Mit einem robusten Design und bewährten Herstellungsprinzipien werden zylindrische Batteriezellen häufig in Anwendungsbereichen mit hoher Energiedichte eingesetzt, von Elektrofahrzeugen (EVs) bis hin zu Laptops und anderen tragbaren Geräten . Bekannt für ihre Zuverlässigkeit, Effizienz und Vielseitigkeit sind zylindrische Batterien zu einer kritischen Komponente in netzgebundenen Energiespeichersystemen (BESS) geworden.
Was diese Zellen von anderen Batterietypen unterscheidet, ist ihre feste zylindrische Bauart, die effizientes Packen und Kühlen ermöglicht. Dieses Design verbessert nicht nur die Leistung, sondern bietet auch mechanische Stabilität und Sicherheit. Darüber hinaus gewährleisten ihre Haltbarkeit und langen Lebenszyklen eine zuverlässige Energieverwaltung.
Bei ATS Industrial Automation haben wir über 110 EV-Batteriemontage- und Testlinien geliefert und verstehen die Herausforderungen bei der Konstruktion und Skalierung von Batteriemontagelinien für zylindrische, Pouch- und prismatische Batterien.
Herausforderungen bei der Montage zylindrischer Batterien
Die Handhabung und Verwendung zylindrischer Zellen in der Batteriefertigung stellt mehrere Herausforderungen dar.
- Präzises Schweißen: Verhindert das Eindringen in die äußere Hülle der Zellen, wodurch Elektrolytlecks und potenzielle Sicherheitsrisiken vermieden werden.
- Materialhandling: Beim Umgang mit Materialien ist Vorsicht geboten, um Schäden an freiliegenden Anschlüssen während der Montage und des Testens zu vermeiden. Außerdem sind aufgrund der kleineren Bauform in der Regel viel mehr zylindrische als prismatische oder flache Zellen in einem Fahrzeug vorhanden. Dies erfordert wiederum eine viel schnellere Materialhandhabung, um die Produktionsrate des E-Fahrzeugs zu erreichen.
- Thermisches Management: Die ordnungsgemäße Kühlung der Zellen muss sorgfältig berücksichtigt werden, da die zylindrische Form es schwierig macht, ein gleichmäßiges thermisches Management zu erreichen.
- Variabilität bei den Maßen: Selbst relativ kleine Abweichungen bei den Maßen der Zellen können den Montageprozess erschweren und erfordern eine strenge Qualitätskontrolle.
Trotz dieser Herausforderungen bleiben zylindrische Zellen aufgrund ihrer Robustheit und hohen Energiedichte beliebt. Dies macht sie für Anwendungsbereiche wie Elektrofahrzeuge geeignet, da die hohe Energiedichte eine längere Reichweite zwischen den Ladevorgängen ermöglicht.
Montage von zylindrischen Zellen zu Batterien
Validierung eingehender Zellen
Der Prozess der Montage der zylindrischen Batterie beginnt mit der Validierung eingehender Zellen, um durch Inspektionen und Tests sicherzustellen, dass sie die erforderlichen Fertigungsspezifikationen erfüllen.
- Physische Inspektion: Überprüfung auf physische Defekte, wie Beulen, Kratzer oder andere sichtbare Schäden, die die Unversehrtheit der Zelle beeinträchtigen könnten.
- Überprüfung der Maße: Vermessung der Zellenmaße, um sicherzustellen, dass sie den angegebenen Toleranzen entsprechen.
- Elektrische Tests: Bewertung der Kapazität, Spannung und des Innenwiderstands der Zelle durch Leerlaufspannungstests (OCV) und einen Wechselstrom-Innenwiderstandstest (ACIR).
- Sortieren: Kategorisieren von Zellen, die alle Validierungstests bestehen und zum nächsten Montageschritt übergehen, während andere zur weiteren Analyse oder Ablehnung beiseite gelegt werden.
- Barcode-Prüfung: Ein weiteres wichtiges Inspektionskriterium ist die Nachverfolgung jeder Zelle, um für jedes EV-Batteriepack ein vollständiges Herkunftsdokument zu erstellen.
Zuordnung der Zellen zu einem Träger
Sobald die Zellen die Validierung bestanden haben, werden sie einem Träger zugeordnet. Abhängig vom jeweiligen Batteriemontageprozess des Herstellers können zylindrische Zellen durch einen Auftragen oder Aufkleben an einem Träger befestigt werden. Dabei werden die Zellen durch Verkleben fest am Träger angebracht.
Aufbau einer elektrischen Anordnung und Validierung
Nachdem die Zellen sicher befestigt sind, besteht der erste Schritt im Aufbau der elektrischen Anordnung. Dieser Schritt umfasst das Schweißen einer Sammelschienenstruktur, wobei die Zellen miteinander verbunden und zu Gruppen zusammengefasst werden, um die erforderliche Spannung und Stromstärke zu erreichen. Die Sammelschienen sind wesentliche Komponenten, die die einzelnen Zellen elektrisch verbinden, damit sie als eine Einheit zusammenwirken können.
Anschließend wird eine Kühlplatte an das Modul angebracht, um die während des Betriebs entstehende Wärme zu regulieren. Die Kühlplatte sorgt dafür, dass die Batterie innerhalb sicherer Temperaturgrenzen arbeitet, um Leistung und Langlebigkeit zu erhalten. Zwischen den Zellen und der Kühlplatte wird Wärmeleitmaterial (Thermal Interface Material, TIM) aufgebracht, was die Wärmeableitung verbessert und als Wärmequelle und Kühlsystem zugleich eine starke thermische Leitung zwischen den Zellen gewährleistet.
Modultests
Schließlich wird das Modul geschlossen und daraufhin getestet, dass alle elektrischen Verbindungen sicher sind und die Zellen korrekt funktionieren. Modultests zylindrischer Zellen umfassen:
- Schweißwiderstand
- Leerlaufspannung (OCV)
- Temperatur
- Stromkalibrierung
- Gleichstrom-Innenwiderstand (DCIR)
- Laden/Entladen
- HiPot-Test (High Potential)
- Dichtheitstests
Diese Tests gewährleisten die Zuverlässigkeit und Effizienz zylindrischer Batteriemodule für Hochleistungsanwendungen wie BESS – große, wiederaufladbare Batterien, die erneuerbare und nicht erneuerbare Energie für die spätere Nutzung speichern – und Elektrofahrzeuge.
Pack-Montage
Das Batteriepaket wird durch das Sammeln mehrerer Module, das Hinzufügen eines Batteriemanagementsystems (BMS) und eines Kühlsystems gebildet. Module sind in Reihe oder parallel angeordnet, je nach gewünschter Spannung, Kapazität oder Leistungsdichte. Ähnlich wie bei der Modulmontage umfasst der Packungsprozess strenge Qualitätskontrolltests, um die Leistung zu validieren, wie OCV, BMS, Fahrzeugumweltsimulation und Dichtheit.
Überwindung von Herausforderungen bei der Montage und dem Testen zylindrischer Batterien
Zylindrische Batterien spielen eine entscheidende Rolle in der Batterielandschaft, da sie Langlebigkeit, Effizienz und Anpassungsfähigkeit in Anwendungsbereichen wie Elektrofahrzeugen und Netzspeichern bieten. Obwohl ihre Montage und Handhabung einige Herausforderungen mit sich bringen, machen die Vorteile einer verbesserten Wärmeregulierung und längerer Lebenszyklen sie zur ersten Wahl für viele Batteriehersteller.
Durch die Einhaltung strenger Qualitätskontrollmaßnahmen, die Nutzung fortschrittlicher Technologien und die Auswahl des richtigen Partners für Batteriemontage und -tests können Hersteller qualitativ hochwertige zylindrische Batteriemodule produzieren, die den Anforderungen moderner Energiespeicheranwendungen entsprechen. Die Einbindung eines Automatisierungspartners mit Erfahrung sowohl in der Montage als auch im Testen kann die Implementierung optimieren und OEMs eine nahtlos integrierte Lösung bieten, die qualitativ hochwertige und volumenstarke Durchsätze fördert.
Bei ATS Industrial Automation stehen wir an der Spitze der Batteriemodul- und Packmontage. Unser Team von Montage- und Testexperten ist bereit, Ihre Anforderungen für den gesamten Prozess der Batterieproduktion zu unterstützen. Kontaktieren Sie uns noch heute, um Ihr Projekt zu besprechen.
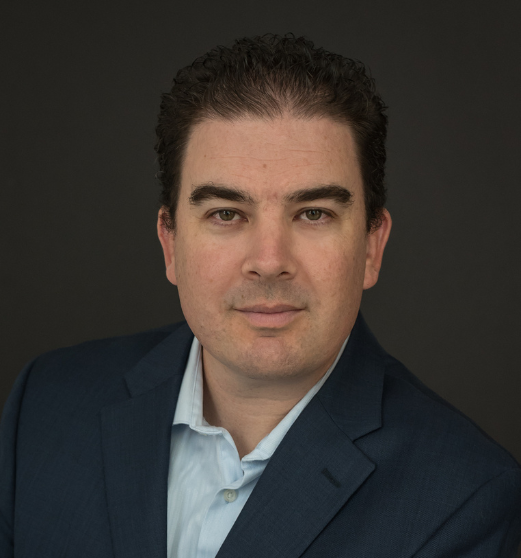
Cameron Bruce
Direktor für Ingenieurwesen
ATS Industrial Automation
Cameron arbeitet mit Kunden zusammen, um durch Entwicklung und Optimierung von Automatisierungssystemen die Produktion zu erweitern und die Betriebseffizienz zu steigern. Cameron hilft seit über 18 Jahren Unternehmen aus zahlreichen Branchen dabei, die Produktion zu automatisieren und zu optimieren.