Projekte für Elektrofahrzeuge (EV) und Energiespeicher zeichnen sich zunehmend durch enge Fristen und sich verändernde Spezifikationen aus. Dieses dynamische Umfeld erfordert flexible und anpassungsfähige Lösungen, die sich häufig während der Angebotsentwicklung, der Projektentwicklung und der Umsetzung wiederholen. Bei diesen Projekten ist die Entwicklung einer Strategie zur Minderung der finanziellen Risiken im Zusammenhang mit stark vorgezogenen Investitionsausgaben (CAPEX) ein wichtiger Aspekt.
Modulare und flexible Produktionslösungen für die Montage sind unerlässlich, da sie sich mit den Produkt- und Marktanforderungen weiterentwickeln können. In Anbetracht der schnellen Verbreitung in der Branche und der anhaltenden Vielfalt an Verpackungsdesigns und Batteriechemien werden diese Systeme wahrscheinlich häufiger umgerüstet werden müssen, um mit den technologischen Fortschritten in der Branche Schritt zu halten. Wir verfolgen derzeit aktiv bei großen OEMs eine Umstellung auf alternative Formfaktoren und Batteriechemien, was wahrscheinlich zu größeren Reinvestitionen in ihre Montageanlagen führen wird.
Fallbeispiel zu Machbarkeitsstudie für Batteriemontage
Beispielsweise sah sich ein Kunde, der sowohl Batterien für batteriebetriebene Elektrofahrzeuge (BEV) als auch für Plug-in-Hybridfahrzeuge (PHEV) herstellt, mit wechselnden Produktionszielen und sich ändernden technischen Spezifikationen infolge der sich verändernden Marktanforderungen konfrontiert. Dieses Szenario erforderte anpassungsfähige und vorausschauende Lösungen für die Batteriemontageprojekte des Kunden. Aufgrund der veränderten Marktnachfrage nach BEV und PHEV in verschiedenen geografischen Regionen rund um den Globus liegt der Schwerpunkt zunehmend auf der Skalierung der Produktion, wobei die Anpassungsfähigkeit der Anlagen im Vordergrund steht.
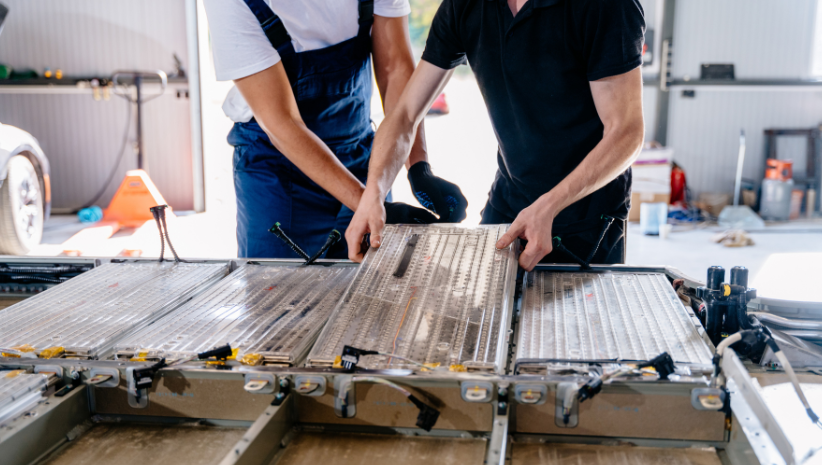
Unabhängig davon, ob Kunden EV- oder Energiespeicherbatterien bauen, kann die Durchführung einer Machbarkeitsstudie zu einem frühen Zeitpunkt in der Entwicklung eine entscheidende Rolle bei der Validierung von Batteriedesigns, bei der Bewältigung von Änderungen der Spezifikationen und bei der Gewährleistung eines reibungslosen Übergangs von der Idee zur Serienproduktion spielen.
Mit Machbarkeitsstudien können Teams Risiken mindern, Entwürfe verfeinern, die Entwicklung rationalisieren und die Projektergebnisse verbessern.
Die Vorteile von Machbarkeitsstudien
Mit Machbarkeitsstudien kann nachgewiesen werden, dass ein Produkt, ein Konzept oder ein Prozess machbar ist und erfolgreich umgesetzt werden kann. Wenn Machbarkeitsstudien frühzeitig im Entwicklungsprozess durchgeführt werden, können sie zur Optimierung der Teile- und Produktleistung beitragen und so zu skalierbaren Lösungen und anpassungsfähigen Produktionsstrategien führen. Machbarkeitsstudien bilden die Grundlage für eine erfolgreiche Fertigung mit weitreichenden Vorteilen, die es Unternehmen ermöglichen, die Gesamtbetriebskosten (TCO) während des gesamten Produktlebenszyklus zu minimieren.
Der Nutzen dieser Studien liegt meist in der Risikominderung für das Programm oder die Kosten.
Minderung von Programmrisiken
- Einblicke in die Anforderungen des Produktdesigns gewinnen: Machbarkeitsstudien bieten wertvolle Einblicke in die Anforderungen an das Produktdesign, die möglicherweise ursprünglich nicht in Betracht gezogen wurden. Sie ermöglichen dadurch eine fundiertere Entscheidungsfindung in einem frühen Stadium des Lebenszyklus.
- Frühzeitige Datenerhebung: Durch das Erheben von Produktdaten zu einem frühen Zeitpunkt im Entwicklungszyklus trägt eine Machbarkeitsstudie dazu bei, Lösungen zu verfeinern und zu validieren, bevor die Serienproduktion beginnt.
- Senkung von Risiken hinsichtlich Produktionskapazität und Betriebszeit: Die frühzeitige Erkennung und Lösung potenzieller Probleme bei der Produktion trägt zur Gewährleistung reibungsloser und unterbrechungsfreier Fertigungsprozesse bis hin zur Skalierung bei. Durch die Identifizierung von häufigen Fehlerquellen und Inhalten, die eine regelmäßige vorbeugende Wartung erfordern, wird außerdem die Grundlage für eine bessere Wartungsfähigkeit der Ausrüstung geschaffen.
Minderung von Kostenrisiken
- Minimierung der anfänglichen finanziellen und ressourcenbezogenen Investitionen: Dies ermöglicht ein frühes Engagement in neuen Programmen, beschleunigt das Erreichen wichtiger Meilensteine und reduziert das Risiko kostspieliger Verzögerungen.
- Priorisierung der Produktionsanforderungen: Eine Machbarkeitsstudie bietet frühe Einblicke in diese Anforderungen und hilft bei der Planung von CAPEX-Investitionen, die für eine erfolgreiche Programmdurchführung notwendig sind.
- Frühere Erkennung von Änderungen: Wenn Sie mögliche Änderungen an den Produktionsanforderungen frühzeitig vornehmen, können Sie die Auswirkungen auf die Kosten und den Zeitplan in der Produktion minimieren. Zudem fördert dies Gespräche über herstellbarkeitsbezogenes (Design for Manufacturability, DFM) und die Montage, die oft übersehen werden. Dadurch können außerplanmäßige Kosten, die durch Änderungsaufträge später im Lebenszyklus entstehen, reduziert werden.
Es ist entscheidend, die Gelegenheit zu nutzen, in einem frühen Stadium des Produktentwicklungszyklus greifbare Erkenntnisse aus physischen Produkten zu gewinnen, um den Rahmen für ein erfolgreiches Programm zu schaffen. Gelegentlich sind aufgrund laufender Änderungen im Produktdesign oder fehlender beständiger Marktnachfrage in einem frühen Stadium keine größeren finanziellen Investitionen möglich. Sie sollten jedoch nicht vergessen, dass die oben beschriebenen Vorteile auch mit minimalen Investitionen erreicht werden können.
Skalierung von Machbarkeitslösungen
Elektriktests und Dichtheitstests, sowohl prozessbegleitend als auch am Ende der Produktionslinie (EOL), sind ein wichtiger Bestandteil eines jeden Projekts zur Montage von EV-Batterien. Mit diesen Tests wird geprüft, ob das Produkt die spezifizierten Leistungs- und Sicherheitsanforderungen erfüllt, bevor es in die nächste Fertigungsstufe oder den endgültigen Einbau in das Fahrzeug geht. Die Entwicklung skalierbarer Lösungen für diese Testverfahren ist für EV-Batterieprojekte unerlässlich. Das Ziel jeder Machbarkeitsstudie ist es, dass die entwickelten Konzepte und Lösungen effektiv auf eine Produktionsumgebung übertragen werden können.
Beginnen Sie mit temporären Bench-Top-Setups oder einem ähnlichen Ansatz, um die Investitionskosten zu minimieren. Setzen Sie branchenübliche Messgeräte ein, um Produkt- und Produktionsannahmen zu validieren. Anschließend kann die Lösung durch zusätzliche Komplexität und Anpassungen erweitert werden, um ein endgültiges Konzept zu erstellen. Wenn die Ergebnisse der Machbarkeitsstudie vorliegen, können weitere Iterationen durchgeführt werden, oder es wird in einigen Fällen eine vollständige Änderung des technischen Ansatzes festgestellt. Durch diesen Prozess werden die Anforderungen an die Ausrüstung und die damit verbundenen Beschaffungskosten definiert, die um Größenordnungen variieren können. Eine frühzeitige Definition der Kosten hilft bei der Ausrichtung der Projektbudgetziele.
Die Skalierung einer Machbarkeitsstudie, die für eine Batteriezelle, ein Batteriemodul oder ein Batteriepack entwickelt wurde, auf ein umfassendes Produktionssystem erfordert nicht nur eine instrumentelle Ausstattung, sondern auch die Bestimmung der Anforderungen an die Wiederholbarkeit und die Verfeinerung kritischer Designkonzepte, wie etwa Werkzeuge, Vorrichtungen und Anschlüsse. Diese Prozesswiederholbarkeit muss bei der Bewertung der Skalierbarkeit an erster Stelle stehen. Dadurch werden wichtige Diskussionen über zulässige Testzeiten, Zielvorgaben für das Bestehen/Fehlschlagen und Betriebskosten angestoßen. Auch andere oben erwähnte kritische Designkonzepte werden meist in dieser Phase bewertet, um besser zu verstehen, wie die Ausrüstung mit dem zu testenden Gerät (DUT) zusammenarbeitet und welche Anpassungen und Komplexität erforderlich sein könnten.
Ergebnisse der Machbarkeitsstudie für Batterien
Der Kunde, der Elektrofahrzeug- und Hybridbatterien herstellt, konnte die durch die Machbarkeitsstudie erzielten Fortschritte in der Produktentwicklung nutzen, um die Anforderungen an die Messgeräte-Hardware frühzeitig zu bewerten und den Rahmen für die Skalierung auf volle Produktionskapazität zu schaffen. In diesem Beispiel wurde das geeignete Batterie-Impedanzmessgerät mit der gewünschten Messgenauigkeit und Auflösung ausgewählt und die Auswirkungen des gleichzeitigen Testens mehrerer Batteriezellen auf die Produktionszykluszeit bewertet.
Die Machbarkeitsstudie vermittelte ein besseres Verständnis der zur Erreichung der Spezifikationen erforderlichen Prozesstaktzeiten und half dem Unternehmen zu bestimmen, mit welchen Anforderungen an die Produktionsanlagen die Zielmengen erreicht werden können. Mit diesem Ansatz wurden die ersten Meilensteine des Programms früher als geplant erreicht und die Markteinführung beschleunigt, was den gesamten Zeitplan des Programms verkürzte.
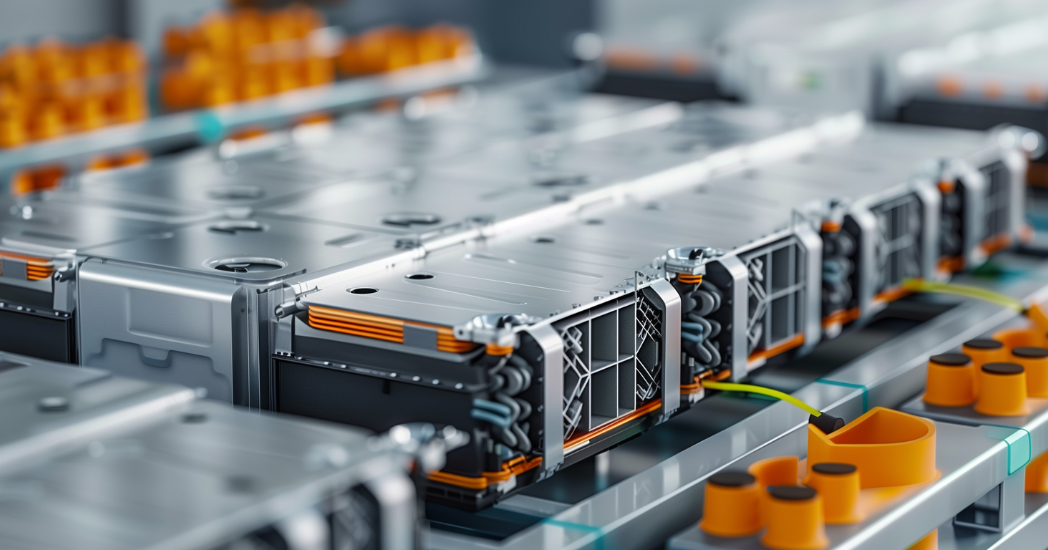
In einem anderen Beispiel wurden bei der Durchführung einer Machbarkeitsstudie die Anforderungen an eine modulare Elektriktestlösung mit geringem Durchsatz ermittelt. Dies ermöglichte eine erste Validierung des Produktdesigns und eine Bestätigung der Spezifikationen. Auf der Grundlage der Ergebnisse der Machbarkeitsstudie wurde die vorgeschlagene Testlösung für eine breite Palette von Produkttypen konzipiert. Dies bietet dem Unternehmen genügend Flexibilität für die Erweiterung der Fähigkeiten mit minimalen Auswirkungen auf das System. Diese Lösung wurde auf ein komplettes Produktionssystem skaliert, um der Fabrik zu helfen, die Marktnachfrage zu erfüllen.
Vorbereitung auf Marktwachstum mit skalierbaren Lösungen
Auf dem Markt für EV-Batterien wird der Wert der Investition in eine Machbarkeitsstudie schnell deutlich, vor allem wenn man die Geschwindigkeit des technologischen Fortschritts, der Entwicklung und der sich ändernden Produktionsmengen berücksichtigt. Die Möglichkeit, die Produktanforderungen zu überprüfen und die Annahmen, auf denen die CAPEX-Investitionen und die Gesamtbetriebskosten (TCO) beruhen, zu validieren oder zu korrigieren, sollte nicht außer Acht gelassen werden.
Mit weltweit steigendem Marktanteil von Elektrofahrzeugen werden die Komplexität und der Umfang von Batteriemontage- und Testprojekten weiter zunehmen. Als Vorbereitung auf das potenzielle Marktwachstum ist es entscheidend, jetzt in Produktionslösungen zu investieren. Die Frage, die Sie sich stellen müssen, lautet: „Welche Werkzeuge können genutzt werden, um das Unternehmen jetzt so zu positionieren, dass es auf die wachsende Marktnachfrage der Zukunft vorbereitet ist und davon profitieren kann?“
Jedes Projekt ist einzigartig. Wir möchten uns Ihre Herausforderungen anhören und Ihnen mitteilen, wie Sie Ihr Projekt durch Machbarkeitsuntersuchungen rechtzeitig auf den Weg bringen können.
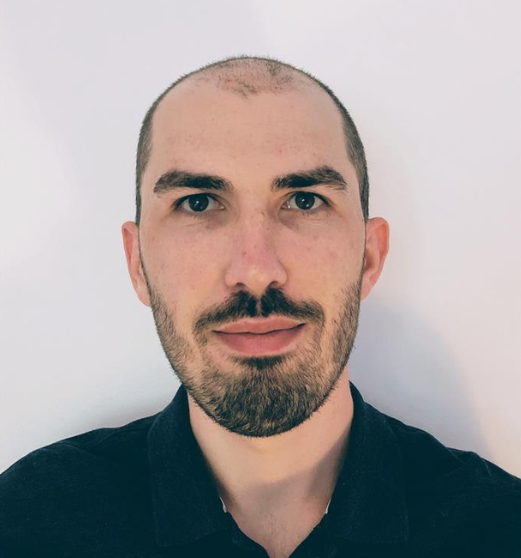
Patrick Tabis
Leiter Anwendungsgruppe
ATS Industrial Automation
Patrick Tabis hilft Unternehmen in zahlreichen Branchen bei der Planung und Umsetzung von Automatisierungsprojekten auf globaler Ebene. Er arbeitet zusammen mit den Kunden an der Optimierung des technischen Designs von Produktionslinien und der Steigerung der betrieblichen Effizienz.