12. December 2022
Im Jahr 2021 gab es 19 E-Fahrzeugmodelle. 2022 waren es bereits 33, Tendenz steigend. Die Branche entwickelt sich schnell weiter – mit neuen Geschäftsmodellen, neuen Designs und neuen Strategien zur Markteinführung von E-Fahrzeugen. In einer Branche, in der alles neu ist, brauchen Unternehmen einen Partner für die Produktion und nicht nur einen Automationslieferanten.
Ein Lieferant stellt her, was bestellt wird, aber ein Partner in der Produktion bringt die Fähigkeiten und die Erfahrung für Untersuchungen mit, berät hinsichtlich Best Practices und bietet die beste Lösung für Ihr Unternehmen. Produktionspartner haben nachweislich Erfahrung bei der Lösung komplexer Herausforderungen und wissen, was funktioniert, was nicht funktioniert und warum. Mit einem Produktionspartner können Sie die Produktion entsprechend der aktuellen und zukünftigen Nachfrage optimieren und skalieren, auch wenn sich Ihre Batteriedesigns weiterentwickeln.
Nachdem wir mehr als 90 Montage- und Teststraßen für E-Fahrzeug-Batterien geliefert haben, sind wir um einiges schlauer. In diesem Webinar besprechen wir, wie wichtig es ist, mit einem Produktionspartner und nicht nur mit einem Lieferanten zusammenzuarbeiten.
Behandelte Themen:
- Was ist eine Design Authority?
- Der Unterschied zwischen einem Lieferanten/Anbieter, einem Partner und einer Design Authority.
- Die Vorteile, die ein Produktionspartner für Projekte haben kann.
Schauen Sie sich jetzt das Webinar „Was wir aus 90 Batteriefertigungslinien gelernt haben“ an
HINWEIS: Das Video ist auf Englisch
Referent
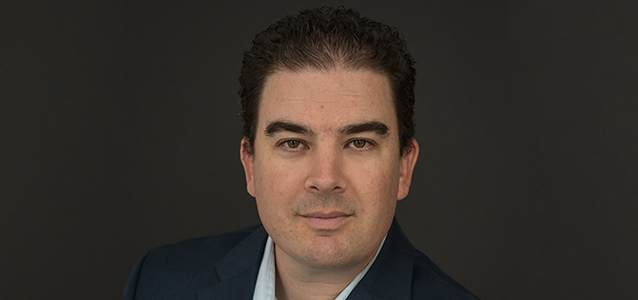
Referent
Cameron Bruce
Mechanical Design Manager, ATS Industrial Automation.
Transkript
Hello, and welcome to Battery Design Authority – What 90 Battery Lines Have Taught Us. During this presentation, we will explore the challenges in the EV industry and some of the emerging trends and patterns as we reflect on more than two decades of EV automation. You will no doubt notice one of the common themes I’ll mention today is the pace of the EV industry. Considering this, we’ll also continue the discussion on how everyday matters.
My name is Cameron Bruce, and I’ll be taking you through some of the challenges with the automotive transformations from over 100 years of ICE production to the future EV market. I’ve been a part of the ATS team for over 15 years, designing automation in a variety of fields including medical, nuclear, consumer products, and traditional automotive programs.
With the shift to EV, opportunities arose to contribute to this new and exciting industry. I took a lead role in several large-scale module and pack assembly projects. With experience in cylindrical and pouch cell automation. I can say that success in this business still takes creative solutions to tailor equipment to specific customer needs. But there is no doubt that as time goes on, and ATS installs more and more projects, I’m starting to see trends in what is and what is not successful. As an EV owner, I understand the appeal and benefits of an electrified future. And I’m convinced demand will outstrip supply for some time to come.
Agenda
Today, I want to talk about the 6 topics shown here:
1. What is design authority anyways? Why should I care about design authority?
2. Who is ATS Industrial Automation and what gives them prestige to tell us about design authority?
To help answer this question, I’ll spend a bit of time today outlining who ATS is, and what gives us the confidence when talking about design authority.
3. Problems or challenges still in EV automation, mainly product design and scale.
4. A clean hand off.
5. Industry trends.
6. Lessons from our experience with 90 battery assembly lines.
However, I think the key takeaway from this talk is the focus on the difference between a vendor, a partner, and an organization with design authority. So, let’s get to it.
Design Authority Value
Design authority comes from problem solving, learning what works, what doesn’t, and more importantly, why. Design authority doesn’t just apply at the discovery phase with the sales team, or during the requirements definition phase, applications response, complete detailed design, integration, or final onsite run off. Design authority is applied throughout all these steps, guiding decision making, and collaboration between organizations. A vendor makes what is ordered. But a partner with design authority brings skills and experience to investigate and advise on the best practices to provide real solutions.
Our customers are the experts in battery development, and what is needed to satisfy the performance metrics of their customers. Design authority and battery manufacturing is about how to effectively enable our customers to reach those metrics. The type of confidence to constructively challenge what you’ve been presented doesn’t come from one or two projects. No one is an expert after one or two attempts at the same activity. And it certainly doesn’t come from getting it right all the time. Some of the best outcomes and decisions were forged out of hard lessons or building something for the first time and then reimagining it in a better form. It is a long history of development and continuous improvement that has positioned ATS where we are today.
Why We Win
And all this history didn’t happen on its own. There are a few key reasons why ATS wins.
We have a great team from an initial sale to engineering, manufacturing and service.
We use the best-in-class components, combined with a substantial design library to leverage past experiences from various industries.
Excellent project management is key to maintaining customer relationships and bi-directional trust.
I’m sure it’s clear by now that EVs are not a regional phenomenon, and it will be the future of the automotive industry. Wherever these opportunities manifest around the world, ATS has the global footprint to support and scale, to meet our customer’s needs.
Financial stability is also a key benefit to working with ATS. As you can be assured ATS will be around in the future to pick up the phone when service is required or when future expansion is needed to meet growing capacity.
ATS Business Model (ABM)
At ATS, our guiding principle known as our ATS Business Model is the foundation to why we win, and the driver behind some of the points I mentioned in the previous slide. While it leads improvement in many aspects of our business, the focus on people first, process second, and then performance has enabled ATS to grow and succeed.
ATS Industrial Automation
With a deep-rooted history in turnkey automation — an ever-expanding capability set — ATS has the capacity and flexibility to partner around the globe to work with our customers to reach common goals. This includes expertise in specialty automation, nuclear tests, digital twin, and we are certainly no strangers to the E-mobility market.
We have 20 years of experience in the EV industry, from EDU’s, to pack assembly, to high-speed module lines, and cell construction. ATS has participated in nearly all aspects of EV manufacturing. We have centers of excellence in Germany, Slovakia, Canada, Ohio, and Michigan. As a global organization, we leverage each other’s strengths and capabilities to produce some of the world’s most exciting and challenging projects. For example, in the automotive industry, throughput and efficiency are everything. With the combined effort of these highly specialized regions, we’re pushing the boundaries to serve our customers in ways that matter to them. This includes increasing scale and speed to drive EV pack assembly lines to target more than 60 jobs per hour.
Also, ATS has been making waves in the industry and in the regions we work. Numerous publications have highlighted some of the exciting work we’re completing, and several new groundbreaking projects and facility launches have brought new opportunities and jobs to our existing locations. Just this year was the grand opening of our additional manufacturing facility in Lewis Center, Ohio. We’ll see our workforce in that region expand up to 600 jobs by 2025.
Last year, I made several presentations on how a shift in perspective is required and how the industry needs to move from vendors to partners. I’m here now to build on that message, that not only are partners critical, but building relationships with companies possessing the breadth of experience and talent is how our customers can leverage ATS’s design authority, and everything we’ve learned and tried over the last 20+ years. Next, we’ll look at a few technology case studies that exemplify where ATS has a proven design authority.
Modular Assembly
Shown here (7:47) is a simplified process flow of a module based on pouch cells. And while what’s shown here isn’t the full scope of battery manufacturing, it’s a good case study of ATS’s in depth knowledge of these processes and the pitfalls in automation and product design.
Incoming Validation
First up is incoming validation. The success of a battery pack starts with ensuring the quality of the incoming cells, cells need to be as balanced as possible to maximize capacity and charge rates. They also need to be traced with incoming inspection forms, have a birth certificate of any given cell as it makes its way into the battery pack, and ultimately be traced during the installation into the vehicle.
Barcode scans and open circuit voltage testing with rapid reject and sorting schemes are critical. More importantly, this is the front of your process. It needs to be the most reliable and available to supply the rest of the system. ATS has developed handling technologies for various form factors, both cylindrical and pouch to give downstream processes the best shot at maximizing reliable throughput while maintaining quality.
Tab Formation
Next, in this example process flow is tab formation. Again, more specific to pouch designs and preparing cells for stacking, proper stringing and module configuration is another early step that not only needs to be reliable, but highly flexible. Tabs may require multiple form configurations depending on where they fit into the stack.
The issue is how do you achieve numerous custom forms on the incoming product that must be selected on demand and then rejoin the main production stream? It is not practical to batch produce these tap configurations when dealing with this amount of volume. And diverting cells through multiple material flow streams is a significant floor space demand.
It’s taken ATS decades to develop one of the most robust and capable material handing platforms known as SuperTrak CONVEYANCE™ Platform. Customers can access this intellectual property and immediately recognize the benefits of a high-speed asynchronous material handling system that can deliver products only to the forming tool required. No batches, it’s on demand, it minimizes footprint, and has high throughput.
Final Array Assembly
After tab formation, the cells are ready for final array assembly or stacking. All pouch cell modules have some form of stacking or layering cells on top of each other to form the cell array. While simple in principle, after all, you’re just layering pouches on top of each other, several factors are critical. First, the correct order of components must be selected and placed. Again, this sounds simple, but consider what happens when a machine faults midway through the construction of a stack, which results in scrapping the current part in the gripper. How should the machine gracefully recover? What material is available lineside to replace the scrap component?
Second, we’re often not just layering pouches, but a multitude of components, including membranes used for isolation, compression material, thermal brakes, and internal module structures. These materials must be available lineside to a densely packed assembly area.
Finally, this is the last opportunity to influence the position of the cells in the stack before they must be handled as a group for module assembly. Therefore, precise alignment of the cells, specifically their tabs, is crucial. Getting this step wrong increases the risk of significant assembly and safety concerns further down the line.
Module Build
Now you’re starting to see a group of cells more closely represent the module. And now we’re on to one of the trickiest process steps — module build.
In module build, the structure of the product is introduced. It often requires compression of the stack built in the previous step to fit the module casing. Again, compression on its own is not complicated. Still, ATS has employed clever solutions to handle the material effectively and apply the necessary compression and additional components to the stack to complete the module. It’s also at this stage, where it’s common to introduce the cooling plate as cooling is a necessary component of module assembly.
To achieve effective cooling, air gaps need to be minimized. So cooling plates often arrive to a module assembly pre-applied with thermal interface material or TIM in a dispense process. Not shown on screen here, but I wanted to take a moment to highlight the importance of TIM dispense. As material sciences for low specific gravity and highly thermally conductive materials continue to evolve, TIM is becoming less abrasive, less damaging to processing equipment, and even injectable in some cases. The optimum distribution of TIM will promote battery cooling more effectively while keeping weight down. While not suitable for all battery products, applying TIM is a crucial process step that requires substantial equipment investment, and can be iterative to get it right. TIM is almost exclusively a two-component material and thus must be metered carefully. It’s typically heavy and highly abrasive.
A common approach is to mount servo metering equipment to the elbow of a six-axis robot and allow the robot to trace the pattern. And provided there’s sufficient cycle time, this is a highly flexible and suitable approach. However, this may not produce the required volumetric flow to meet total throughput, thus, additional stations may be required. This multiplies the capital cost of the dispense and motion platform equipment. ATS has experienced developing robotic systems for maximum flexibility and bespoke dispense solutions that optimize pattern density. After TIM is dispensed, it’s typically concealed in a product and never seen again. Knowing that you’ve dispensed the correct amount of material in the right location is critical to a quality product. Real-time volumetric monitoring, through laser scanning tools can measure the profile during dispense and guarantees the correct amount and shape of material was applied.
Final Assembly
The bulk of the module is now produced, time for final preparation starting with tab bend. In the final module assembly, all the tabs and connection points protruding from the module case are prepared for final joining or welding. While not the most complex step in the process, ensuring tabs and connection points are in good contact is vital to our next step.
Intelligent Welding
Once tabs are successfully formed in place, we can begin another critical step — laser welding. If there’s one process in this entire fabrication of a module, regardless of if it’s a pouch or a cylindrical cell that is most critical to quality, it’s laser welding.
An automation partner who is an expert in laser welding is in necessity. Laser welding has emerged as the preferred technology for cell bonding to the lattice structure. With our in-house lab, ATS can develop welding processes for customers with similar or dissimilar metals, or perhaps develop an aluminum welding process without filler wire or shielding gas while still producing quality welds. However, welding components not in contact with each other usually yield poor results. ATS has developed dozens of laser weld clamping applications to achieve a reliable zero gap, while working around intricate geometry of battery design and being nonconductive when necessary.
Finally, ATS can provide fully automated solutions in either standard or customized Class 1 Laser Enclosures for safe operation on the factory floor. Deviating slightly from the pouch cell example we’re looking at here, consider a typical EV battery pack full of cylindrical cells. Upwards of 6500 cells can be strung together, each requiring a connection to a positive and negative terminal resulting in 13,000 individual joints. In this required volume, this is only economical through a robust laser welding process.
Each weld site is critical to product quality, and a bad weld directly impacts vehicle performance. In a production process with a 98% first time quality pass rate, a weld process with 13,000 welds needs to have a 99.98% success rate. And there’s more. This process needs to be fast. 3D galvo heads can weld very quickly, but the real trick here is the robust automated clamping solution — mentioned earlier — that reliably couples the bus strings to the cells while at the same time working around product geometry. That zero gap between the lattice structure and the cell surface is vital to a good penetration weld.
ATS Intelligent Welding
What separates ATS from other companies is our strong partnership with some of the industry leading laser manufacturers to develop new technologies such as integrated real time monitoring with scanning galvo weld heads. This monitoring can not only inspect the quality of each weld by measuring the keyhole of the weld directly but can also be fed forward to the primary process laser fiber or motion platform. This allows tooling to course correct or modulate power. Gone are the days of indirectly measuring the weld by visualizing the plume. Coaxial process monitoring lasers can see through the effluent and plumes given off by the process to measure various features while simultaneously welding. This direct measurement is the secret sauce to real time weld monitoring and ensures the highest quality process.
Process Validation
To build on the value of real time monitoring, consider that the end of line testing might result in 1000s of dollars in scrapped work in progress until a weld problem is identified. Maybe one of the sites in the clamp matrix has become damaged, and there are now repeated weld failures at that contact site over dozens of modules. With process monitoring and careful development, these weld failures are identified at the source and can be dealt with immediately. Validation of this real time technique is also essential to build process confidence. This can be handled in ATS’s dedicated laser lab via tensile strength tests and cross-sectioning to verify the weld penetration and strength. And of course, knowing this information earlier in the stages of your product development is better than later.
Does your automation supplier have the facilities and lab equipment to support and test your process? Or demonstrate process capability through samples and coupons before the final product is complete? It’s not uncommon to submit coupons or pre-production level components to a laser lab for process validation. And prototype work is just the beginning. ATS does not stop at the lab. We use this early development knowledge and the lessons learned with our customers to design and build world class production laser welding equipment.
Final Quality Checks
The module is now largely complete, time for final quality checks before packaging. Knowing that batteries in either modules or packs meet their desired metrics is essential to validate key processes before ramping up to production. Whether it is incoming cell inspections such as open circuit voltage measurement, or leak testing on the coolant circuit. Each successful production line has both in-line and offline testing to help minimize scrap and ensure a quality product. Other essential testing requirements are likely to include HIPOT test, DCIR testing, and low voltage circuit testing to validate that the batteries internal voltage monitoring system is functioning correctly.
To couple with the connection points on the cell module or pack, the automation tooling may require custom connectors to ensure long lasting and reliable contact. On the back end of testing is the databank of all this information. So, each product has a credible birth certificate from the production floor to the final consumer.
We quickly step through a process based on pouch cell manufacturing and touched on several processes related to that workflow. There are many more from which ATS has developed design authority. To mention a few; adhesive dispense when joining cylindrical cells to their carriers, module case welding, sealing of the pack enclosure, and finally complete pack charge and discharge cycle testing, are all additional essential areas in EV manufacturing. And with all our exposure to different technologies, processes and customers, we’ve noticed a few pervasive themes.
Product Design & Scale
Every project that’s come across our desk has these two issues — product design and scale. There isn’t an EV battery project that hasn’t struggled with either of these two fundamental challenges. Product design is constantly challenged with performance targets and manufacturing realities. At the same time scale tries to grapple with the enormity of these projects and the race to make them production worthy. Let’s have a look at the scale element first.
Will EVs Surpass Regular Combustion Vehicles?
Well, it’s no longer a question of if it’s a matter of time. Companies worldwide — both the traditional organizations and the disruptors — are racing to keep pace with the EV industry’s relentless change. Developing a product concurrently with the manufacturing capacity to support the demand is a front-page problem for any organization considering getting into the broader market.
Global EV Volumes
And it only takes a few quick searches to see the rapid growth of the EV industry. The year-over-year sales growth is showing no signs of slowing down. Having weathered a global pandemic and now on the backside of two years of substantial uncertainty. While overall vehicle sales remain stagnant, EV sales continue to eat away at a larger and larger portion of the market.
Global EV Sales
The previous slides (22:13) showed us where we’ve come from, and it’s that data that forms these projections into the future. As you can see here (22:38), the demand is expected to exponentially increase as the industry moves to produce upwards of 45 million vehicles by 2030. Combined with other transportation demands like commercial trucking and public transport, as well as grid storage, the need for battery production is overwhelming.
Footprint Challenge
But all that continued growth undoubtedly gives rise to risks. For example, the floor space alone to launch these programs is daunting. ATS has built module lines with an annual production volume of 530,000 modules equivalent to 38,000 battery electric vehicles occupying the same total footprint as an Olympic swimming pool. In a separate application, module production lines with a total output of 1 million modules that could support an annual vehicle production volume of 100,000 units was specified but needed two full soccer pitches. And that was just to build the modules. To get the modules into packs, the equivalent of an additional 19 basketball courts was laid out for that same program. And while that was true last year, it’s grown again to increase footprint further. All in all, producing 100,000 high mileage vehicles annually, consumed just over 22,000 square meters, or nearly 240,000 square feet.
Floor Space
Massive battery facilities are either already built or under construction around the world. Some of these facilities are new builds and others have chosen to repurpose existing traditional automotive space for renewed manufacturing purpose. But can all this floor space — not to mention the tooling to fit into these buildings — be secured in time? Now think back to where EV sales are going if EV sales hit 20 million units annually by 2025 and understanding that today’s production lines can produce roughly 100,000 units per year, 200 battery pack production lines will be required.
Finally, considering SOP is a two-to-three-year lifecycle you can quickly see that planning for this footprint on the OEM floor is critical, but also consider that capacity is required on the automation suppliers’ floor within the next year or sooner to support the OEM timing. These companies must procure new space to accommodate customer requirements and don’t necessarily have the option to repurpose existing facilities to take on the workload. Companies worldwide, ATS included, are constantly expanding their footprint and capacity to construct these large battery production lines.
And as challenging as solving the floor space issue is, getting the product design right is even more complex. Throughout the design, there’s no shortage of pitfalls along the tightrope. There’s no doubt that the entire industry is still learning. There have already been many companies — some you’ve heard of and others you may not have — that could not convert good ideas into production reality. On top of that, we’ve seen organizations wrestle with the end of the line for their existing combustion platforms and the need to decide whether new EV platforms should attempt to integrate into a universal chassis between ICE and EV drivetrains. While this sounds like a reasonable transition, there are plenty of tradeoffs to this approach compared to what is emerging as the industry standard skateboard design. And even if companies leap to a skateboard chassis, it’s still a new platform, requiring new vehicle dynamics and assembly lines. It’s natural that this forms a continuous source of change, both before and after started production.
On top of that, batteries for electric vehicles are still a relatively young industry and are constantly changing to keep up with performance and regulatory requirements. At the same time, securing the volume of batteries and other crucial components to satisfy the requirements is still no small feat in today’s incredibly tight supply chain market. This includes the automakers’ ability to produce good quality parts to supply to the automation equipment. It’s also true that with 100 years of development, ICE manufacturing has honed this process to a 95% or greater overall equipment efficiency. But in many respects, we’re starting over again. And these designs for EVs and equipment often run at far reduced rates. Finally, new technologies require a workforce with a unique skill set and training, both on the production floor and in the engineering and design phases, as new technologies are being considered.
Optimal Engagement
Finally, there’s the timing. When do you take an idea and present it to the world? When do you take a vehicle idea out of R&D, and start considering manufacturing? The truth is, there isn’t a time when it’s too early to start, but it sure is easy for companies to get ahead of themselves. To put a point on this, we’ve worked with companies who are more concerned about the amount of fume extraction required in their building before selecting which materials are needed for dispense.
Using DFM and DFA with an automation partner who already knows what is needed, is how early engagement can pay off. They will not only have familiarity with the materials required for product design, but also experience with any auxiliary equipment required to support a given process. However, it’s too late to benefit from sound manufacturing principles if the product design has been frozen without considering some key points.
A true partner also understands the need for flexibility. There is no shortage of factors that affect product design and remaining flexible in the design phase of automation to keep up with the changing product is how strong partnerships succeed. But this comes to a point, at some time the machine will need to be built and requires parts per the agreed design to validate machine performance. Pushing prototype builds and nonproduction intent parts through machine acceptance is a common problem in the industry. It often results in the final integration of the machine on the customer’s floor, as production parts become available for the first time. Experienced manufacturers understand this and have staff capable of supporting their customers right through the start of production and beyond.
Industry Trends
There are a few other trends that we’re seeing in the industry. The race is undoubtedly on to transform transportation. All automakers now are pushing hard to gain as much market share as possible. This means getting to volume production in two to three years, not five. It means the simultaneous design of the product dunnage, ASRS, factory and the equipment to fill it. It took combustion vehicles 50 years to get to a point where production of 30 million vehicles annually was possible. The EV industry is pushing to achieve the same goal and less than 10 years.
Growing Regulations
On top of the compressed timelines, EVs are also navigating new regulatory spaces. I thought this slide (30:15) was interesting; It’s a measure of the number of pieces of legislation related to the EV industry by respective governments. It includes new regulations from production targets, to safety requirements, to charging ambitions, and battery swap stations. Governments worldwide are incentivizing all aspects of the EV industry to be creative and rise to meet environmental and safety targets for all of us. As you can see, the most significant activity is also in the 3 largest EV markets, namely China, Europe and North America. Why does this matter? It’s another consideration for product designers and production supervisors to remember when scoping out EV programs.
The Magic Triangle
All of this is going on at once, design, scale, compressed timelines, and regulatory requirements. What’s the result? Consider this magic triangle of factors converging to form a perfect storm for supply chain capacity.
Rapid Speed of Technology Improvements
Battery technology is changing and improving rapidly. We’ve seen this in both performance enhancement and regulatory requirements. Lithium ion is the core technology of today, with many recipe developments to improve capacity in charge/discharge times. And what’s next? Solid state batteries are on the horizon. While none are ready for mainstream production, their arrival could shake up existing supply chains as companies pivot to obtain the most competitive technologies.
Project Timing
Second, as we’ve discussed, battery assembly projects take two to three years from project start to full production ramp up. Batteries are complex multidisciplinary programs requiring substantial capital and time investment. EV batteries are integral to vehicle design and need SOP timing that aligns with the remainder of the vehicle chassis.
Limited Flexibility Built into the System
Third, automated assembly lines can be challenging to alter if not engaged early enough. For example, what if solid state batteries come into the market? Will the existing product design roll the latest technology into the current form factor? Or will these new batteries take on an entirely different shape? This makes an automation project a moving target. And as a result, programs with more than 400 change orders are not uncommon in the production landscape.
Battery packs are not a commodity, they require a full vehicle system integration and analysis to be successful. And with so many interdependent elements, change is inevitable. If the automation equipment can’t adapt to an evolving product, tooling can quickly become obsolete. This could throw the development of an electrification program into chaos, and put the automaker behind the eight ball, while others are rapidly consuming more significant market segments. Battery pack assembly is not a solved problem. And there was a lack of capable supply base to mitigate supply chain risks. Not addressing these risks early in the development can leave some automakers with nowhere to turn if plan A does not work.
This last point is significant. Automakers are aggressively locking up capacity worldwide to secure automation partners. And those with history and design authority are the first to be secured. Organizations with a history of getting large scale projects to launch quickly and successfully are becoming a scarce commodity. Some automakers may be left without a seat when the music stops on manufacturing capacity.
Another industry trend that we’re seeing is the compression of throughput. I’ve experienced this personally when a project at launch was slated to operate at a tack time of 180 seconds, only to have it reduced to 90 seconds while doubling the size of the line. And just when we thought we’ve squeezed the maximum out of the footprint and optimized performance, the customer requested that the facility be expanded and drove throughput higher again. Only careful planning and strategic upgrades to critical aspects of the line made these continual improvements possible. Organizations that excel in this area have a strong foundation in manufacturing, optimization, and simulation. Knowing what to do is just as important as being able to demonstrate to your customer that their capital dollars will directly improve the bottom line and in automation, that’s throughput.
Lessons Learned
And by no means were we experts out of the gate. We certainly picked up some lessons learned along the way.
Despite all the different form factors, implementation strategies, and manufacturing methods, there is still no clear winner on the best cell form factor; prismatic, pouch and cylindrical cells all have economic and production pros and cons and risks along the way. For example, those leaning towards a cylindrical cell technology, which location on the cylindrical cell have the best chance of success for coupling to the module bus structure? With 1000s of individual bonds, this critical design consideration will ultimately affect module design and pack layout. For those considering pouch cells, which tab trim and bend profiles guarantee the best conditions for successful welding? And for prismatic cells can the additional weight of the case be balanced against the handling benefits?
Value of a Design Authority
Back to design authority. Over time, partners with design authority have already invested so much intellectual capital into the key processes to make battery manufacturing successful, they no longer need to start from a blank page and think about how to, for example, stack pouch cells together or dispense potting into the interstitial spaces of cylindrical cell array, or how to test at any one of the stages of pack development. Partners with design authority have a vast library of experience and designs that can be adapted to suit specific customer form factors, while retaining the core conceptual design intent that makes for a successful process. This allows our customers to bypass the development and costly tooling iterations, and access solutions applicable to their unique applications the first time.
Supply Chain
However, having design authority doesn’t mean that you have complete control over the situation. I’ll bet there isn’t a company out there that hasn’t in some way been affected by the global supply chain crisis. Last year, I highlighted the impact of the chip crisis on the automation components. Unfortunately, in the last 12 months, the situation has only expanded to include more basic commodities like cables and other seemingly ordered, ordinary electrical components. All the planning in the world cannot accommodate for a supply chain that can’t source or deliver parts.
Component lead times necessary for machine build have blown past what was previously days and weeks and are now in the months to years’ timeframe. But when we’re smart, we use our experience to identify long lead risks early and work with our customers to share the risk of ordering components long before the line takes shape. It takes knowledge and confidence to specify components knowing they will successfully pair with the automation equipment before the design is complete.
Timeline
Hand-in-hand with supply chain concerns are getting the timeline correct. Making sure components arrive on time is just a piece of the puzzle. Everything we’ve talked about so far affects timelines which are on top of mind for everyone. Project timelines often extend rather than pull in from baseline plan. There’s too much to consider in a simultaneous product and automation design path. Product designs that may be valid one year, could be affected by regulations, vehicle crash testing, industry safety trends, or even performance increases from the competition. As mentioned before, having all the components available on time at the location is a monumental task. Something as simple as a connector or a fastener can grind the entire process to a halt. This makes closing projects difficult and strains automation suppliers to free resources in human capital and floorspace to take on future projects.
Pilot to Production
One of the trends and lessons we’ve observed is to put in a pilot or a low volume production line ahead of an entire production system. There are substantial benefits to this approach. Pilot lines typically focus on key processes like dispensing, forming, and welding, without the investment in full automation and material handling. A low volume approach allows vehicle manufacturers to produce prototypes with production and intend tooling to provide a close feedback loop with the equipment to make quick modifications and iterate on design ideas.
The automation supplier is afforded time to roll out complete production material handling strategies for simulation and throughput. While knowing that reserve space for critical process equipment will be filled by mature designs capable of production on day one. But overall, it de-risks the investment on both parties until the best solution is understood, and then scaled to meet the total objectives of the customer.
Set Teams Up for Success
Having a solid plan and an approach to production is essential. If you think the game musical chairs is stressful, consider that multiple customers approach some suppliers, and with only limited capacity, suppliers are choosing in which customers to place their trust. For some suppliers pursuing a rush customer who has not engaged early enough in the product design stage lacks a solid growth model for a systematic execution plan, can be an incredibly risky and burdensome task. Failed projects of this scale would simply bankrupt some other automation houses. Suppliers are looking for customers who can engage on the engineering and senior leadership levels to work together to build a solid plan to get to market. But the right customer and an automation partner with design authority can really drive the future of what’s possible in manufacturing.
Take-Aways
I think here it’s worth repeating why design authority is so important. It enables customers with demanding projects to partner with organizations like ATS, to help them bring ideas to reality. Design authority is the culmination of experience, identifying trends, and lessons learned. It’s knowing what works, what doesn’t, and why. What design authority does for our customers is it allows them to get to market in the fastest, most reliable way, making use of strategies to mitigate schedule and reduce risks. A partnership with design authority is what’s necessary to stay ahead in today’s competitive electric vehicle landscape.
I want to close by saying on a personal level, how excited I am to be part of an organization that’s shaping the future of the automotive industry, and one that has the experience and the confidence to make a difference for our customers. I see a bright future for what EVs mean to our everyday way of life, not only for obvious environmental and energy security reasons, but also for our pure driving enjoyment and mobility opportunities for upcoming generations. Because of this, it’s clear to me and to all of us at ATS, that everyday matters bringing this future to reality.
Thank you very much for your attention today, and I look forward to working with you in the future.
Jedes Projekt ist einzigartig. Wir möchten uns Ihre Herausforderungen anhören und Ihnen mitteilen, wie Sie Ihr Projekt durch Automatisierung rechtzeitig auf den Weg bringen können.