Segmentation of a nuclear reactor during the decommissioning processes is highly complex and presents several significant challenges like radiation hazards, contamination control, worker safety, structural stability, tight spaces, degraded conditions, volume reduction, and tool reliability.
Segmentation involves the cutting and dismantling of two main reactor components: the reactor vessel, and the reactor vessel internals. Traditionally, this has been done using remotely operated equipment with primarily manual controls, and very little, if any, automation. But what if we could actually make this process safer and more efficient with automation?
For many industries such as life sciences, industrial assembly and consumer product manufacturing, automation is at the core of their manufacturing and is most often associated with improved performance, safety, and cost. But for nuclear, and specifically Pressurized Water Reactor (PWR) style segmentation, operators are segmenting components that are few in number, but with very large and heavy sections, rather than a large number of components that are relatively small and present themselves in a repetitive matrix as in the industries mentioned above.
Common Challenges During Segmentation
Operators usually prefer manual controls because they want the ability to directly control speeds, travel, and pressures directly using manual controls and jogging.
Automation is often negatively associated with unproven customization, lack of robustness, “flakey” operation, and high levels of complexity that complicate troubleshooting and in-field support.
But does it need to be this way?
Reactor internal and pressure vessel segmentation can be augmented with appropriate levels of automation and doesn’t need to be at the expense of simplicity, robustness, and operator friendly operation.
Why Add Automation to Decommissioning?
While automation might seem daunting, it’s been a game-changer in many other industries and shouldn’t be overlooked in nuclear decommissioning. Automation usually requires that the process and part types being handled are well defined. This is traditionally provided through some type of user specification, which defines in detail the process, components, and required outcomes. Speeds, cycle times, weights, dimensions, accelerations, materials, surface finish, environment, tolerances, material strengths and hardness, and allowable contact materials, are specified in great detail and acceptance of the equipment is tied directly to these requirements.
The automation required for these applications is typically focused on throughput, cycle time, and quality. High-speed handling and path planning are usually entirely within the control and discretion of the automation provider. The automation is usually focused on eliminating repetitive operator tasks and improving output. Components are relatively light-weight, and anything over a tonne would be considered heavy. The system, processes, and equipment provided typically include high-speed measurement and vision systems, and qualified processes with detailed parameters. Most of the time, these are factory automation applications where the environment is well-controlled and relatively clean.
In contrast, for segmentation environments, the detailed processes are often not well defined. A cut plan will be developed but is focused on waste classification and it is not required to provide the level of detail typically seen in other industrial automation markets. The actual segmentation can be heavily driven by actual field conditions and as-found conditions.
The part properties that would normally be critical to an automation designer or engineer in a routine industrial automation project are not a consideration in segmentation. Cut finish is usually irrelevant and final size is very approximate and variable. But this doesn’t mean automation should be discounted.
Different levels and types of automation have been shown to be appropriate for segmentation. There are many types and configurations of tools where these approaches can be applied. While the examples of automation may seem trivial to those immersed in standard industrial settings, they represent a level of automation that is appropriate and adds improved safety, efficiency, and cost, for the segmentation environment. The automation described below provides operational flexibility, to work in fully manual jog mode or select some simple automated moves when needed.
The Approach to Adding Appropriate Levels of Automation for Nuclear Segmentation
Different levels and types of automation have been shown to be appropriate for segmentation. Segmentation systems such as the MultiFlex™ nuclear segmentation system, which I will talk about more shortly, can be provided that significantly reduce the amount and size of segmentation equipment in order to minimize set-up effort and Automation, when applied correctly, can maximize operational flexibility, while maintaining the robustness and proven cutting methods. This type of automation augments the baseline manual operation, while providing the operator with options for combined moves to minimize operator-dependent co-ordination, improve cutting efficiency, reduce operator strain, and reduce the chance of errors.
This approach is heavily based on providing the operator options for ease of control, but not replacing the ability to operate in a completely manual mode. This allows the operator to use the best mode of operation depending on the situation at hand and the actual field conditions.
MultiFlex™ uses electric servo axes for precise, programmable movements. Operators can still control everything manually if they want, but they also have the option to use automated moves for more efficiency.
How Simple Automation Improves Efficiency During Segmentation
Simple Distance Move
The MultiFlex™ Nuclear Segmentation Systems allows vertical cuts to be made moving from one position to another, without operator intervention. For automation designers, this may barely meet the bar for automation but has been used in segmentation and proven to be an appropriate level of simple and effective automation.
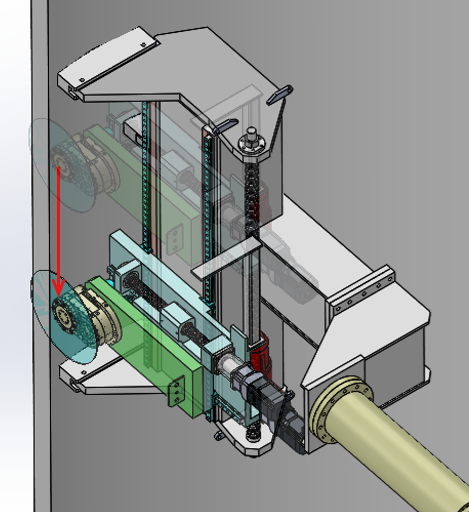
Simple Coordinated Move
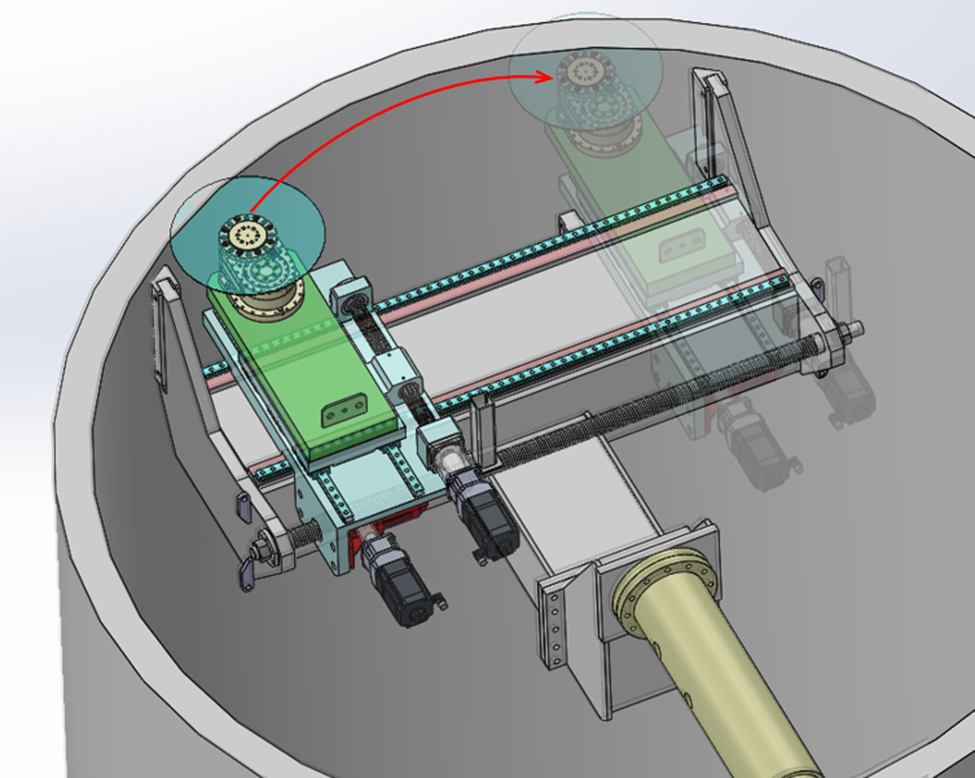
The image to the left illustrates a coordinated move in the ATS MultiFlex™ Nuclear Segmentation System. This automated move allows horizontal cuts to be made along a curved path to follow the radius of the reactor vessel and prevents the need for the operator to jog two axes at the same time as would be standard for a manual operation.
Point-to-Point Moves
This automated move allows horizontal cuts to be made along a curved path from point B to point C in the same way as the coordinated move, but adds an initial plunge from point A to point B.
This allows the operator to make cuts on as-found complex geometries where the operator has control over the selection of points based on field conditions, and then use the automation to coordinate multiple axes in a way that would be nearly impossible for an operator to control.
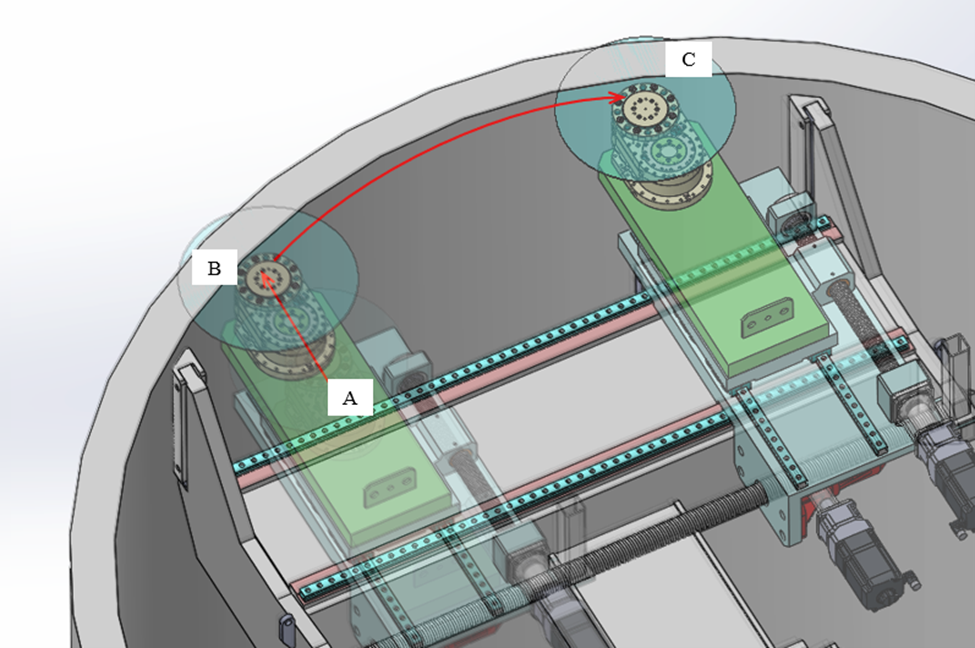
By integrating appropriate levels of automation, we can reduce setup time, improve operational flexibility, and maintain robust cutting methods. This hybrid approach allows operators to choose the best mode of operation based on the situation, ensuring both safety and efficiency, proving that automation doesn’t have to be overly complicated.
It is essential that the automation applied considers the difference between a standard industrial automation environment and nuclear segmentation to avoid over-automating and over-engineering solutions. With the right balance, it can significantly improve the segmentation process in nuclear decommissioning.
Talk to a member of our Nuclear team to learn more about how our MultiFlex™ Nuclear Segmentation System can help solve your decommissioning challenges.