Produktionsverzögerungen sind eine der größten Herausforderungen für moderne Fertigungsunternehmen. Sie können den Netto-Barwert eines Produkts um beträchtliche 15 % und 35 % mindern und die Wettbewerbsfähigkeit eines Unternehmens erheblich beeinträchtigen. In einer globalisierten Wirtschaft, die von ständig kürzeren Produktlebenszyklen und hohem Innovationsdruck geprägt ist, ist es für Hersteller unerlässlich, ihre Produktentwicklung von Grund auf neu zu überdenken. Die Antwort auf diese Herausforderung liegt im **Design for Manufacturability (DFM)** – einem integrierten Ansatz, der die Fertigbarkeit bereits in den frühesten Phasen des Produktdesigns in den Mittelpunkt stellt.
DFM verstehen: Warum die Produktionsfähigkeit bereits in der Entwicklung zählt
Das Verständnis der Hauptursachen für Verzögerungen in der Produktionslinie ist entscheidend für einen reibungslosen und effizienten Fertigungsprozess. Produkte, die erfolgreich in einer Prototyp- oder Kleinserienproduktion hergestellt wurden, können beim Hochskalieren auf die Massenproduktion Probleme verursachen. Je mehr Produkte in höheren Geschwindigkeiten montiert werden, desto größer ist die Wahrscheinlichkeit von Problemen in der Montagelinie.
Dies liegt daran, dass Prozesse, die in früheren Phasen gut funktionierten, bei einer Skalierung häufig nicht mehr den Standards entsprechen. Wenn sich Montageschritte nicht korrekt skalieren lassen, können Produktfehler entstehen. Häufig müssen Prozesse überarbeitet werden und erfordern möglicherweise neue Montage- und Testgeräte.
Das frühzeitige Ansprechen dieser Probleme in der Produktdesignphase durch die Umsetzung einer DFM-Denkweise ist essenziell für einen reibungslosen Produktionsstart.
Umsetzung des herstellbarkeitsbezogenen Designs (Design for Manufacturability, DFM)
Das übergeordnete Ziel von DFM ist klar: Es geht darum, die Produktion zu vereinfachen, die Produktqualität nachhaltig zu verbessern, Herstellungskosten signifikant zu senken und kostspielige Verzögerungen von vornherein zu vermeiden. Das Kernproblem, das DFM adressiert, ist oft erst bei der Skalierung offensichtlich: Ein Produkt, das im Prototypenstatus oder in Kleinserien noch perfekt funktionierte, stößt bei der Massenproduktion an seine Grenzen. Prozesse, die bei geringen Geschwindigkeiten und Volumina problemlos abliefen, erfüllen bei hohem Tempo nicht mehr die erforderlichen Qualitätsstandards oder sind schlichtweg nicht effizient genug. Dies resultiert in erhöhtem Ausschuss, Nacharbeit, aufwendigen und teuren Prozessüberarbeitungen oder sogar der Notwendigkeit, komplett neue Produktionsanlagen anzuschaffen. Ein **proaktives DFM-Mindset** bereits in der Konzeptionsphase ist daher absolut entscheidend, um einen reibungslosen und wirtschaftlichen Produktionsstart zu gewährleisten. Es geht darum, Probleme zu antizipieren und zu eliminieren, bevor sie überhaupt entstehen können.
DFM strategisch implementieren: Von der Idee zur effizienten Fertigung
Die wirksamste Implementierung von DFM beginnt nicht erst kurz vor der Produktion, sondern bereits in den allerersten Phasen der Produktentwicklung – konkret während der Ideenfindung und der Machbarkeitsstudie. Hier werden die Weichen für den späteren Erfolg gestellt:
- Frühe und systematische Integration von DFM-Prinzipien: Jede Designentscheidung sollte von Anfang an die spätere Fertigung im Blick haben. Dies umfasst die sorgfältige Berücksichtigung von:
- Standardisierung von Teilen: Die Nutzung von Standardkomponenten reduziert nicht nur Kosten und Komplexität, sondern vereinfacht auch die Beschaffung und Lagerhaltung.
- Kompatibilität mit bestehenden Prozessen und Anlagen: Kann das neue Produkt mit vorhandenen Maschinen und Methoden gefertigt werden, oder sind teure Anpassungen oder Neuanschaffungen nötig?
- Realistische Toleranzen und Spezifikationen: Engere Toleranzen bedeuten oft höhere Fertigungskosten. DFM hilft, ein Gleichgewicht zwischen notwendiger Präzision und wirtschaftlicher Machbarkeit zu finden.
- Betrachtung der gesamten Produktionskosten (TCO): DFM blickt über die reinen Materialkosten hinaus und berücksichtigt Arbeitskosten, Energieverbrauch, Werkzeugkosten und Abfall.
- Skalierbarkeit und zukünftige Volumina: Ist das Design inherent für eine spätere Erhöhung der Produktionsmengen ausgelegt?
Aktives Einholen von externem und internem Feedback
Vertrauen ist gut, Kontrolle ist besser. Ziehen Sie externe Experten – beispielsweise von ATS Industrial Automation – für Montage und Tests hinzu. Ihr unabhängiger und erfahrener Blick auf das Design und den vorgeschlagenen Herstellungsprozess ist von unschätzbarem Wert. Sie können potenzielle Stolpersteine und Engpässe identifizieren, bevor diese zu kostspieligen Verzögerungen in der Serienproduktion führen. Gleichzeitig ist auch das Feedback aus den eigenen Reihen – von Produktionsingenieuren, Werkern und Qualitätsmanagern – unverzichtbar.
Design-Simplifizierung ohne Kompromisse bei der Funktionalität
Weniger ist oft mehr. Reduzieren Sie die Komplexität von Komponenten, die Anzahl der Materialien und die Schritte in den Montageprozessen. Ein einfacheres Design führt in der Regel zu weniger Fehlern, schnelleren Produktionszyklen und geringeren Herstellungskosten. Dabei ist es entscheidend, dass diese Vereinfachung die Kernfunktionalität, die einzigartigen Merkmale und das geistige Eigentum des Produkts nicht beeinträchtigt. Es geht darum, intelligente Reduktionen vorzunehmen, die den Fertigungsprozess optimieren, ohne das Produkt zu kompromittieren.
Die unverzichtbare Rolle von Proof-of-Principle (POP)-Tests
Während theoretische Modelle und Simulationen wertvolle Erkenntnisse liefern, ist die praktische Validierung von Designs unerlässlich. Hier kommen **Proof-of-Principle (POP)-Tests** ins Spiel. Sie sind der entscheidende Schritt, um DFM-Ergebnisse nicht nur auf dem Papier, sondern auch unter realen Bedingungen zu bestätigen und sicherzustellen, dass Ihre Designs tatsächlich für die Massenproduktion geeignet sind.
- Praktische und realitätsnahe Validierung: Führen Sie physikalische Tests mit frühen Prototypen durch. Dies ermöglicht es, die Herstellbarkeit unter Bedingungen zu überprüfen, die denen der späteren Serienproduktion so nahe wie möglich kommen.
- Generierung von verwertbarem Feedback: Die Ergebnisse von POP-Tests liefern entscheidendes Feedback. Sie zeigen auf, welche Aspekte des Designs oder des Prozesses noch verfeinert werden müssen, um die gewünschte Effizienz und Qualität zu erreichen.
- Frühzeitige Risikominderung: Indem potenzielle Probleme und Engpässe bereits in der Testphase aufgedeckt werden, minimieren POP-Tests die erheblichen Risiken, die mit einer späteren Skalierung der Produktion verbunden sind. Sie verhindern teure Überraschungen im vollen Produktionsbetrieb.
Ein Praxisbeispiel aus der Automobilindustrie: DFM in Aktion
Ein anschauliches Beispiel für den Wert von DFM liefert ein führender Automobil-OEM. Dieser stand vor der Herausforderung, einen komplexen Laser-Schweißprozess für ein neues Batteriemodul in die Massenproduktion zu überführen. Obwohl der Prozess bei geringen Stückzahlen in der Entwicklung einwandfrei funktionierte, traten bei höheren Produktionsraten erhebliche Probleme auf: Die intensive Wärmeentwicklung beim Schweißen erhöhte das Risiko thermischer Ereignisse – ein kritischer Faktor bei Batterien.
In enger Zusammenarbeit mit ATS Industrial Automation wurde der Prozess durch die Brille des DFM analysiert. Die Empfehlung: Eine Materialänderung des Batteriemodulgehäuses. Diese scheinbar kleine Anpassung, die bereits in der Designphase hätte berücksichtigt werden können, reduzierte die Wärmeentwicklung beim Schweißen erheblich. Das Ergebnis war eine signifikante Minimierung des Risikos thermischer Ereignisse und eine optimierte Herstellbarkeit des Batteriemoduls für die Großserienproduktion. Dieser Fall unterstreicht eindringlich, wie frühzeitige DFM-Überlegungen immense Folgekosten und Risiken verhindern können.
Ihr Weg zur optimierten Produktion: Mit DFM und ATS Industrial Automation
Die Implementierung von Design for Manufacturability ist nicht nur eine technische Notwendigkeit, sondern eine strategische Investition in die Zukunft Ihres Unternehmens. Sie ermöglicht es Ihnen, Produktionsverzögerungen effektiv zu reduzieren, Ihre Kostenstrukturen zu optimieren und die Qualität und Marktreife Ihrer Produkte zu sichern.
Benötigen Sie umfassende Unterstützung, tiefgehendes Fachwissen oder strategische Beratung bei der Integration von DFM in Ihre Produktentwicklungsprozesse und der Optimierung Ihrer Herstellungsprozesse? **ATS Industrial Automation** steht Ihnen als erfahrener Partner zur Seite, um Ihre Fertigung auf die nächste Stufe der Effizienz und Rentabilität zu heben.
Jedes Projekt ist einzigartig. Wir möchten uns Ihre Herausforderungen anhören und Ihnen mitteilen, wie Sie Ihr Projekt durch Automatisierung rechtzeitig auf den Weg bringen können.
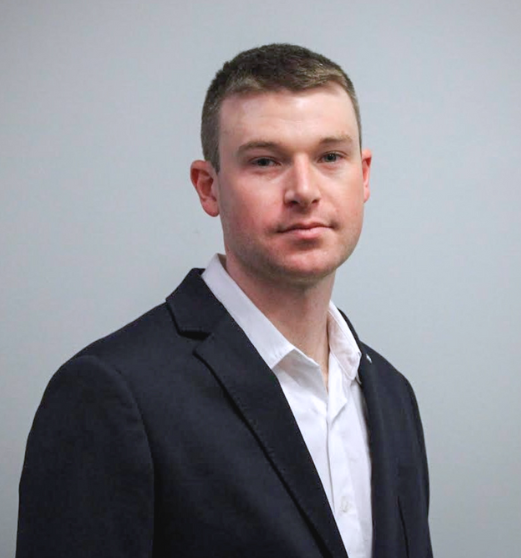
Kevin Peake
Key Account Manager
ATS Industrial Automation
Kevin Peake hat Unternehmen in zahlreichen Branchen dabei geholfen, die Produktion zu automatisieren und zu optimieren. Er hat einen Bachelor of Science in Luft- und Raumfahrttechnik sowie Maschinenbau. Er liebt Roboter und baut sie in seinem Keller zum Spaß. Es macht ihm Freude, Kunden bei der Konfiguration von Systemen zur Erhöhung der Produktionskapazität und Steigerung der betrieblichen Effizienz zu unterstützen.