In schnelllebigen Produktionsumgebungen können Stillstandszeiten am Fließband die Effizienz der Produktion, die Zeitpläne, die Rentabilität und die Kundenzufriedenheit beeinträchtigen.
Hersteller, die in Automatisierungsanlagen und Robotertechnik investieren, erwarten, dass die Systeme täglich wie geplant laufen, ohne dass es zu Ausfällen kommt. Das ist jedoch nicht immer der Fall. Unabhängig davon, ob Sie sich in der Anfangsphase der Implementierung von Montageautomation befinden oder eine seit langem etablierte Produktionslinie verwalten, ist es für einen reibungslosen Betrieb entscheidend, die Hauptursachen für Stillstandszeiten von Maschinen zu kennen und zu wissen, wie man sie verhindern kann.
Häufige Ursachen für außerplanmäßige Stillstandszeiten von Maschinen
Falsch eingelegte Teile oder nicht den Spezifikationen entsprechende Komponenten: Automatisierte Montagemaschinen arbeiten innerhalb strenger Parameter. Wenn Teile falsch eingelegt werden oder Komponenten nicht den Spezifikationen entsprechen, kann sich die Anlage abschalten, um Schäden oder Fehlfunktionen zu vermeiden.
Verschleiß: Selbst die modernsten Maschinen nutzen sich mit der Zeit ab. Die Werkzeuge werden schmutzig, die Schmiermittel trocknen aus, und die Komponenten verschleißen allmählich. Dies kann sich auf die Leistung der Maschinen auswirken und dazu führen, dass die Produktionslinien langsamer werden oder stehen bleiben, was wiederum zu einem geringeren Ertrag führt.
Unerfahrenes Bedienpersonal oder nicht ausreichende Schulung: Wenn das Bedienpersonal nicht ausreichend geschult ist, dauert die Reparatur der Geräte bei Störungen länger. Dies ist besonders häufig der Fall, wenn neues, weniger erfahrenes Bedienpersonal die Maschine übernimmt oder das Team, das die Maschine ursprünglich erhalten hat, das Unternehmen verlässt. Ohne eine angemessene Schulung des Bedienpersonals kann es auch bei gut funktionierenden Maschinen zu häufigen Abschaltungen kommen.
Engpässe und Probleme mit der Maschinenleistung: Manchmal verursacht eine einzelne Station in der Fertigungslinie Verzögerungen durch unzureichend funktionierende Geräte oder langsamere manuelle Vorgänge, was zu Engpässen in der gesamten Linie führt. Wenn Probleme nicht frühzeitig erkannt werden, kann dies zu erheblichen Stillstandszeiten führen, bevor die eigentliche Ursache gefunden ist.
Neben diesen häufigen Ursachen für Stillstandszeiten bei Maschinen können auch andere Faktoren – wie die Verwendung der falschen Automatisierungsausrüstung für die Aufgabe, nicht spezifikationsgerechte Teile, die in die Maschine eingelegt werden, Umweltbedingungen oder Störungen in der Lieferkette – die Betriebszeit der Produktion beeinträchtigen. Obwohl jede Produktionslinie ihre eigenen Herausforderungen hat, ist der erste Schritt zur Verringerung von Stillstandszeiten und zur Vorbeugung künftiger Unterbrechungen das Verständnis der Grundursachen.
5 Tipps zur Vermeidung von Verzögerungen bei Ausrüstung und Fließband
Mit mehr als 45 Jahren Erfahrung in der Entwicklung fortschrittlicher automatisierter Fertigungssysteme weiß ATS Industrial Automation, worauf es ankommt, damit automatisierte Systeme mit höchster Leistung laufen.
Wir haben Hochgeschwindigkeits-Montagelinien und Automatisierungssysteme für verschiedene Branchen entwickelt und ausgeliefert, z. B. für die Automobilbranche, Batterien für Elektrofahrzeuge, Elektronik, Konsumgüter, langlebige Güter, Logistik und mehr. Mit mehr als 3 000 ausgelieferten und in Betrieb befindlichen Anlagen geben wir Ihnen hier unsere fünf Tipps zur Vermeidung von Stillstandszeiten:
1. Umsetzung eines strengen Programms zur vorbeugenden Wartung
Eine gut geplante vorbeugende Wartung gehört zu den effektivsten Methoden zur Vermeidung unerwarteter Stillstandszeiten. Dazu gehört die regelmäßige Überprüfung von Verschleißteilen (Berührungswerkzeuge, Lager, Riemen, Motoren usw.), die ausgetauscht werden müssen, die Reinigung kritischer Bereiche, in denen sich Staub oder Schmutz ansammeln kann, die Schmierung beweglicher Teile, um Reibung und Verschleiß zu verringern, und Maschineninspektionen, um frühe Anzeichen von Ausfällen zu erkennen.
Bei ATS Industrial Automation bieten wir maßgeschneiderte Wartungs- und Servicepläne an, um den effizienten Betrieb von Montagemaschinen zu gewährleisten. Dies reicht von Inspektionen vor Ort bis hin zur Entwicklung von Schulungsmaterialien, Videos und Wartungsplänen, um die langfristige Funktionsfähigkeit der Anlagen sicherzustellen.
2. Einsatz fortschrittlicher Tools zur Produktionsüberwachung
Tools zur Echtzeitüberwachung wie die Illuminate™ Manufacturing Intelligence Software bieten sofortige Einblicke in die Leistung der Anlagen. Sie verfolgt Betriebszeit, Verfügbarkeit und Erträge und hilft Teams, Engpässe, langsame Maschinen oder leistungsschwache Stationen zu erkennen.
Illuminate vereinfacht die Datenerfassung und -analyse und erstellt detaillierte Berichte über Störungen, Stillstandszeiten und Maschineneffizienz. Die Software hilft auch bei der Verfolgung von Leistungstrends und erleichtert so die Vorhersage und Vorbeugung künftiger Probleme. Das Ergebnis ist eine effizientere Fertigungslinie, eine höhere Maschinenzuverlässigkeit und weniger Betriebsunterbrechungen.
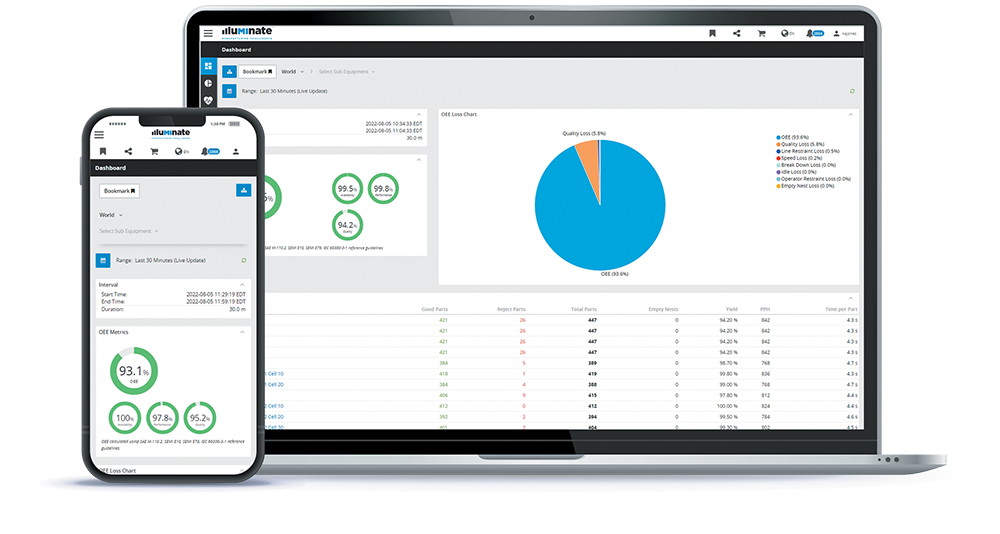
3. Investition in umfassende Schulungen des Bedienpersonals
Ausreichende Schulungen sorgen dafür, dass das für die Bedienung und Wartung der Geräte zuständige Personal die Geräte richtig bedienen und kleinere Probleme beheben kann, bevor sie zu größeren Verzögerungen führen.
Die meisten Unternehmen führen Schulungen zum Zeitpunkt der Anschaffung neuer Montagemaschinen durch. Die Schulungen sollten jedoch kontinuierlich erfolgen. Wenn neues Bedienpersonal eingestellt wird, sollte es die gleiche gründliche Schulung erhalten wie das Team, das die Anlage ursprünglich erhalten hat. Und erfahrenes Bedienpersonal kann von Auffrischungskursen profitieren, um bei Systemaktualisierungen auf dem Laufenden zu bleiben.
Wir bieten umfangreiche Schulungsprogramme an, darunter Schulungen vor Ort, Schulungsunterlagen und Simulationen in virtueller Realität. Mit unserer UReality-Software können Unternehmen innerhalb von Minuten immersive 3D-Schulungssimulationen erstellen und diese team- und standortübergreifend nutzen. Dies ist eine kosteneffiziente Möglichkeit, neues Personal an Bord zu holen oder vorhandene Fähigkeiten mit interaktiven Lernmethoden zu verbessern.
4. Regelmäßige Systemaudits
Über die vorbeugende Wartung hinaus sind regelmäßige Systemaudits ein proaktiver Weg zur Erkennung von Problemen, bevor sie die Produktion verlangsamen. Unsere Fachleute können Zustandsprüfungen an Maschinen durchführen und mit Geräten wie Debug-Kameras Echtzeitaufnahmen von Fehlfunktionen machen. Unser Technikpersonal kann das Filmmaterial auswerten und Probleme, die die Maschinenleistung beeinträchtigen, schnell erkennen und beheben.
5. Aufrüstungen einplanen
Automatisierungs- und Produktionsanlagen müssen sich mit der Zeit weiterentwickeln. Wenn neue Produkte/Teile eingeführt werden oder sich das Produktionsvolumen ändert, reicht die ursprüngliche Ausrüstung möglicherweise nicht mehr für die neue Belastung aus. Die Aufrüstung von Maschinen oder das Hinzufügen neuer Funktionen kann die Leistung verbessern und Stillstandszeiten reduzieren.
Wir bieten Aufrüstungen der Anlagen an, um sie an neue Produkte anzupassen oder die Effizienz zu steigern, damit die Systeme über ihre gesamte Lebensdauer flexibel und widerstandsfähig bleiben.
Maximierung der Betriebszeit
Stillstandszeiten von Fließbändern und Maschinen können kostspielig sein, sind mit den richtigen Strategien aber vermeidbar. Vorbeugende Wartung, moderne Überwachungsinstrumente und gründliche Schulung sind der Schlüssel. Wenn Sie proaktiv vorgehen und potenzielle Probleme angehen, bevor sie entstehen, ist sichergestellt, wird Ihr Fließband auch weiterhin reibungslos funktionieren. Mit dem richtigen Ansatz, den richtigen Werkzeugen und dem richtigen Partner können Sie die Lebensdauer Ihrer Anlagen erheblich verlängern und die Gesamteffizienz Ihrer Produktion maximieren.
Stillstandszeiten von Montagelinien
Ursachen für Stillstandszeiten von Maschinen | Lösungen |
---|---|
Falsch eingelegte Teile | Schulungen und VR-Simulationen für Bedienpersonal |
Teile entsprechen nicht den Spezifikationen der Maschine | Aufrüstungen einplanen |
Maschinenverschleiß | Produktionsüberwachung, vorbeugende Wartung und Systemaudits |
Verschmutzte Zuführanlagen und Kontaktwerkzeuge | Programm zur vorbeugenden Wartung |
Unerfahrenes Bedienpersonal | Umfassende Schulung des Bedienpersonals |
Unzureichend funktionierende Geräte | Produktionsüberwachung und Systemaudits |
Langsame manuelle Vorgänge | Schulung des Bedienpersonals und Systemaudits |
Austausch der Linien für neue Produkte | Aufrüstungen und Bedienpersonalschulungen planen |
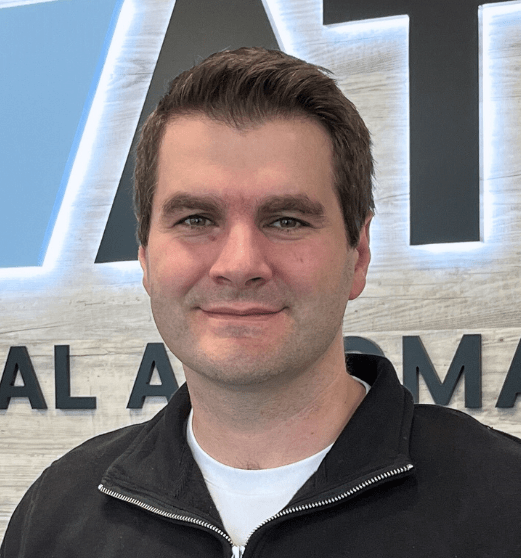
Ken Aarts
Manager, Controls Engineering
ATS Industrial Automation
Ken hat Unternehmen in zahlreichen Branchen bei der Automatisierung und Optimierung ihrer Montage- und Testlinien geholfen. Er hat sich auf die Konfiguration von Steuerungssystemen zur Erweiterung und Optimierung von Produktionslinien und zur Steigerung der betrieblichen Effizienz spezialisiert.