s spaces can ensure smooth integration.
- Design and Customization: Once the assessment is complete, the next step is to design and customize the AGVs to meet the manufacturing plant’s specific needs. This includes considering the turning radius and interface size, plus ensuring handshake sensors are location specific.
- Software Integration: AGVs need robust software systems to manage and control their operations. That means developing or adapting software to ensure seamless communication between the AGVs and existing manufacturing systems.
- Installation and Testing: Once the AGVs are installed in the manufacturing plant after the design and customization, they require further testing to ensure they’re operating correctly and efficiently during production.
- Training and Regular Maintenance: Finally, it’s crucial to train staff in operating and maintaining the AGVs. Operators must also routinely charge and check AGVs to keep these systems functioning correctly. Regular maintenance can prevent costly disruptions in the production line and help the AGV perform as long as possible.
Integrating AGVs into Manufacturing Plants
AGVs are transforming today’s manufacturing workflows—improving precision in material transport and handling repetitive tasks so employees can focus on higher-value work. Despite the challenges of integrating AGVs, such as having adequate space, prioritizing ongoing maintenance, and software integration, their potential to optimize workflows and reduce costs often makes them a worthwhile investment.
A mature automation partner can help OEMs navigate this intricate process, delivering equipment and software that seamlessly integrates with AGV systems. Get in touch with one of our experts today and learn how AGVs can help you stay competitive and create a safer, more productive workplace.
Every project is unique. Allow us to listen to your challenges and share how automation can launch your project on time.
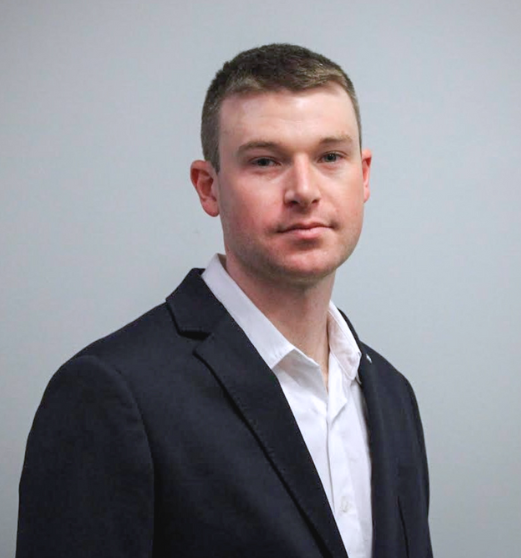
Kevin Peake
Key Account Manager
ATS Industrial Automation
Kevin has helped companies across numerous industries automate and optimize production. Kevin has a Bachelor of Science in Aerospace Engineering and Mechanical Engineering, he loves robots and has built them in his basement for fun. He enjoys helping customers configure systems to build and scale production and drive operational efficiency.