Pouch-Zellen sind eine beliebte Wahl bei Batterieherstellern. Das liegt daran, dass die Zelle hoch effizient ist und eine Verpackungseffizienz von 90–95 % erreicht, eine der höchsten unter den Batteriepaketen. Diese Zellen werden oft zur Herstellung von Batterien für Elektrofahrzeuge (EVs) verwendet, können aber auch in Unterhaltungselektronik wie Mobiltelefonen und Tablets oder in kleinen Geräten wie Drohnen eingesetzt werden. Pouch-Zellen unterscheiden sich von zylindrischen oder prismatischen Zellen durch ihr flexibles und leichtes Design. Dies ermöglicht eine höhere Energiedichte und eine bessere Raumausnutzung als bei zylindrischen Zellen.
Die Montage und Prüfung von Pouch-Zellen stellt jedoch eigene Herausforderungen dar, von der empfindlichen, flexiblen Struktur der Zellen bis hin zu ihrer Empfindlichkeit gegenüber hohen Temperaturen. Durch sorgfältige Handhabung, frühe Validierung, präzises Schweißen und Qualitätskontrollen können Batteriefabrikanten die Leistung ihrer Produkte jetzt und in Zukunft sicherstellen.
Häufige Herausforderungen bei der Montage und Prüfung von Pouch-Batterien
Der Zusammenbau von Beutelbatterien stellt mehrere einzigartige Herausforderungen dar, die eine sorgfältige Handhabung und spezielle Verfahren erfordern, um ihre Zuverlässigkeit zu gewährleisten. Zu diesen Herausforderungen gehören:
- Zerbrechlichkeit: Pouch-Zellen sind äußerst empfindlich und besitzen nicht die inhärente dimensionale Stabilität zylindrischer oder prismatischer Batteriezellen. Diese geschichteten Batterien sind in eine flexible Folie eingeschlossen – ein Material, das deutlich weniger robust ist als die starren Gehäuse anderer Zelltypen. Infolgedessen sind Pouch-Zellen wesentlich anfälliger für Beschädigungen während der Handhabung und Montage. Selbst geringer Druck oder unsachgemäße Berührung kann zu internen Schäden führen, was ihre Leistung beeinträchtigt oder sogar ein Sicherheitsrisiko darstellt.
- Materialhandling:Das Materialhandling von Pouch-Zellen erfordert besondere Sorgfalt und angepasste Techniken, um Beschädigungen zu verhindern. Da diese Batterien keine starren Gehäuse besitzen, sind sie anfällig für Verformungen oder Belastungen. Um die empfindlichen Zellen sicher zu manipulieren und insbesondere eine Verformung der Folienschweißnähte oder eine übermäßige Belastung der empfindlichen Anschlusstabs zu vermeiden, kommt häufig das Vakuumhandling zum Einsatz. Diese Methode gewährleistet einen schonenden und präzisen Griff, der die Zellintegrität bewahrt.
- Laschenhandling: Die Schnittstelle zwischen der Lasche und den Zellinnenteilen ist ebenfalls fragil. Hersteller müssen beim Biegen oder Formen der Laschen vorsichtig sein, um Schäden oder Belastungen zu vermeiden.
- Kompression:Während des Kompressionsprozesses werden Pouch-Zellen einem kontrollierten Druck ausgesetzt. Das ist entscheidend, damit die Zellen flach und gleichmäßig bleiben. Diese Kompression ist unverzichtbar für die Leistung und Langlebigkeit der Batterien. Sie hilft, Luftspalte oder Unregelmäßigkeiten innerhalb der Zellschichten zu eliminieren, die andernfalls die Effizienz und Stabilität der Zellen negativ beeinflussen könnten. Durch diesen präzisen Schritt wird eine optimale interne Struktur gewährleistet, die für die zuverlässige Funktion der Batterie unerlässlich ist.
- Schweißen und Verbinden: Stabile elektrische Schweißverbindungen sind für die Funktion und Sicherheit von Pouch-Batterien unerlässlich. Doch dieser Prozess ist hochsensibel, da die Bereiche, an denen die Schweißung erfolgen muss, extrem empfindlich sind.
- Es erfordert absolute Präzision, die richtige Balance zu finden:
- Zu viel Schweißleistung: Die dünnen Laschen der Pouch-Zellen können schnell durchdrungen und das darunterliegende Substratmaterial beschädigt werden. Dies gefährdet die Zellintegrität und kann zu internen Kurzschlüssen führen.
- Zu wenig Schweißleistung: Die Verbindung formt sich nicht korrekt, was zu einem erhöhten Widerstand, Leistungseinbußen oder sogar einem vollständigen Ausfall der Verbindung führen kann.
- Dieser kritische Prozess erfordert daher nicht nur höchste Präzision, sondern auch umfassende Tests, um die Unversehrtheit der Zelle zu gewährleisten und langfristige Zuverlässigkeit sicherzustellen.
Schritte und Überlegungen zur Montage von Pouch-Batterien
Validierung für eingehende Pouch-Zellen
Der erste Schritt bei der Pouch-Montage ist die Validierung eingehender Zellen. Dieser Schritt gewährleistet die Qualität und Zuverlässigkeit der Zellen, bevor sie in weitere Montagephasen übergehen. Die Zellvalidierung umfasst eine Reihe von Inspektionen und Tests, um zu überprüfen, ob die Zellen die erforderlichen Spezifikationen und Standards erfüllen.
Kritische Aspekte der Validierung eingehender Zellen umfassen:
- Überprüfung auf physische Defekte.
- Messung der Zellengröße.
- Durchführung elektrischer Tests zur Beurteilung der Kapazität, Spannung und des Innenwiderstands der Zelle.
Durch die Validierung eingehender Zellen können Batteriehersteller Probleme frühzeitig erkennen und beheben. Dies kann das Risiko von Defekten in nachfolgenden Prozessen verringern und die Gesamtleistung und Sicherheit des endgültigen Batteriepacks verbessern.
Zuschneiden und Formen der Pouch-Zell-Laschen
Das Zuschneiden und Formen der Laschen ist ein absolut entscheidender Schritt, damit diese im weiteren Montageprozess die erforderlichen Spezifikationen und Parameter präzise erfüllen. Wird dieser kritische Prozess nicht ordnungsgemäß ausgeführt, erhöht sich das Risiko eines thermischen Durchgehens erheblich.
Fehlerhafte oder ungenau geformte Laschen können zu schlechten elektrischen Verbindungen und physischen Schäden während der späteren Montageschritte führen. Diese Risiken bergen erhebliche Sicherheitsbedenken, die es unbedingt zu vermeiden gilt.
In diesem Prozess werden die aus der Pouch-Zelle ragenden Laschen sorgfältig auf die exakte Länge und Form zugeschnitten, um höchste Qualität und Sicherheit zu gewährleisten.
Dann folgt der Formungsschritt, bei dem die Laschen gebogen oder geformt werden, um den spezifischen Designanforderungen der Batterie gerecht zu werden. Präzision ist in dieser Phase entscheidend, um Schäden an der empfindlichen Schnittstelle zwischen der Lasche und dem Zellinneren zu vermeiden. Richtiges Zuschneiden und Formen der Laschen gewährleistet zudem die Leistung und Zuverlässigkeit der Zelle, stabilisiert elektrische Verbindungen und minimiert das Risiko mechanischer Belastungen oder Schäden.
Sequenzieren und Stapeln von Pouch-Zellen
Das Sequenzieren und Stapeln von Pouch-Zellen ist ein entscheidender Schritt, besonders für Anwendungen wie Elektrofahrzeuge.
Sequenzieren ordnet die Zellen in einer spezifischen Reihenfolge an, um die Leistung und den Ausgleich im gesamten Batteriepack zu optimieren.
Stapeln beinhaltet das sorgfältige Ausrichten und Schichten der Zellen. Dies minimiert Fehlstellungen und sichert korrekte, zuverlässige Zellverbindungen, was für die Effizienz und Sicherheit des Batteriepacks unerlässlich ist.
Kompression von Pouch-Zellen
Die Kompression bewahrt die Form und Unversehrtheit von Pouch-Zellen. Während dieses Schrittes werden die Zellen einem kontrollierten Druck ausgesetzt, um sicherzustellen, dass sie flach und gleichmäßig bleiben. Häufig wird zwischen den Zellen eine Klebe- und Kompressionsabsorptionsschicht aufgebracht, um sie an Ort und Stelle zu sichern und die richtige Ausrichtung während des Kompressionsprozesses zu gewährleisten.
Um jedoch Schäden an den Zellen zu vermeiden, müssen Hersteller während der Kompression die Variablen wie der angewendete Druck und die Dauer des Prozesses sorgfältig handhaben. Richtige Kompressionstechniken stellen sicher, dass die Pouch-Zellen die erforderlichen Standards erfüllen.
Montage von Pouch-Zell-Sammelschienen und Laschenformung
In der Modulphase beinhaltet das Herstellen elektrischer Verbindungen für Pouch-Zellen die Nutzung von Sammelschienen, um stabile und zuverlässige Verbindungen zwischen den Zellen zu schaffen. Dieser Prozess stellt sicher, dass die Zellen als Einheit funktionieren. Serienverbinder verbinden mehrere Zellen miteinander, um die gewünschte Spannung des Batteriemoduls zu erhalten.
Schweißen von Pouch-Zell-Sammelschienen
Sammelschienen werden typischerweise an die Laschen der Pouch-Zellen geschweißt oder geklebt, um eine sichere und stabile elektrische Verbindung zu gewährleisten. Während der Sammelschienenmontage werden die Laschen der Pouch-Zellen sorgfältig gebogen oder geformt, um den spezifischen Designanforderungen des Batteriepakets gerecht zu werden. Eine korrekte Ausrichtung und sichere Verbindung der Sammelschienen minimiert das Risiko von mechanischen Belastungen oder Beschädigungen und gewährleistet Leistung und Zuverlässigkeit.
Präzision beim Schweißen hilft Batterieherstellern auch, die Unversehrtheit der Zellen und langlebige Verbindungen zu gewährleisten. Der Schweißprozess muss sorgfältig gesteuert werden, um Schäden an der empfindlichen Schnittstelle zwischen der Lasche und dem Zellinneren zu vermeiden.
Überlegungen zur Verteilung von Wärmeleitmaterial und zu Kühlplatten
Das Management der von den Pouch-Zellen während des Betriebs erzeugten Wärme erhöht die Langlebigkeit der Batterie. Das Auftragen von Wärmeleitmaterial (TIM) und Kühlplatten ist eine gängige Lösung. Wärmeleitmaterial zwischen den Zellen und Kühlplatten verbessert die Wärmeleitfähigkeit und Wärmeableitung. Eine ordnungsgemäße Verteilung sorgt für gleichmäßige Abdeckung und verhindert Luftspalten, die zu Hotspots und Leistungsabfall führen können.
Kühlplatten, die häufig aus Materialien mit hoher Wärmeleitfähigkeit bestehen, sorgen für eine gleichmäßige Wärmeverteilung über die Pouch-Zellen. Die Hersteller müssen diese Kühlplatten sorgfältig entwerfen und platzieren, damit sie die thermische Belastung effektiv bewältigen, ohne das Batteriemodul durch übermäßiges Gewicht oder Volumen zu belasten.
Qualitätsprüfungen der Batteriemontage und Batteriepackmontage
Die letzte Phase der Pouch-Montage umfasst eine Reihe von strengen Prüfungen und Tests, um sicherzustellen, dass die Module den erforderlichen Spezifikationen und Standards entsprechen, bevor sie zur weiteren Qualitätsprüfung in das Pack eingebracht werden.
Zu den wichtigsten Aspekten dieser Qualitätsprüfungen gehören:
- Sichtprüfungen auf physische Defekte.
- Gründliche Prüfungen der Schweißnahtqualität.
- Elektrische Prüfungen zur Bewertung der Kapazität.
- Spannung und Innenwiderstand.
- Thermische Bewertungen, um ein ordnungsgemäßes Wärmemanagement sicherzustellen.
Durch gründliche Qualitätskontrollen können Batteriehersteller Probleme angehen, bevor die Batterien eingesetzt werden, und so die Sicherheit und Effizienz des Endprodukts gewährleisten. Oftmals verfügen Batterie-Fertigungslinien über sowohl prozessinterne (Inline-) als auch am Prozessende stattfindende (End-of-Line-)Tests. Inline-Tests helfen, Ausschussteile zu reduzieren und Prozessschritte zu identifizieren, die verbessert werden müssen. End-of-Line-Tests konzentrieren sich darauf, dass nur Batterien bester Qualität im Endprodukt verwendet werden.
Beschickung der Pouch-Montage- und Testlinien
Die Montage und Prüfung von Pouch-Zellen sind komplexe Prozesse, die genaue Aufmerksamkeit für Details und präzise Handhabung erfordern. Von der Validierung der eingehenden Zellen bis zu den abschließenden Qualitätsprüfungen spielt jeder Schritt eine entscheidende Rolle bei der Sicherstellung der Zuverlässigkeit und Leistung der Batterie.
Durch die Zusammenarbeit mit einem Automatisierungspartner, der die Herausforderungen und Überlegungen bei der Montage und Prüfung von Batterien unter Verwendung von Pouch-Zellen versteht, können Batteriehersteller ihre Prozesse frühzeitig optimieren und höherwertige Batterien produzieren, die den Anforderungen schnell fortschreitender Technologien gerecht werden.
Jedes Batterieprojekt ist einzigartig. Wir möchten uns Ihre Herausforderungen anhören und Ihnen mitteilen, wie Sie Ihr Projekt durch Automatisierung rechtzeitig auf den Weg bringen können.
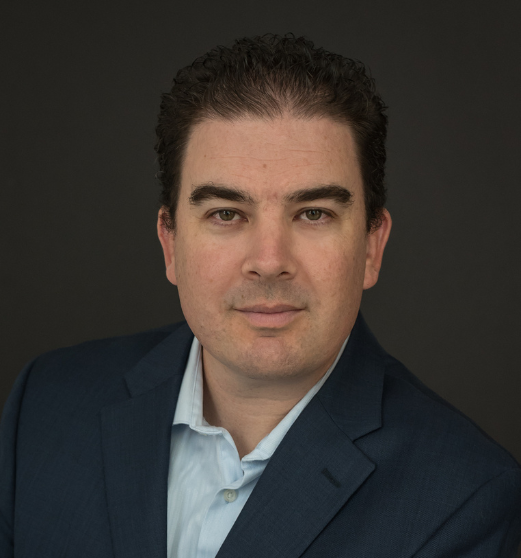
Cameron Bruce
Direktor für Ingenieurwesen
ATS Industrial Automation
Cameron arbeitet mit Kunden zusammen, um durch Entwicklung und Optimierung von Automatisierungssystemen die Produktion zu erweitern und die Betriebseffizienz zu steigern. Cameron hilft seit über 18 Jahren Unternehmen aus zahlreichen Branchen dabei, die Produktion zu automatisieren und zu optimieren.