Die Qualität der Batterien als einer der wichtigsten Faktoren bei der Batterieproduktion ist nicht nur Ergebnis der Montage- und Testprozesse der physischen Produktionslinie, sondern auch der miteinander verbundenen Datenverwaltungssysteme, die das Zusammenwirken all dieser Prozesse dokumentieren. Mit der verpflichtenden Einführung des Batteriepasses in Europa bis Februar 2027 wird es für Batteriehersteller immer wichtiger, umfassende Aufzeichnungen über die Herkunft der Rohstoffe, die Produktionsgeschichte und die Qualitätstests der Batterien zu führen.
Eine der Voraussetzungen für den Batteriepass ist die Einhaltung einer Richtlinie zur Sorgfaltspflicht in der Lieferkette, in der Nachhaltigkeitspraktiken und betriebliche Transparenz festgelegt sind. Für Batteriehersteller bedeutet das, dass die Qualität der Batterien bereits mit der Herkunft der Rohstoffe beginnt, lange bevor die Produktion startet. Rohstofflieferanten müssen Transparenz darüber gewährleisten, wie sie die Materialien beschaffen, Daten verwalten, Systeme schützen und Kontrollen für jede Batterie durchführen. Dies erfordert umfangreiche Systeme, die all diese Informationen erfassen und den einzelnen Batterieeinheiten zuordnen können, vorzugsweise in Echtzeit und schließlich auch zugänglich für den Verbraucher, der das Fahrzeug kauft, in dem die Batterie eingebaut ist.
Ein solches System könnte ein Manufacturing Execution System (MES) sein, das den Herstellungsprozess von Waren nachverfolgt, dokumentiert und kontrolliert – vom Eingang der Rohstoffe in der Fabrik bis zum fertigen Produkt. Das MES bildet die Grundlage für den Herstellungsprozess. Es verbindet die Produktion mit den Managementsystemen des Unternehmens, indem es Einblicke in Produktionsvolumen, Ausschussrate, OEE usw. gewährt. Ein MES ist jedoch nur so gut wie die Daten, mit denen es gespeist wird, darunter Ergebnisse der Batteriemontagetests an der Produktionslinie.
Aufbauend auf einem Fundament von Qualitätsmontageprozessen
Bei Qualität fällt einem zuerst der Montageprozess ein – und Qualität beginnt bei der Batteriezelle. Am Anfang des Montageprozesses müssen automatisierte Hochgeschwindigkeitstests und die Sortierung von Zellen mit Barcode, einschließlich der Erkennung und Aussortierung fehlerhafter Zellen, schnell und präzise erfolgen. Diese Tests konzentrieren sich auf die Intaktheit des Inneren der Zelle, d. h. Kapazität, Ladung, Spannung und Innenwiderstand, z. B. AC/DC-Innenwiderstand (IR), Selbstentladung der Zelle, HiPot-DW-Isolationswiderstand und mehr.
Und jetzt vervielfachen Sie das um Tausende. Ein einziges EV-Batteriepaket kann 6.500 Zellen umfassen, wofür 13.000 einzelne spaltfreie Laserschweißnähte erforderlich sind. Zunächst erkennt das intelligente Laserbearbeitungs- und Schweißsystem die Teile und richtet sie in fachmännisch konstruierten Schweißzangen oder -köpfen aus. Dann überprüft es mit einer Kombination aus Robotik, Bildverarbeitungssensoren und Laserschweißen die Tiefe der einzelnen Schweißnähte in Echtzeit und meldet sofort, ob die Schweißnaht in Ordnung ist oder nicht.
Angesichts der unterschiedlichen Größen von Batteriemodulen und der Komplexität ihres Zusammenbaus erfordern Batteriemodule zahlreiche Tests, mit denen die einzelnen Verbindungspunkte zwischen den Zellen sowie ihre integrierte Leistung und Haltbarkeit bewertet werden. Mit weiteren Tests wird die physische Robustheit und Sicherheit des Moduls überprüft. Dazu gehören Temperatur-, Schweiß- und Stromschienenwiderstand, Dichtheitstests, mechanische Vibrationen und Tests des Batteriemanagementsystems (BMS) (Letzteres wird auch bei Batteriepacks getestet).
Ein BMS ist eine obligatorische Komponente einer fertigen EV-Batterie. Es überwacht und steuert die Temperatur, den Strom und die Spannung der Batterie während des Ladens und Entladens. Es bestimmt den Ladezustand (State of Charge, SoC) und den Funktionszustand (State of Health, SoH) der Batterie und regelt die internen Betriebsbedingungen, um Leistungsfähigkeit und Sicherheit zu erhalten und die Lebensdauer der Batterie zu verlängern. SoC- und SoH-Schätzmethoden wie Leerlaufspannungstests (OVC) und die elektrochemische Impedanzspektroskopie (EIS) sind unerlässlich, um den Betrieb des BMS innerhalb des Batteriepacks zu bewerten, bevor es die Produktionslinie verlässt.
Regelung der Anforderungen und Protokolle von Batterietests
Die Kenntnis, welche Tests durchgeführt werden sollen, ist nur ein Teil der Qualitätsgleichung; die Kenntnis der komplexen Anforderungen und Protokolle für diese Tests ist ein anderer. Die Testergebnisse werden anhand von Parametern und Bestanden/Nichtbestanden-Schwellenwerten gemessen, die mit Software wie der ATS Test Executive Suite konfiguriert und gesteuert werden.
Diese werden vom Batteriehersteller definiert, um die spezifischen Mess- und Kontrollanforderungen für jede Komponente und jede Phase des Montageprozesses sowie für das fertige Batteriemodul oder -pack zu erfüllen. Rückverfolgbare Produkttestberichte, Prozessereignisprotokollierung, Versionskontrolle und andere Datenverwaltungsfunktionen bieten eine detaillierte Aufzeichnung der Testhistorie der Batterie.
Die Genauigkeit und Wiederholbarkeit der Testergebnisse hängt jedoch von der Kalibrierung der Testgeräte und der Prüfung und Validierung der Testprotokolle ab. Die ATS Test Executive Suite verfügt beispielsweise über integrierte Diagnose- und Analysewerkzeuge zur Automatisierung der Sensorkalibrierung und liefert Statistiken zum Prozessfähigkeitsindex (Cpk) sowie Studien zur Wiederholbarkeit und Reproduzierbarkeit von Messungen (gauge repeatability and reproducibility, GR&R) zur Ermittlung der Variabilität von Messsystemen.
Die Informationen aus der ATS Test Executive Suite können über eine gemeinsame Steuerungsarchitektur in ein MES integriert werden. Durch diese Datenintegration wird der Kreislauf der Batterieproduktion vom Rohmaterial bis zum fertigen (getesteten und validierten) Produkt geschlossen, wobei diese rückverfolgbare Historie nach Bedarf im MES, SCADA, QMS und anderen Fertigungssystemen gespeichert wird.
Jedes Batterieprojekt ist einzigartig. Wir möchten uns Ihre Herausforderungen anhören und Ihnen mitteilen, wie Sie Ihr Projekt durch Automatisierung rechtzeitig auf den Weg bringen können.
Datenbereitschaft für den Batteriepass herstellen
Bis Februar 2027 wird in Europa für alle EV- und Industriebatterien ein Batteriepass erforderlich sein. Dieser standardisierte und reglementierte digitale Datensatz muss Informationen über Haltbarkeit, Leistung, SoH, Herstellungsstandort(e), Sorgfaltspflicht in der Lieferkette und mehr enthalten. Die Daten, die während des Beschaffungsprozesses dokumentiert und während des gesamten Produktions- und Testlebenszyklus der Batterie erhoben wurden, werden einen Großteil des Batteriepasses ausmachen.
Insbesondere Haltbarkeit, Leistung und Funktionsfähigkeit der Batterie sind Schlüsselindikatoren für ihre Gesamtqualität, die direkt mit der Montage und den Tests sowie der Rückverfolgbarkeit und Verwaltung dieser Testergebnisse zusammenhängt. Dies unterstreicht die Bedeutung miteinander verbundener Montage-, Test- und Datenerfassungsprozesse und Arbeitsabläufe sowie robuster und flexibler Datenverwaltungssysteme, die alles zusammenführen.
Mit mehr als 45 Jahren Erfahrung in der Automatisierung und mit Fachwissen zu zahlreichen Testdienstleistungen und -lösungen kann Ihnen unser Team aus Montage- und Testexperten beim Aufbau eines umfassenden End-to-End-Produktionsprogramms für Batterien helfen. Lassen Sie uns wissen, wenn Sie über Ihre spezielle Situation sprechen möchten.
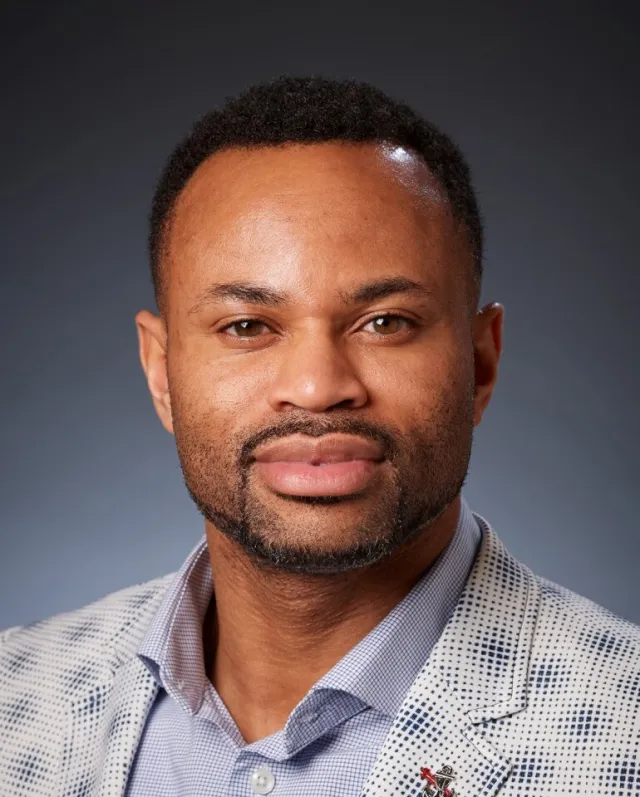
Peter Adeyemi
Kundenbetreuung Vertrieb
ATS Industrial Automation
Peter Adeyemi unterstützt Unternehmen in zahlreichen Branchen bei der Automatisierung und Optimierung von Test- und Validierungsprozessen. Er konfiguriert gemeinsam mit den Kunden Testsysteme für den Aufbau und die Skalierung der Produktion und die Steigerung der betrieblichen Effizienz.