In the rapidly evolving and complex field of battery production, OEMs must implement an effective automation sourcing strategy. With battery manufacturing scrap rates ranging between 5-10% across the industry, selecting the right automation technologies and supplier can help manufacturing leaders optimize production and ensure those processes are efficient, scalable, and cost-effective.
A well-planned automation sourcing strategy directly impacts the success of battery product launches. It has the ability to reduce lead times and maintain consistency across manufacturing sites. It also helps mitigate risks, including supply chain disruptions and technical incompatibilities, ultimately supporting smoother operations and faster time-to-market.
A critical question that arises in this context is whether to localize or globalize battery production technology. This decision hinges on various factors, including:
- Project management complexities
- Government policies
- Technical standards
- Logistics
Localizing production offers advantages such as consistent communication and alignment with local regulations. Meanwhile, globalizing can provide uniformity and scalability across multiple facilities. Each approach has its own set of challenges and benefits, making it essential for battery manufacturers to carefully evaluate their specific needs and goals before determining the most suitable option.
Understanding Automation Sourcing Strategies
Building an automation sourcing strategy involves carefully planning and selecting automation technologies and suppliers that can help manufacturing companies optimize production processes. Automation solutions encompass various elements, including project management workflows, technical standards, regulations, and logistics. By keeping each of these factors top of mind, companies can determine the most effective approach, whether through turnkey solutions or discrete work packages. The goal is to ensure the chosen systems align with production requirements and can be seamlessly integrated into manufacturing operations.
Properly sourced automation systems can reduce lead times, enhance production quality, and ensure consistency across manufacturing sites. These systems also mitigate risks associated with supply chain disruptions and technical incompatibilities. By strategically planning the sourcing of automation technologies, companies can enhance production and expedite time-to-market for their battery products.
Key Factors Driving Automation Sourcing Strategies
Several key factors influence automation sourcing strategies. This is especially true for large-scale battery automation projects with global operations. Effective communication is paramount, as language barriers can significantly impact project timelines and outcomes. OEMs must ensure the customer and automation supply team align on the language used in project communications. English is often the common language for global programs.
The choice between centralized program management and localized project management also plays a critical role in sourcing equipment. A centralized or global approach can provide uniformity and adherence to corporate standards, but it may face challenges in addressing local infrastructure needs. Conversely, local project management offers the advantage of proximity and a better understanding of regional specifics, though it requires robust coordination with the main team. Leaders must also consider time zone differences and non-productive time. Local automation can alleviate these issues by aligning working hours, which reduces downtime.
Resource availability is another vital consideration. Skilled project management talent is scarce and valuable. In addition to selecting the right equipment, properly staffing both global and local project management roles ultimately supports the automated production of battery technologies, no matter where they happen.
Local vs. Global Management
Local and global project management approaches differ significantly in scope. Local project management is typically more straightforward. By leveraging local resources, OEMs can make decisions faster and better align with local regulations and market conditions. However, this tactic may lack the broader perspective, consistency, and global mindset that centralized management offers.
Global program management offers uniformity and adherence to corporate standards across multiple locations. This approach ensures all projects align with the organization’s strategic goals. However, it comes with its own set of challenges, such as potential gaps in addressing local infrastructure needs and the difficulty of managing diverse teams in different locations. Manufacturing leaders cannot underestimate the complexities and increased effort required for global programs. These projects demand robust coordination, extensive communication, and a significant investment in task management resources. By ATS estimates, managing a global program, often requires at least 50% more effort than a locally managed project would, reflecting the increased complexity of today’s manufacturing landscape and the need for meticulous planning and execution to ensure success across multiple locations.
Line Integration Approaches
Line integration can happen through an integrator or is managed by the OEM. Engaging an integrator means the entire automation and test equipment line comes from a single provider. This approach often results in a more controlled and condensed schedule to the start of production (SOP), as the vendor manages the integration and debugging of all components.
Meanwhile, an OEM owned integration approach involves procuring various technologies from different suppliers. Then, companies must handle the integration internally or select a separate automation or controls provider. This method offers flexibility but may introduce complexities in ensuring uniform technical configurations and managing logistics between teams and external partners.
Key considerations for line integration include staffing, process complexity, schedule, and costs. Staffing is critical, as skilled resources are scarce and essential for both initial implementation and ongoing support. Team leaders must also manage each process carefully to ensure all components work together, which can be challenging when dealing with multiple suppliers.
The timeline is another crucial factor. A turnkey supplier can often shorten the road to SOP compared to the coordination it takes when managing more than one vendor. Finally, cost considerations include initial procurement and long-term expenses associated with maintaining the integrated line. It’s vital to effectively manage these factors for the successful implementation of major battery production projects.
Multi-Line and Multi-Facility Considerations
It’s essential to implement global common build standards for battery projects with multiple lines and facilities. These standards ensure consistency and quality across sites, reducing technical risks and facilitating easier support and redeployment of equipment. Staggered installations and shipping logistics helps manage the complexities of rolling out equipment in various locations while maintaining a uniform build standard. An automation partner with experience executing multi-facility installations within compressed time frames can help battery OEMs efficiently meet global production demands.
Best practices for installation and operations process replication include using digital tools to reduce lead times and improve process development. Digital twin technology, for instance, allows for rapid deployment of design changes across locations, providing a virtual model to test and refine workflows before physical implementation. Emphasizing the deployment of successful repeat line operations ensures each facility operates at the same level. Utilizing a consistent installation team across multiple sites can further streamline the process, ensuring operators can apply best practices consistently and address any issues uniformly. This approach enhances continuous improvement across the production network.
ATS Industrial Automation: A Global Leader
ATS Industrial Automation stands as a global leader in the automation industry, renowned for its extensive experience and innovative solutions. With a presence in over 65 facilities and 85 offices worldwide, the company employs more than 7,500 professionals dedicated to advancing historic green tech. ATS boasts over 45 years of expertise in automation technologies, serving diverse markets including eMobility, energy and consumer goods.
A well-planned automation sourcing strategy can help OEMs make certain their production systems are efficient, scalable, and capable of meeting global demand. The decision to localize or globalize battery production technology must align with the specific goals of the battery project. Localizing can offer advantages in communication and optimize production time, while globalizing provides uniformity and scalability. Ultimately, whatever approach production leaders take should support more efficient operations and sustained competitive advantage as the battery market continues to grow.
Download our Free eBook to learn more about navigating challenges in the battery manufacturing lifecycle.
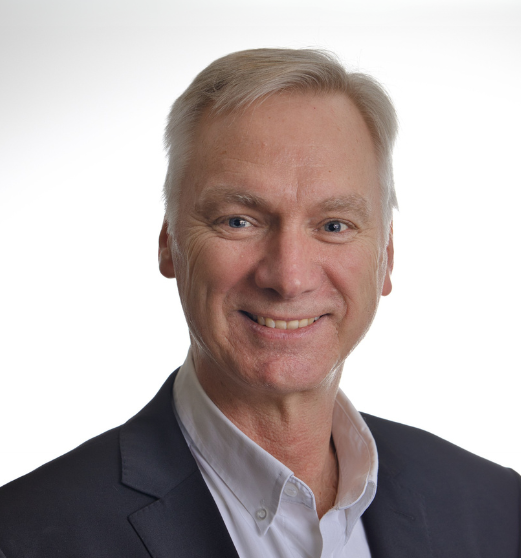
Rob Faulhammer
Vice President of Sales, Specialty Automation
ATS Industrial Automation
Rob has helped companies of all kinds to automate and scale production for over 30 years. Rob works with customers throughout their lifecycle to configure services, systems and digital tools strategies to enable product manufacturing at scale.